Inhaltsverzeichnis
UmschaltenDoppelschneckenextruder zur Verarbeitung von gewöhnlichem Hochglanzpulver
Anwendung von Hochglanzpulver in der Kunststoffindustrie
Hochglanzpulver ist ein Pulverzusatz, der Kunststoffen zugesetzt werden kann, um die Helligkeit von Produkten zu erhöhen und das Aussehen und die Textur zu verbessern. Das Prinzip von Hochglanzpulver besteht darin, die diffuse Streuung von Licht zu nutzen, um kleine Fehler in Kunststoffprodukten zu modifizieren, anstatt sich nur auf reines Beschichten zu verlassen, das das Aussehen des Produkts verbessern kann. Um einen Glanzeffekt zu erzielen, ist Bariumsulfat das in der Kunststoffindustrie am häufigsten verwendete Hochglanzpulver. Der Kunststoffmodifizierung wird ein bestimmter Anteil Bariumsulfat zugesetzt, um das Produkt glänzend zu machen und die Festigkeit, Steifheit und Verschleißfestigkeit von Kunststoffprodukten zu verbessern.
Bei der Verarbeitung von gewöhnlichen Hochglanzpulver-MasterbatchBeim Doppelschneckenextruder müssen wir auf zwei Punkte achten: Zum einen auf den eigentlichen Mischeffekt, zum anderen darauf, dass das Pulver nicht agglomeriert und sich gleichmäßig im Kunststoffträger verteilt.
Derzeit sind alle Doppelschneckenextruder für die Herstellung und Verarbeitung von Hochglanzpulver geeignet, sofern es sich um qualifizierte Produkte handelt.
Um die Mischwirkung sicherzustellen (zu verbessern), wirken sich bei der Anordnung der Extruder-Schneckenkombination die Lage des Mischabschnitts, der Abstand zwischen den beiden Schnecken, der Verschleißgrad des Gewindeelements, die Einstellung der Zylindertemperatur und die Genauigkeit der Temperaturregelung auf die Dispersion des Hochglanzpulvers im Kunststoffgranulat aus.
Zu den Überlegungen zum Einsatz von Doppelschneckenextrudern bei der Verarbeitung von Standard-Hochglanzpulver-Masterbatches gehören die folgenden Punkte.
Rohstoffauswahl-Doppelschneckenextruder verwendet
Für die Herstellung von Hochglanzpulver ist die Auswahl hochwertiger Rohstoffe von großer Bedeutung.
Auswahl der Rohstoffe: Für die Herstellung von Hochglanzpulver-Masterbatch ist die Auswahl hochwertiger Rohstoffe von entscheidender Bedeutung.
Stellen Sie sicher, dass die Qualität der Rohstoffe den Produktspezifikationen entspricht, um die Vermischung von Verunreinigungen und Schadstoffen zu vermeiden.
Extruderparametereinstellung - Doppelschneckenextruder verwendet
Passen Sie die Betriebsparameter des Doppelschneckenextruder, einschließlich Temperatur, Druck und Geschwindigkeit usw., um sicherzustellen, dass während der Verarbeitung die ideale Produktleistung und das ideale Erscheinungsbild erzielt werden.
Temperaturregelung-Doppelschneckenextruder verwendet
Die Kontrolle der Temperatur des Extruders ist ein wichtiger Schritt. Stellen Sie sicher, dass die Temperatur der Schnecke und des Zylinders moderat ist, um eine Materialzerstörung durch zu hohe oder zu niedrige Temperaturen zu vermeiden, die den Extrusionseffekt beeinträchtigen.
- Einstellung der Regeltemperatur in Schmelzzonen-Doppelschneckenextrudern
- Wir empfehlen, die eingestellte Temperatur T der Schmelzzone mit dem Seitenverhältnis i der Extruderschnecke und der Rotationsgeschwindigkeit n zu verknüpfen: n≤200 U/minT≈120 °C, n=200-350 U/minT≈140 °C, n=500-800 U/minT≈140 °C, n=500-800 U/minT≈150 °C Wenn i=18, um 5 °C reduzieren, wenn i≥20, um 10 °C reduzieren.
