عند استخدام ماكينة الأصبغة الرئيسية لإنتاج الأصبغة الرئيسية، غالبًا ما نواجه بعض المشاكل، لذا لا يمكننا الحصول على الأصبغة الرئيسية المؤهلة. على سبيل المثال، يعد التشتت غير المتساوي في الأصبغة السوداء إحدى المشكلات المعتادة أثناء عملية الإنتاج.
تستعرض هذه المقالة مشكلتين معتادة تتم مواجهتهما عند استخدام ماكينة الأصبغة الرئيسية.
جدول المحتويات
تبديل1. ظاهرة التشتت غير المتساوي لأسود الكربون
سواء كان لديك الارتباك أدناه أم لا؟ أثناء عملية تصنيع الصبغة الرئيسية السوداء، التي تحتوي على أسود الكربون 40% وتستخدم شمع EVA كمشتت، يمكن ملاحظة عدم الاتساق في تشتيت أسود الكربون. يتجلى هذا التناقض في أن بعض الشرائط تكون هشة للغاية بينما البعض الآخر غير قابل للكسر. يتضمن الإنتاج استخدام آلة بثق لولبية مزدوجة، حيث يخضع الخليط لخلط مسبق عالي السرعة قبل إضافته إلى القادوس. تتراوح درجة الحرارة من 160 درجة مئوية إلى 180 درجة مئوية، مع ضبط درجة حرارة الرأس على 175 درجة مئوية.
مشكلة التشتت غير المتساوي لآلة صنع الأصبغة
الكسر المتكرر للشرائط
تفشل المواد الموجودة في القادوس في النزول بسلاسة، مما يؤدي إلى كسر الشرائط بشكل متكرر. في البداية، كان هناك شك في وجود نقص في المواد، ولكن عند التغذية، تم اكتشاف وجود وفرة من المواد في القادوس، مما يتطلب الدفع اليدوي. ومن المثير للاهتمام أن هذه المشكلة لا تنشأ عندما يكون محتوى أسود الكربون 20% أو 30%.
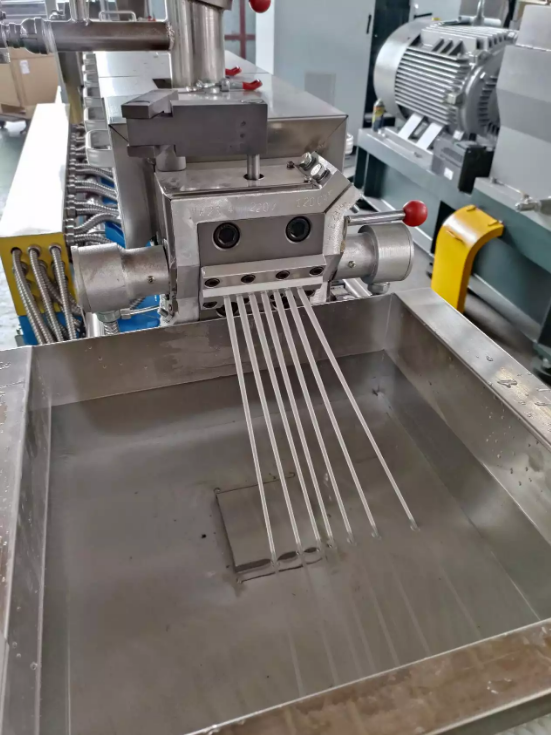
عدم الاتساق في سرعة رأس القالب
علاوة على ذلك، عند وجود مادة، تستمر الشرائط في الانكسار، ويكون هناك عدم تناسق ملحوظ في سرعة منافذ التفريغ. وعلى وجه التحديد، يعمل المنفذان الأوسطان بمعدل أسرع مقارنة بالمنفذين الآخرين، مما يؤدي إلى تفريغ غير متساوٍ.
إن سرعة التفريغ غير المتساوية لرأس الماكينة ناتجة على وجه التحديد عن التشتت غير المتساوي للمادة. المواد المشتتة بشكل سيئ لديها قدرة ضعيفة على الحركة، والمواد المشتتة بالتساوي تتمتع بحركة جيدة. تُجبر المادة ذات السيولة الضعيفة على الالتصاق بالجدار الداخلي لقناة التدفق. تفريغ طرفي الدليل بطيء، وتفريغ الشريط الأوسط سريع.
