Inhaltsverzeichnis
UmschaltenEinführung
Extruder sind mechanische Geräte, die Hitze, Druck und mechanische Scherkräfte zur Materialverarbeitung nutzen. Doppelschneckenextruder bestehen, wie der Name schon sagt, aus zwei ineinandergreifenden Schnecken in einem Zylinder. Diese Schnecken drehen sich in die gleiche Richtung und erzeugen eine Knet- und Mischwirkung, die die Materialverarbeitung erleichtert.
Ineinandergreifender Doppelschneckenextruder

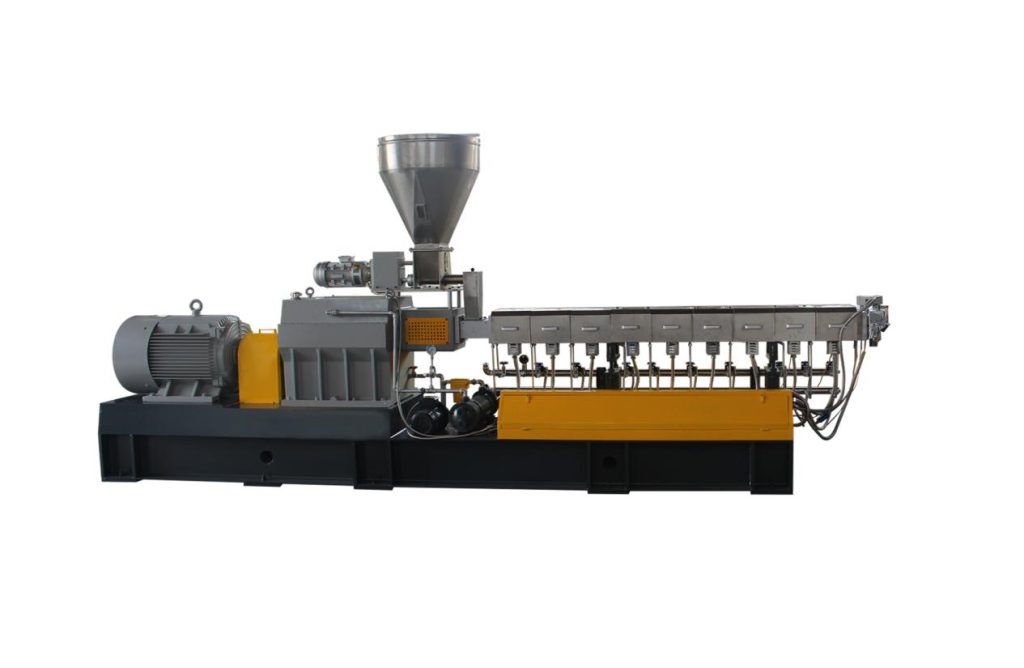
Im Gegensatz zu nicht ineinandergreifenden Doppelschneckenextrudern sind die Schnecken von ineinandergreifenden Doppelschneckenextrudern in einem einzigen Zylinder eng miteinander verzahnt. Diese Konstruktion ermöglicht eine intensive Verzahnung und verbessert so die Misch- und Verteilungseigenschaften.
Anwendung für ineinandergreifende Doppelschneckenextruder
Ineinandergreifende Doppelschneckenextruder werden häufig in Branchen eingesetzt, in denen effizientes Mischen, Compoundieren und Dispergieren erforderlich ist. Die Schnecken in einem ineinandergreifenden Doppelschneckenextruder haben ein komplexes Profil mit ineinandergreifenden Elementen, was eine größere Materialverarbeitungskapazität ermöglicht.
- Polymer-Compoundierung
- Masterbatch-Herstellung
- Mischungen und Legierungen
- Gummiverarbeitung
- Lebensmittel- und Futtermittelverarbeitung:
- Herstellung von Pharmazeutika und Nutraceutika
Vorteile eines ineinandergreifenden Doppelschneckenextruders
- Einer der Hauptvorteile von Doppelschneckenextrudern mit ineinandergreifenden Schnecken ist ihre hervorragende Selbstreinigungsfähigkeit. Während sich die Schnecken drehen, reiben sich die ineinandergreifenden Elemente gegenseitig ab und sorgen so dafür, dass das Material während des gesamten Prozesses gleichmäßig gemischt und verteilt wird. Dies führt zu einer verbesserten Produktqualität und -einheitlichkeit.
- Auch das Einbringen von Additiven, Füllstoffen oder Verstärkungsmitteln in das Material gestaltet sich mit ineinander greifenden Doppelschneckenextrudern einfacher.
- Die ineinandergreifenden Schrauben erzeugen ausreichend Druck und Scherkräfte, um diese Komponenten gleichmäßig in der Matrix zu verteilen, was zu verbesserten Materialeigenschaften führt.
Das Design von ineinandergreifenden Doppelschneckenextrudern ermöglicht eine breite Palette von Anwendungen in verschiedenen Branchen. Sie werden häufig in der Kunststoffindustrie zum Mischen von Polymeren mit Additiven, zum Erstellen von Masterbatches und zum Herstellen von Mischungen verwendet. Darüber hinaus werden ineinandergreifende Doppelschneckenextruder in der Lebensmittelindustrie zum Mischen von Zutaten, Extrudieren von Teig und zur Verarbeitung von Fleisch- und Fischprodukten eingesetzt.