- Kühlwassertemperaturregelung
Aufgrund der selbstreinigenden Eigenschaften des Doppelschneckenextruders ist der Spalt zwischen den Schnecken klein. Das Material im Zylinderhohlraum erhöht die innere Reibung aufgrund der Widerstandskraft zwischen den Schmelzen, wodurch die Innentemperatur des Materials erheblich ansteigt. Schnell, und die Wärme staut sich bis zum Höhepunkt im Extrusionsabschnitt. Daher ändert sich die Temperatureinstellung des Doppelschneckenextruders von schneller Erwärmung am Einfüllstutzen zu schneller Abkühlung im Extrusionsabschnitt, sodass die Kontrollanforderungen für das Kühlwasser strenger sind. Andernfalls wird die Dispersion des Masterbatches beeinträchtigt, weil die Materialtemperatur zu hoch ist.
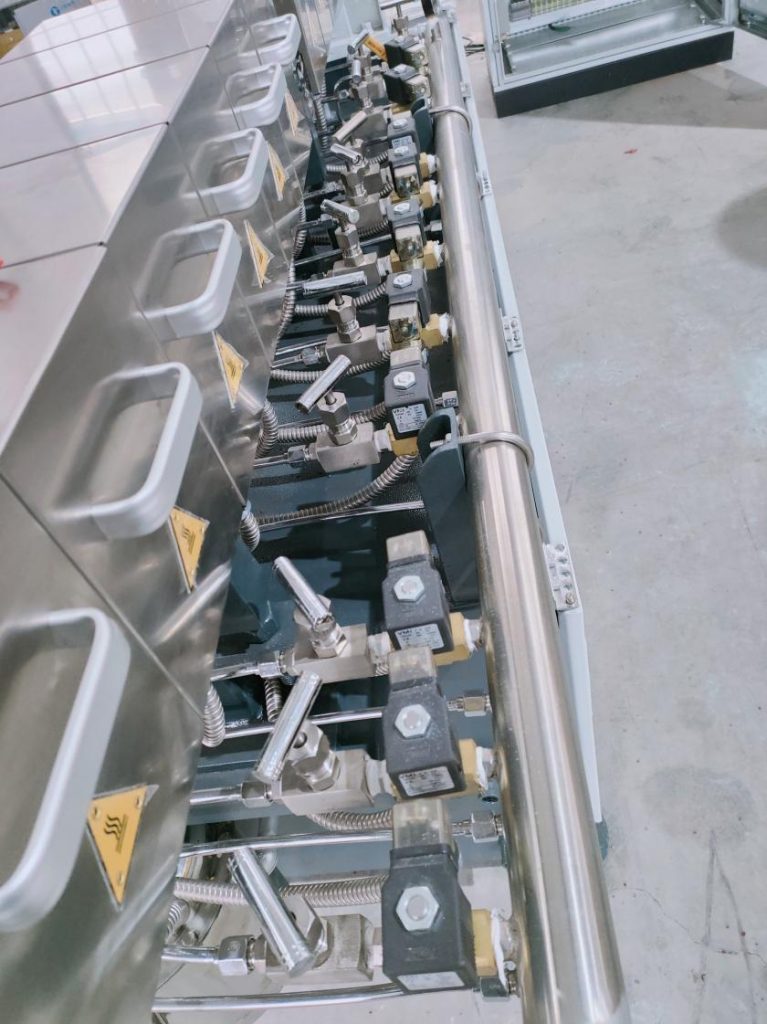
Daher ist jeder Abschnitt mit einer unabhängigen Kühlleitung ausgestattet. Das Magnetventil steuert den Einlass und Auslass des Kühlwassers und das Drosselventil steuert den Kühlwasserfluss. Während des Öffnens und Schließens des Magnetventils wird eine präzise Temperaturregelung erreicht. Dies stellt sehr hohe Anforderungen an die Qualität und Lebensdauer von Magnetventilen. Normalerweise beträgt der ideale Temperaturregelbereich +-2 °C. Wenn der Einstellbereich der Temperaturdifferenz 10 °C überschreitet, ist es schwierig, den tatsächlichen Mischeffekt sicherzustellen.

Die Genauigkeit der Temperaturregelung hängt von der Durchflussrate und dem Temperaturanstieg des Kühlwassers ab. Je größer die Durchflussrate und je geringer der Temperaturanstieg, desto höher ist die Genauigkeit.