لسوء الحظ، لا توجد طريقة متاحة للكشف في الموقع، ويتم استخدام الأصبغة الرئيسية مباشرة في الإنتاج. وبالتالي، هناك نقص في الفهم فيما يتعلق بكيفية تقييم جودة الأصبغة الرئيسية بسهولة.
حل
ولمعالجة المشكلات التي تمت مواجهتها، يمكن تنفيذ العديد من الحلول المحتملة.
زيادة كمية شمع EVA
أولاً، يمكن أن تساعد زيادة كمية شمع EVA في عملية التصنيع في تحقيق تشتيت أفضل لأسود الكربون، مما يؤدي إلى تحسين جودة الشريط.
خفض درجة الحرارة بمقدار 10 درجات مئوية
بالإضافة إلى ذلك، فإن تقليل درجة الحرارة بمقدار 10 درجات مئوية يمكن أن يساعد في تحسين ظروف المعالجة وتحسين الأداء العام للأصبغة الرئيسية.
ضبط سرعة الدوران للطارد المزدوج اللولب
هناك طريقة أخرى تتمثل في ضبط سرعة دوران آلة البثق ذات اللولب المزدوج. يمكن القيام بذلك إما عن طريق تقليل السرعة أو زيادتها للعثور على الإعداد الأمثل الذي يعزز تكوين شريط أكثر اتساقًا واتساقًا.
استخدام عناصر لولبية الخلط الخاصة لتحسين قدرة التشتت
نظرًا لأن أسود الكربون له بنية معقدة ودقيقة، فهو يتكون من طبقات عديدة من جزيئات الجرافيت، وهناك فجوات وزوايا صغيرة بين كل طبقة من جزيئات الجرافيت والطبقات الأخرى. هيكلها عبارة عن هيكل متعدد الأصداف، يتكون من تراكم طبقات عديدة من جزيئات الجرافيت. تكون جزيئات كل طبقة سميكة ورقيقة، ويمكن أن تشكل بنية طبقات معقدة. لذلك، فإن الحالة المثالية في تشتت أسود الكربون ليست تدمير فجواته وزواياه الصغيرة، ولكن كتلة القص المستخدمة عادة تكون قوية جدًا، مما سيؤدي إلى تدمير زوايا جزيئات أسود الكربون ويتسبب في تكتل أسود الكربون، لذلك يتم استخدام خيط لولبي خاص أصول مثل أصول S وأصول المنشور السداسي تعمل على تحسين قدرة التوزيع والخلط لأسود الكربون.
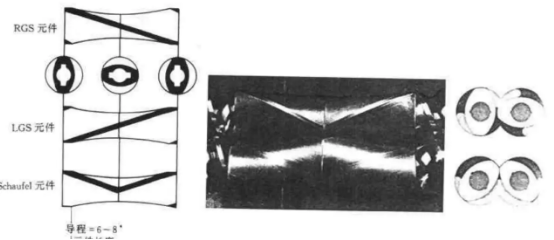
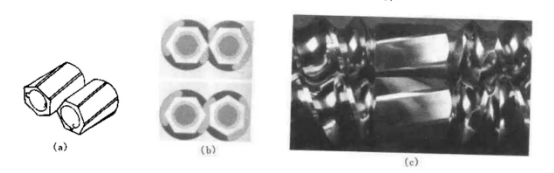
2. ظاهرة تكوين الجسور
يعمل القادوس كوحدة تخزين للمواد الخام البلاستيكية، وبعض القواديس مجهزة بآليات التسخين والنفخ لإنشاء قادوس التجفيف. عادةً ما يكون للقادوس شكل مخروطي في الأسفل وشكل أسطواني في الأعلى. يختلف المنحدر الأمثل للقسم المخروطي اعتمادًا على عوامل مثل حجم الجسيم، وشكل الجسيم، ومعاملات الاحتكاك بين الجزيئات، ومعاملات الترابط. يشير تشكيل الجسر إلى أن الفشل في أخذ هذه العوامل في الاعتبار يمكن أن يؤدي إلى إهدار سعة القادوس أو مشاكل مثل تأثير "الجسر" أو "أنبوب القمع"، مما يؤدي إلى سوء التغذية أو الفشل الكامل في تفريغ المواد. تحدث ظاهرة التجسير عندما يضيق قطر القادوس بسرعة كبيرة بالقرب من منفذ تغذية الطارد. يؤدي هذا التغير السريع في القطر إلى ضغط المادة وتصلبها، مما يعيق دخول المواد الخام إلى الطارد.
