Intermeshing co-rotating twin-screw extruder is widely used in field of plastics+rubber blending modification, plastic cunctional masterbatch. plastic +glass fiber reinforcment, various cable material compounding .PLA+PBAT+ corn starch compounding and so on. It is the first choice of continuous mixing equipment for polymer modification. Co-rotating twin screw extruder is one of the main types of twin screw extruders.

Table of Contents
ToggleStructural characteristics of co-rotating twin-screw extruder
The most prominent feature of the co-rotating twin-screw extruder is the “building block” design of both the screw and the barrel. The screw is composed of several elements sheathed on the mandrel, such as coney element, kneader element, TME,SME etc special functional screw element. The barrel is also composed of different barrel parts ( close barrel, exhaust barrel and feed barrel).
According to the specific material, formula and performance requirements of the mixture to be prepared, through scientific combination, different types and quantities of screw elements (conveying elements and kneader elements)are combined in a certain order, so as to efficiently complete the mixing task.
By changing the combination order of screw and barrel, the best use effect of different materials and formulations can be achieved, and the purpose of multi-use of one machine can be achieved. In addition, another advantage of the building block design is that the worn screw element can be replaced partly, thus avoiding the scrapping of the whole screw and greatly reducing the maintenance cost. The modular design of the barrel can be connected by flanges or drawbars, and mini lab machines are usually connected by drawbars.
The barrel is usually embedded with bimetal bushings to improve the wear resistance of the inner surface of the barrel. In order to arrive at an accurate temperature, each barrel has its own heating / cooling design to achieve the best combination of cooling and heating functions.
By combining various screw elements, all co-rotating twin screw extruders have the functions of feeding, melting, mixing, exhaust, pressure holding and conveying, realizing a variety of processes such as material conveying, plasticizing, shearing, exhaust, pressure holding and extrusion.
Working principle
The structure and function of the co-rotating twin-screw extruder are similar to that of the single-screw extruder, but the working principle is very different. It is mainly shown in the following aspects.
Forcing transport
In an intermeshing co-rotating twin screw, two screws move in opposite directions in the meshing position, one screw pulls the material into the meshing gap, while the other pulls the material out of the gap, causing the material to be transferred from one screw groove to another, and the material is forcibly transported to the head along the screw in a shape.
Homogenization and mixing
The co-rotating twin screw has a small gap in the meshing position, and the speed direction of the screw bar and the screw groove is opposite, so the shear speed in the meshing area is high, the shear force is large. The mixing effect is much better than that of single screw extruder and counter-rotating twin screw extruder.
Fantastic self-cleaning
In the co-rotating twin-screw extruder, the relative speed is higher because the speed direction of the screw rib and the screw groove in the meshing area are opposite. Therefore, it has a very high shear speed, can scrape off any accumulation material attached to the screw, and has a very good self-cleaning effect, so the residence time of the material is very short, and it is not easy to local degradation.
Controllable Plasticization of materials
The screw clearance has a great influence on the plasticizing quality of the material. The smaller the gap, the greater the shear force, but the amount of material passing through decreases. The larger the gap, the greater the amount of material, but the shear force will decrease.
Material compression
There are many ways to compress the material of co-rotating twin-screw extruder, and the comprehensive effect is good.
Flexible Feeding methods
The co-rotating twin-screw extruder adopts metering starvation feeding and realize the blending of different materials at fixed time, uniform quantitative and temperature.
Brilliant Exhaust
As to metering starvation feeding, the conveying element with large lead can be used to make the screw groove in the unfilled state and in the zero pressure state, so that the exhaust section can be set. The negative pressure vacuum pump is used to extract small molecular substances such as volatiles and moisture in the blending system. The general limit vacuum degree can reach -0.1Mpa.
Perfect granulation system
The largest usage of the co-rotating twin screw is modification granulation, different materials need the different pelletizing/granulation systems. There’re several pelletizing/granulation systems are under in consideration. For example: water-cooling strands pelletizing system, air-cooling strand pelletizing system, air-cooling hot-cutting pelletizing system, water ring pelletizing system, eccentric water fogging pelletizing system and the most automated underwater pelletizing system. Besides,different pelletizing system must be equipped with corresponding auxiliary machines.
Application of Twin Screw Extruder
According to the different rotation direction of the two screws, the twin-screw extruder can be divided into co-rotating twin-screw and counter-rotating twin-screw. Intermeshing co-rotating twin screw extruder is widely used in physical and chemical modification of matrix resin, such as filling, reinforcement, toughening, reactive extrusion and so on.
The co-rotating twin-screw extruder should be selected, which is mainly mixed by dispersing and mixing various raw materials, and the velocity vectors of the co-rotating twin-screw are opposite to each other. Therefore, compared with the rotating twin screw, the shearing effect of the same rotating twin screw is much larger, which is not suitable for PVC mixed molding.
