Table of Contents
ToggleThe development of twin-screw extruder
Screw extrusion is one of the most commonly used processing methods of polymer. It mainly has two forms: single screw and twin screw.Twin-screw extruder appeared in the 1930s. According to the different relative rotation direction of the two screws, they can be divided into two categories: co-rotation and counter-rotation.
In the past 60 years, a conical twin-screw extruder with non-parallel axis of two screws has appeared, which belongs to counter rotation. The counter-rotating twin-screw extruder is stable, which is mainly used for the extrusion of pipes, profiles and other products with high cross-section size. at present, the production of door and window profiles is mostly based on the conical twin-screw extruder.
The co-rotating twin-screw extruder is mainly used for mixing. Mixing plays an important role in polymer processing. More than 50% of the polymer resin has to go through screw mixing before becoming the final product, which shows the importance of co-rotating twin-screw extruder.
At present, most of the extrusion systems of co-rotating twin screw extruders adopt modular structure. The barrel components and screw components can be transformed and combined to meet the special requirements of transportation, melting, mixing, devolatilization, homogenization and so on in the specific mixing process.
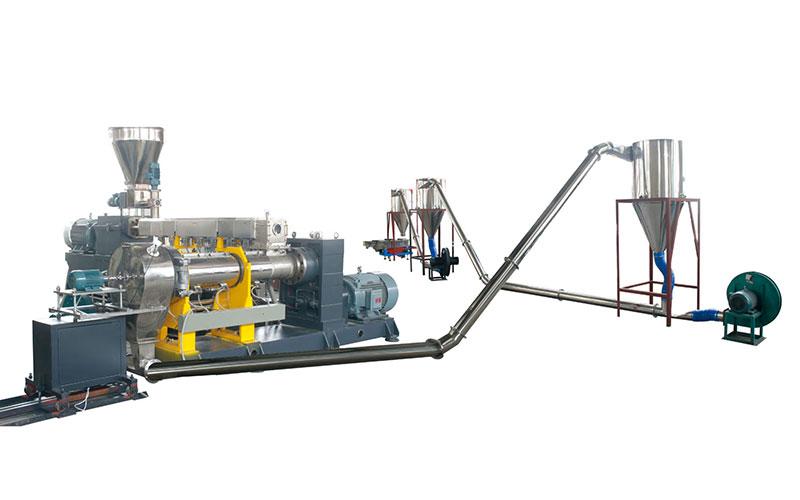
A twin screw is not a simple combination of two single screws. There is not only screw clearance between twin screw and barrel, but also side clearance, Calendering clearance and tetrahedral clearance. The meshing twin screw can be divided into full meshing and partial meshing, and the full meshing type can be further subdivided into conjugate type and non-conjugate type.
The difference of the relative rotation direction makes the geometry of the co-rotating and counter-rotating twin screws different. The two kinds of screws are determined according to the conjugate motion relationship. Their cross-sectional shapes are completely different. At the same time, the differences in kinematic and geometric relations also lead to differences in their extrusion characteristics and application fields.
The difference in the relative direction of rotation makes the geometries of the co-rotating and counter-rotating twin-screws different.Two kinds of screws are determined according to the relationship of conjugate motion and their cross-sectional shapes are completely different. At the same time, the differences in kinematics and geometric relations also lead to differences in their extrusion characteristics and application fields.
The characteristics of the co-rotating twin screw extruder
- The rotating speed of the co-rotating twin screw is relatively high and there is a relatively close relative motion speed at different positions in the meshing area (the overlap of the two screws in the cross section). Therefore, strong and uniform shear force can be produced.
- The geometry determines that the longitudinal flow channel must be open, resulting in material exchange between the two screws. During the exchange, the material originally at the bottom of one screw groove will move to the top of another screw groove. The opening of the longitudinal channel also makes it possible to open the transverse channel to realize the exchange of materials between the adjacent screw grooves of the same screw. This makes the co-rotating twin screw have better distributed mixing ability, so it is most suitable for mixing operation.
- It has good self-cleaning function.
- It has low conveying characteristics and general conveying efficiency, and its pressure building ability is low, so it cannot be used to directly extrude products (except granulation/pellets). If you want to obtain a high base pressure, you need to connect a gear pump downstream, or connect a second-stage single-screw extruder.
- The barrel and screw are segmented combined structure, which brings great flexibility to its application. The best combination of screw and barrel can be made according to the purpose of mixing operation and the requirements achieved to achieve the best results together. The screw and barrel can be partially replaced after wear, so the maintenance cost is low.
The characteristics of the counter-rotating twin screw extruder
- It has excellent positive displacement ability, weak shearing ability and high pressure building ability. It can be directly used for extrusion products at low speed (10-50r/min), especially for processing RPVC.
- If a non-conjugated screw is used, due to the large gap between the screw and the cylinder, when the screw rotates at high speed, some materials will be pulled into the calendering gap and side gap, where they are subjected to high shear rate and tension. Elongation rate, material surface renewal is more efficient,resulting in good distribution mixing and dispersion mixing effect, and the melting efficiency is higher than that of the upper screw.
- This twin-screw is similar to the continuous internal mixer of Farrel Company, mainly used for mixing and preparing high-filling materials,polymer alloys and reactive extrusion, etc. Its working speed can reach 200-300rpm.
- The barrel and screw of such counter-rotating twin-screw extruder are integral structures, and the barrel and screw must be replaced as a whole after wear. Therefore, the maintenance cost is high. And the equipment is limited.
- The geometric parameters of the counter-rotating twin screw determine that its longitudinal flow channel can be closed, so the material is forced forward by the screw, which is the so-called positive displacement. This makes the stable extrusion become the main feature of counter-rotating twin-screw extrusion.
- The positive displacement conveying capacity of the counter-rotating twin-screw is much stronger than that of the same direction. The pressure building ability is higher, so it can be used to directly extrude products, but due to the pressure of the material on the screw, the screw is pressed against the inner wall of the barrel and the barrel is easy to wear. And the higher the screw speed, the more serious the wear, so this extruder can only run at low speed (10-50r/min).