مشكلة تشكيل الجسر لاستخدام ماكينة الماسترباتش
تتراكم جزيئات البلاستيك
عندما تتراكم جزيئات البلاستيك وتشكل جسرًا مفتوحًا عند الفتحة الضيقة للقادوس، مما يوفر الدعم للمادة أعلاه، فمن المرجح أن تحدث ظاهرة التجسير. وهذا أمر شائع بشكل خاص في المواد المعاد تدويرها ذات الجزيئات الأكبر والأشكال غير المنتظمة.
تأثير "القمع في الأنابيب".
يمكن أن يساهم تأثير "القمع في الأنابيب" في سد الفجوة. يحدث هذا عندما يفتقر التدفق الهبوطي للجسيمات إلى القوة الكافية لسحب الجزيئات المجاورة معًا. ويكون أكثر انتشارًا عندما يكون حجم الجسيمات البلاستيكية صغيرًا.
المواد التي يتم تعبئتها خفيفة الوزن للغاية
تميل ظاهرة التجسير إلى أن تكون أكثر إشكالية في الحالات التي تكون فيها المادة التي يتم تعبئتها خفيفة الوزن للغاية أو تحتوي على نسبة عالية من الحشو. لتقليل الجسور أو إزالتها، من الضروري اتخاذ تدابير معينة. ويشمل ذلك فصل الهواء المختلط عن المسحوق قبل دخوله إلى جهاز البثق المزدوج اللولب، وتقليل المسافة الرأسية بين منفذ التغذية والمسمار قدر الإمكان، والتأكد من دخول المسحوق إلى أسفل اللولب بدلاً من إضافته مباشرة إلى الأعلى. يجب أن يسهل الهيكل اللولبي حركة الهواء على طول الأخدود اللولبي وتفريغه في قسم العادم، مع منع تدفق الغاز مرة أخرى إلى منفذ التغذية للتفريغ. غالبًا ما يعالج المصنعون مسألة التجسير عن طريق إضافة زيت أبيض 1-2% إلى الخليط وخلطه بقوة لمدة 2-3 دقائق، بشرط أن يسمح المنتج بذلك. من المهم الانتباه إلى وقت الخلط وطريقة الخلط، حيث أنه من الأفضل بشكل عام تحويل المسحوق إلى كتل. يعمل هذا الأسلوب على إزالة الهواء من الحشو بشكل فعال، وضغطه بشكل ما والتخلص من الهواء غير المرغوب فيه. بمجرد أن تصبح الحشوة متكتلة، تزداد كثافتها الظاهرية، وتصبح مسافة واتجاه التغذية بالنسبة للأخدود اللولبي أقل أهمية.
حل
تركيب جهاز اهتزاز أو تقليل انحدار المخروط
يمكن معالجة ظاهرة التجسير في القواديس عن طريق تركيب جهاز اهتزاز أو تقليل ميل المخروط. يمكن أن تؤدي درجات الحرارة المرتفعة في القادوس إلى تليين الكريات البلاستيكية وترابطها، مما يؤدي إلى تكوين الجسور أو الانسداد. يمكن أن تحدث صعوبات في التفريغ عند إضافة مسحوق الكالسيوم بسبب ضعف سيولته والعائق الناتج عن مواد التشحيم الخارجية. للتغلب على ذلك، يوصى بخلط الكالسيوم الثقيل مع الكالسيوم الخفيف، والنظر في إضافة هزاز إلى القادوس السفلي، وزيادة كمية مادة التشحيم الداخلية. تركيب الهزاز هو الحل الأكثر فعالية.
التحكم في درجة الحرارة
يجب التحكم في درجة الحرارة في منطقة التغذية للطارد، حيث يتم نقل المواد عن طريق سحب الاحتكاك، بين 120-160 درجة مئوية. تؤدي درجات الحرارة المنخفضة إلى نقص المواد في المنطقة المنصهرة، بينما تؤدي درجات الحرارة المرتفعة إلى ذوبان مبكر وتكوين طبقة منصهرة على شكل حلقة تشحيم. تعد نسبة ضغط الطبقة الصلبة في قسم التغذية أمرًا بالغ الأهمية لتحقيق الكثافة اللازمة للصهر. من السهل ضغط المواد الجزيئية بسبب قابليتها للتشوه، في حين تتأخر المواد المسحوقة في الضغط بسبب خصائصها المنزلقة وانخفاض كثافة المواد، مما يؤدي إلى تباطؤ عمليات الذوبان والعادم.