Und das Kühlwasser des Maschinenlaufs sollte weiches Wasser sein (kleiner Kreislauf).
Normalerweise bildet heißes Wasser Schmutz in den Strömungskanälen des Zylinders. Mit der Zeit verstopfen die Kühlströmungskanäle des Zylinders. Um Wartung und Temperaturkontrolle zu erleichtern, sind wir mit einem speziellen Kühlwassertank ausgestattet. In den Wassertank müssen Kunden enthärtetes oder destilliertes Wasser geben, um verstopfte Wasserkanäle zu vermeiden. Das Wasser im Wassertank passiert eine hochtemperaturbeständige Wasserpumpe und wird in die Hauptleitung gepumpt, wo es dann über Magnetventile zu jedem Zylinder umgeleitet wird. Daher: Jeder Zylinder ist eine unabhängige Temperaturregeleinheit, die durch ein Temperaturregelmessgerät oder ein Halbleiterrelais eines Temperaturregelmoduls, ein Hauptwasserzulaufrohr, ein Hauptrücklaufrohr, ein Magnetventil, ein Durchflussventil und andere Rohrverbindungen ein geschlossenes Kühlsystem bildet. Einheit, das von jeder Temperaturregelzone zurückgeführte heiße Wasser wird gesammelt und über den Plattenwärmetauscher in den Wassertank zurückgeführt.
- Verfestigte Partikel
Es gibt viele Faktoren, die zur Bildung von verfestigten Partikeln führen. Dies ist ein umfassender Faktor, der nicht nur mit der Mischung der Formel und der Komponentenqualität und sogar der Charge zusammenhängt, sondern auch mit der Leistung der ACM-Mühle zusammenhängt, wie z. B. übermäßige Erwärmung des Mahlhohlraums usw.
Beim Doppelschneckenextruder liegt der erste Grund darin, dass der Abstand in jedem Teil der Schnecke zu klein oder zu groß ist. Bei einer kleinen Schnecke erhöht sich die Reibung, und die lokale Temperatur ist zu hoch. Dies führt aufgrund des Verlusts der Selbstreinigungsfähigkeit zur Aushärtung des Materials bei niedrigen Temperaturen.
Andererseits ist die Einstelltemperatur jeder Zone instabil, insbesondere im Auslassbereich, die spezifische Temperatur im Betrieb übersteigt die eingestellte Temperatur bei weitem oder der Auslassanschluss sammelt sich über einen langen Zeitraum an, was zu einer Aushärtung bei niedriger Temperatur führt.
Daher gibt es drei Schlüsselbedingungen für die Herstellung und Verarbeitung von Hochglanzpulver-Masterbatches:
- Perfekte Formel und hochwertige Inhaltsstoffe
- Es handelt sich um eine Maschine mit hervorragenden technischen Parametern und überlegener Leistung.
- Es handelt sich dabei um eine geschickte Manipulationstechnik.
Ganztägige Wartung und Vorsichtsmaßnahmen für Hochglanz-Pulver-Masterbatch-Produktionsanlagen
1. Schneckengeschwindigkeit: Passen Sie die Schneckendrehzahl an, um sicherzustellen, dass die Rohstoffe während des Extrusionsprozesses vollständig vermischt werden und eine gleichmäßige Extrusion gewährleistet ist.
2. Reinigung und Wartung des Extruders: Reinigen Sie den Extruder regelmäßig, um zu verhindern, dass Rückstände die Produktqualität beeinträchtigen. Überprüfen Sie regelmäßig die Schnecke, den Zylinder und andere wichtige Komponenten, um sicherzustellen, dass sie ordnungsgemäß funktionieren.
3. Produktkühlung: Nach der Extrusion wird das Produkt richtig gekühlt, um sicherzustellen, dass sich keine Feuchtigkeitsrückstände auf der Oberfläche des Hochglanzpulver-Masterbatches befinden und um den Energieverlust durch die anschließende Trocknung zu verringern.
4. Qualitätskontrolle: Implementieren Sie strenge Qualitätskontrollmaßnahmen, einschließlich Stichprobenprüfungen der extrudierten Produkte, um sicherzustellen, dass die Produkte den Spezifikationen und Kundenanforderungen entsprechen.
