The main production equipment for producing masterbatch is a twin-screw extruder. The common production process is: pre-mixing.ingredient mixing, extrusion, cooling, cutting, and packaging. Appearance defects are a quality problem for masterbatch products, mostly related to production processes, raw material quality, production equipment, and production environment factors. Common defects include elongated particles, agglomerations, black spots, discoloration, vacuum defects, iron filings, poor plasticization, and carbonization, Uneven particle size, Color Difference, etc.
Table of Contents
ToggleElongated Particles
Particles that are more than twice the normal size are considered elongated particles. The main causes are starting with elongated particles or broken pieces, non-linear direction of the material strips, and wear and tear or gaps in the cutting machine.
Solutions:
- Adjust the direction of the material strips entering the cutting machine and adjust the length of the water flow during normal production.
- Adjust the production process to address broken material strips.
- Pay attention to the cutting blade of the cutting machine and replace damaged ones in a timely manner.
- Use an appropriate vibrating sieve to filter out elongated particles.

Agglomerations
Two or more particles that are connected side by side are called agglomerations. The main causes are broken material strips or insufficient water flow. The spacing of Die is too small, and the rotary speed of cutter blades is too low
Solutions:
- Use an appropriate guide wheel width when extruding material strips to separate them.
- Adjust the appropriate cooling water flow to reduce agglomerations.
- Use an appropriate vibrating sieve to filter out agglomerations.
- Replace the hot die template with a larger space distance
- Increase the rotary speed of the hot cutting blades, to increase the centrifugal force, and quickly throw the particles into the cooling medium to avoid secondary adhesion.
Black Spots
Black spots are black spots on the surface or inside of particles. The main causes of black spots are unclean cleaning after production, black spots in raw materials, screw carbonization, environmental pollution, and Carbon black agglomeration of the black master batch.
Solutions:
- If the cleaning process during production changeover is not clean, clean it again.
- Strengthen material inspection, especially for fillers or flame retardants that are prone to black spots or impurities.
- Pay attention to controlling and adjusting the screw temperature and the residence time of materials in the screw to prevent excessive processing temperature.
- Pay attention to the environmental hygiene around the production area and isolate and protect different colored products from each other.
- The problem of black spots in the black master batch requires readjusting the screw combination and improving the plasticizing ability and dispersion ability of the screw.
Discoloration
Discoloration occurs when the product’s color suddenly changes during production, resulting in an obvious color difference. The main causes are uneven mixing, unclean cleaning, excessive temperature, and excessive shear.
Solutions:
- Strictly follow the mixing process to ensure uniform mixing.
- Inspect the cleaning process to ensure it is clean.
- Control the extrusion temperature to prevent excessive temperature that can cause colorants to decompose.
- Choose an appropriate screw combination to avoid too much shear.
Uneven particle size
The main reason for the uneven particle size comes from the change of head pressure, or the uneven plasticization of the raw materials, resulting in the blockage of the changer filter or die hole.
Solution:
- Check whether the pressure sensor is damaged
- Replace the new changer/filter
- Adjust screw combination to improve plasticizing ability
- Clean up the blocked die head and properly raise the die head to help the flow of materials.
Color Difference
There are many reasons for the color difference, which may be the color masterbatch formula, the change of the process, the change of the auxiliary agent, the change of the equipment temperature, and the screw cleaning is not clean, etc.