استخدام عناصر لولبية خاصة لتحسين قدرة نقل المواد.
ارجع إلى تغذية بعض المواد الخام الأخف وزنًا وسهلة التعويم (مثل أسود الكربون وكربونات الكالسيوم النانوية وما إلى ذلك)، وعادةً ما نستخدم بعض عناصر الخيوط ذات الرصاص الكبير، أو نخصص بعض عناصر الخيوط ذات الرصاص الأكبر، واستخدم هيكل الخيط الخاص - مما يقلل زاوية دفع المواد إلى الزاوية اليمنى (خيط SK الأصلي) - لتحسين قدرة نقل المواد لمنفذ التغذية.
تحسين نسبة العرض إلى الارتفاع لقسم التغذية
غالبًا ما تؤدي معالجة جزيئات اللدائن المرنة بالحرارة، التي تتميز بالاحتكاك الداخلي واللزوجة العالية، إلى نقص المواد، وتقلبات إنتاج الإنتاج، وتدهور المواد. ويمكن معالجة ذلك من خلال تحسين نسبة العرض إلى الارتفاع لقسم التغذية، وتنفيذ التبريد القسري، واستخدام التغذية الاهتزازية. تحتوي بعض المواد الخام للتحبيب على اللدائن، وزيوت الحشو، والمواد المالئة، والراتنجات، ومكونات أخرى، مما يجعل تغذية المواد أمرًا صعبًا بسبب وجود الزيت. لا يُنصح عمومًا بسحق هذه المواد إلى جزيئات صغيرة جدًا. بالإضافة إلى ذلك، من الضروري زيادة معامل الاحتكاك لحافة المسمار في برغي قسم التغذية.
سليم ما قبل التشتت
عندما يتم خلط الصبغة مع الراتنج وتخضع للتشتت المسبق ("مسحوق الفرك")، يجب الانتباه لضمان التشتت المناسب. تؤثر عملية التشتت وما قبل التشتت أثناء تحضير الصباغ بشكل كبير على التشتت بعد المعالجة. يمكن أن يؤدي الفشل في تشتيت مسحوق الحبر مسبقًا إلى خلط غير متساوٍ، مما يؤدي إلى ظهور ألوان مختلفة ("ديكورات") في مناطق مختلفة من المادة. يجب أن يكون مصنعو الخلط حذرين إذا لاحظوا تغيرات في اللون أثناء الإنتاج. من الناحية النظرية، لا ينبغي أن تتعرض الأصبغة، التي يتم تشتيتها مسبقًا بواسطة حامل، إلى تشتت ضعيف. ومع ذلك، من المهم ملاحظة أن الحاملات من نفس اللون يمكن أن تعمل بشكل مختلف أثناء المعالجة. يمكن أن تؤدي الاختلافات الكبيرة في MFR السائبة بين الأصبغة الرئيسية والراتنج المخلوط إلى خلط الألوان. بالإضافة إلى ذلك، إذا كانت مرونة اللون الطبيعية للأصبغة الرئيسية تؤدي إلى تكوين حطام ناعم أثناء عملية الخلط، فقد يؤدي ذلك إلى ظهور ظلال مختلفة من الألوان في المنتج النهائي ("خلط الألوان").
معلومات عنا
نانجينغ جرانويل الماكينات والشركة المحدودة متخصصة في تصميم البحث والتطوير وتصنيع آلات البثق عالية البوليمر، حيث يوفر فريقنا من محترفي البثق رفيعي المستوى آلة البثق المناسبة لتطبيقك الدقيق.

نحن نمتلك قدرة ممتازة على الابتكار وتطوير المنتجات، ونرغب في تقديم أفضل المنتجات لعملائنا من خلال تحسين هيكل المعدات وتقليل استهلاك طاقة المعدات من خلال خبراتنا العملية والابتكار الفني.
عن أي سؤال / استفسار، نرحب ترحيبا حارا في الاتصال بنا!
هاتف: +86-25-86199956
الجوال: +86-13813371123