5. Sichere Produktion: Während des Verarbeitungsprozesses müssen die entsprechenden Sicherheitsverfahren befolgt werden, um die Sicherheit der Bediener und der Geräte zu gewährleisten.
Durch die oben genannten Vorsichtsmaßnahmen können die Produktionseffizienz und Produktqualität von gewöhnlichem Hochglanzpulver, das mit einem Doppelschneckenextruder verarbeitet wird, wirksam verbessert werden.
Wenn Sie mehr über die Herstellung von Hochglanz-Pulver-Masterbatches erfahren möchten, kontaktieren Sie uns für weitere Informationen.
Über uns
Nanjing Granuwel Machinery CO., LTD ist auf die Forschung und Entwicklung sowie die Herstellung von Hochpolymer-Extrudern spezialisiert. Unser Team aus Extrusionsexperten der Spitzenklasse liefert den richtigen Extruder für Ihren genauen Anwendungszweck.
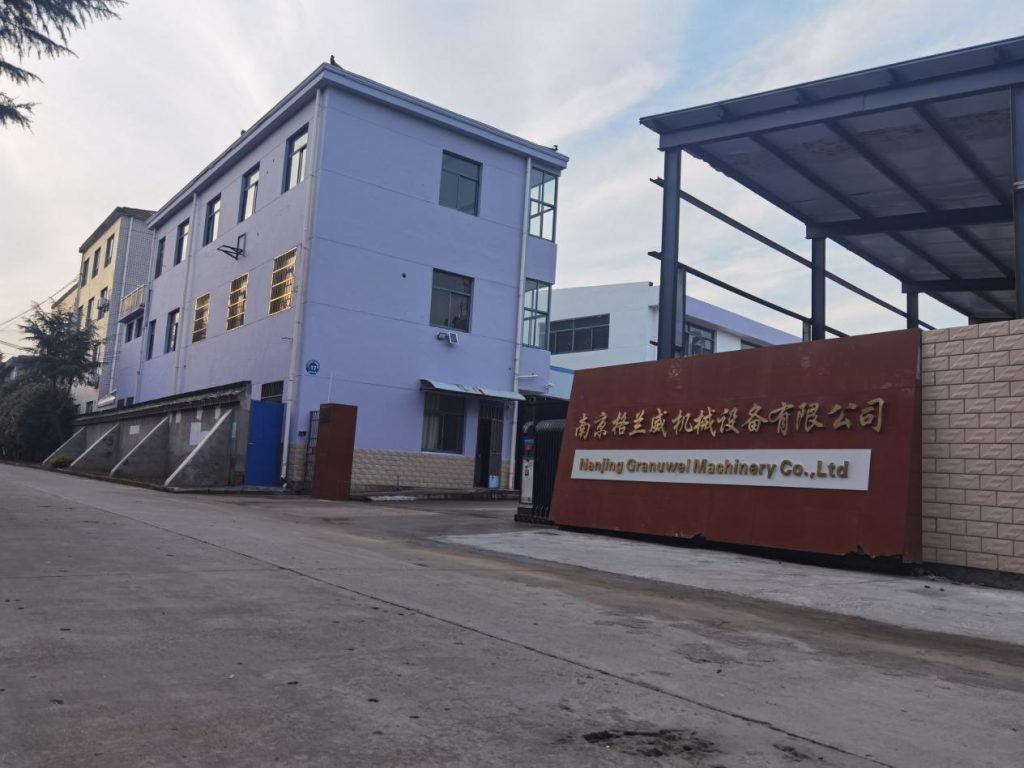
Wir verfügen über hervorragende Innovations- und Produktentwicklungsfähigkeiten und möchten unseren Kunden die besten Produkte bieten, indem wir auf Grundlage unserer praktischen Erfahrungen und technischen Innovationen die Gerätestruktur verbessern und den Energieverbrauch der Geräte senken.
Bei Fragen oder Anfragen können Sie sich jederzeit gerne an uns wenden!!!
Tel: +86-25-86199956
Handy: +86-13813371123
E-Mail: [email protected]
Netz: https://toolant.net