Powdered calcium carbonate, talcum powder and titanium dioxide are commonly used for plastic blending and filling, with a filling amount of 30% to 60% and a filling masterbatch of up to 80%. Because the powder filler contains a lot of air, when mixing in the kneading zone of the screw, the air will be separated, resulting in the reverse flow of the material into the screw tank, affecting the forward transportation of the powder, and finally reducing the amount of extrusion.
Application examples of twin screw extruder
- Glass fiber reinforcement, fuel barrier granulation (such as PA6, PA66, polyester, polybutylene terephthalate, polypropylene, polycarbonate reinforced flame retardant, etc.).
- Granulation with high fillers (such as polyethylene and polypropylene filled with 75% calcium carbonate).).
- Granulation of thermosensitive materials (such as polyvinyl chloride and cross-linked polyethylene cable materials).
- Concentrated masterbatch (such as filling with 50% toner); antistatic masterbatch, alloy, coloring, low filling blending granulation.
- Granulation of cable materials (such as sheath materials and insulation materials).
- Granulation of cross-linked polyethylene pipes (such as hot water crosslinking masterbatch).
- Mixing and extrusion of thermosetting plastics (such as phenolic resin, epoxy resin and powder coatings).
- Hot melt adhesive and polyurethane reactive extrusion granulation (such as EVA hot melt adhesive and polyurethane), k resin, SBS devolatilization granulation, PLA +PBAT+ corn starch for full bio-degradation material compounding etc.
Advantages and disadvantages
Due to the complexity of structural design and processing of twin-screw extruder, the theoretical development is not perfect and still have a lot of work to do. However, the combined design of co-rotating twin-screw extruder can combine screw elements and barrel elements with various geometric shapes. The design can be optimized according to different mixing requirements to meet the needs of different process formulations, so that the co-rotating twin-screw extruder has strong adaptability.
It is mainly shown in the following aspects:
Mixing performance
Due to the meshing of the two screws, all kinds of convey elements, such as reverse convey element, kneader element, TME, SME etc. It can be added as needed to precisely adjust the shear / mixing, so that the mixing strength and mixing quality (whether dispersed mixing or dispersed mixing) can be effectively controlled. This is beyond the ability of a single screw extruder.
Processing flexibility
The co-rotating twin screw extruder usually uses the measurement of starvation feed, and the output depends on the feed quantity and has nothing to do with the screw speed, so it is an independent controllable variable, so it can flexibly deal with various processing functions such as melting, mixing, exhaust, reaction and so on.
Controllability of process parameters
The co-rotating twin-screw extruder has narrow(very short) residence time distribution, good convection heat transfer and accurate control of temperature curve, which can obtain better extrusion shear-time and temperature process in a larger range. in order to obtain better product quality stability.
High production efficiency
The positive transportation of the screw can handle more raw materials and mixed formulations, and the shutoff time is short.
Higher economy
Due to high process flexibility and productivity, a wider range of final products can be produced, highly consistent product quality can be provided, and screw wear can be compensated by adjusting screw speed.
About US
Nanjing Granuwel Machinery CO., LTD is specializing in R&D design and manufacture of high polymer extruders, our team of top-level extrusion professionals provides the right extruder for your exact application.
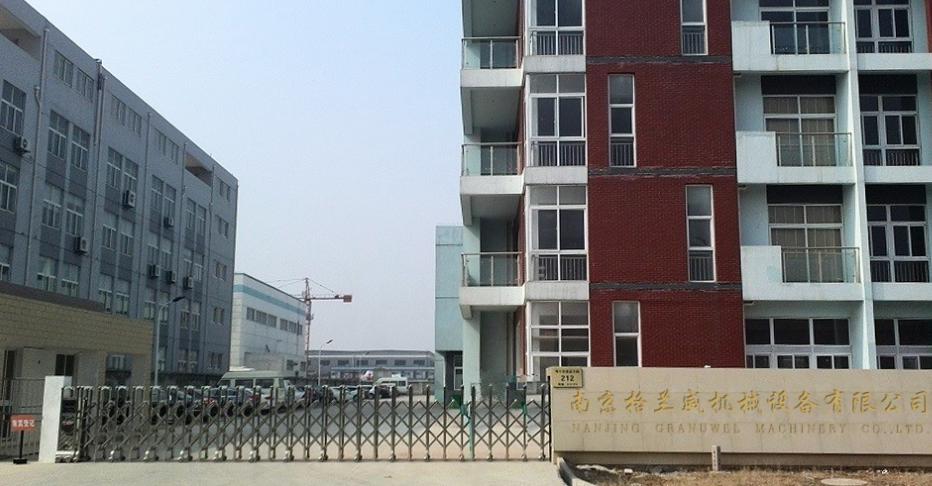
We possess excellent capability of innovation and product development, and desire to provide best products for our customers through the improvement of equipment structure and reduction of equipment energy consumption through our practical experiences and technical innovation.
For any question/inquiry,warmly welcome to contact us!!!
Tel: +86-25-86199956
Mobile: +86-13813371123
Web:https://toolant.net