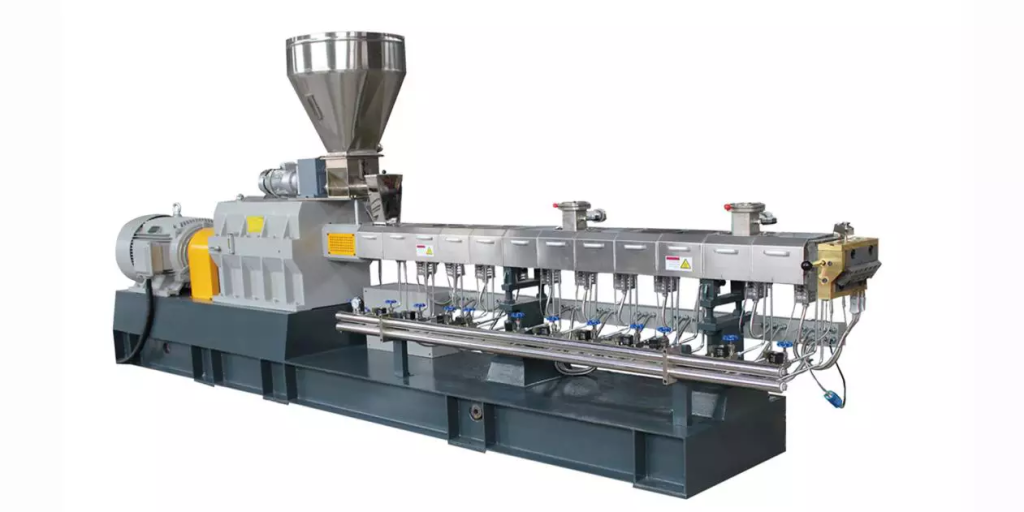
Solution:
- Carefully check the raw material manufacturers and ratios of the mixing formula with the changed manufacturers compared with the previous ones, and change the proportion of addition.
- Thoroughly clean the screw, barrel and Die head.
- Check whether the cylinder barrel cooling is blocked and whether the temperature control is out of control.
- Homogenized product silos are used to stir masterbatches produced at various time periods to minimize color difference.
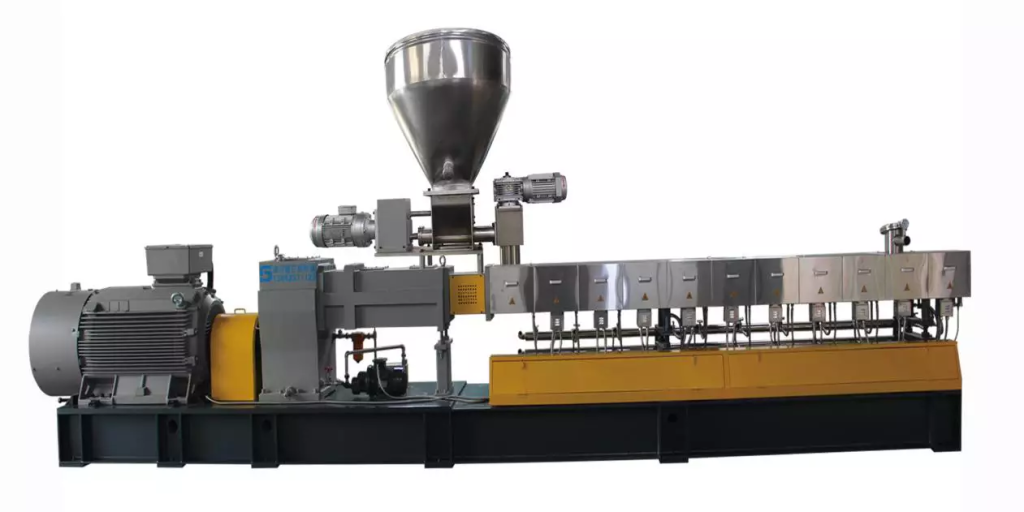
About us
Nanjing Granuwel Machinery CO., LTD is specializing in R&D design and manufacture of high polymer extruders, our team of top-level extrusion professionals provides the right extruder for your exact application.

We possess excellent capability of innovation and product development, and desire to provide best products for our customers through the improvement of equipment structure and reduction of equipment energy consumption through our practical experiences and technical innovation.
For any question/inquiry, warmly welcome to contact us!!!
Tel: +86-25-86199956
Mobile: +86-13813371123
Email:[email protected]