Im Bereich Tierfutter für die Mischung und Dispersion von Proteinen, Kohlenhydraten, Fett usw.;
Im Bereich der Polymerisationsreaktionen zur Monomerpolymerisation, Entgasung und anderen physikalischen oder chemischen Reaktionen.
Schlüsselkomponenten eines ineinandergreifenden Doppelschneckenextruders
Zu den Hauptkomponenten eines Extruders mit ineinandergreifenden Doppelschnecken gehören Zylinder, Schnecken, Antriebssystem und Bedienfeld.
Zylinder und Schneckenwelle werden präzise bearbeitet, um die Genauigkeit der Konstruktionsanforderungen zu gewährleisten und eine gleichmäßige Verteilung der Materialien und eine effiziente Verarbeitung zu gewährleisten. Der Zylinder ist mit Heiz- und Kühlzonen ausgestattet, um die Temperatur während des Extrusionsprozesses zu regeln. Das Antriebssystem liefert die erforderliche Leistung und das erforderliche Drehmoment zum Drehen der Schnecken, während das Bedienfeld eine präzise Einstellung von Parametern wie Schneckendrehzahl, Temperatur und Druck ermöglicht.
Nicht ineinandergreifender Doppelschneckenextruder
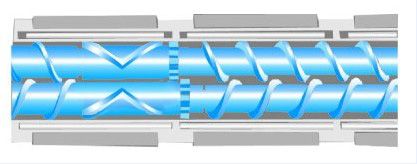
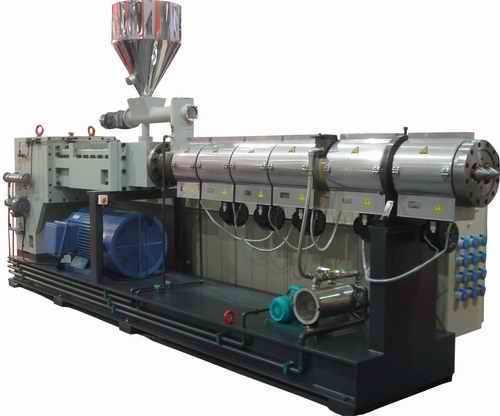
Ein nicht ineinandergreifender Doppelschneckenextruder, auch als paralleler Doppelschneckenextruder bekannt, verfügt über zwei Schnecken, die nicht direkt miteinander in Kontakt kommen. Stattdessen rotieren sie nebeneinander in getrennten Zylindern. Jede Schnecke hat ihren eigenen Kanal, wodurch eine unabhängige Steuerung des Materialflusses und der Verarbeitungsbedingungen möglich ist.
Vorteile eines nicht ineinandergreifenden Doppelschneckenextruders
Der nichtkämmende Doppelschneckenextruder bietet in bestimmten Anwendungen mehrere Vorteile.
- Erstens ermöglicht es eine präzise Kontrolle der Temperatur, Verweilzeit und Schergeschwindigkeit und eignet sich daher für die Verarbeitung wärmeempfindlicher Materialien.
- Zweitens wird durch das Fehlen eines direkten Schraubenkontakts der Verschleiß der Komponenten verringert, was zu einer längeren Lebensdauer der Maschine führt.
- Schließlich wird dieser Extrudertyp häufig für Entgasungsprozesse in der Polymerindustrie verwendet, bei denen flüchtige Verbindungen entfernt werden müssen.
Schlüsselkomponenten eines nicht ineinandergreifenden Doppelschneckenextruders
Zu den Hauptkomponenten eines nicht ineinandergreifenden Doppelschneckenextruders gehören die Zylinder, Schnecken, das Antriebssystem und das Bedienfeld. Die Schnecken können je nach den gewünschten Verarbeitungsanforderungen gleich- oder gegenläufig rotieren. Darüber hinaus kann der Extruder über verschiedene Zuführmechanismen verfügen, wie z. B. gravimetrische oder volumetrische Zuführvorrichtungen, um eine gleichmäßige Materialzufuhr zu gewährleisten.
Anwendung für nicht ineinandergreifende Doppelschneckenextruder
- Polymer-Entgasung
- Wärmeempfindliche Materialien
- Compoundieren und Mischen
- Herstellung von Spezialpolymeren
- Pharmazeutische Verarbeitung
- Lebensmittelverarbeitung
Vergleich zwischen nicht ineinandergreifenden und ineinandergreifenden Doppelschneckenextrudern
Sowohl nichtkämmende als auch kämmende Doppelschneckenextruder bieten einzigartige Vorteile und eignen sich für bestimmte Anwendungen. Um ihre Unterschiede besser zu verstehen, vergleichen wir sie anhand mehrerer Aspekte:
Leistung und Effizienz
Einführung von Überschrift 3 zur Anzeige der Gliederungsstruktur.
Nicht ineinandergreifende Doppelschneckenextruder eignen sich hervorragend für Anwendungen, bei denen eine präzise Kontrolle der Verarbeitungsbedingungen entscheidend ist. Sie bieten eine hervorragende Temperaturkontrolle, Verweilzeitverteilung und Scherraten. Dies macht sie ideal für die Verarbeitung wärmeempfindlicher Materialien und das Erreichen spezifischer Produkteigenschaften. Ineinandergreifende Doppelschneckenextruder hingegen sind für ihre überlegenen Mischfähigkeiten bekannt. Sie bieten intensive Scher- und Dispersionskräfte, was zu einer verbesserten Homogenität und Dispersion von Additiven oder Füllstoffen führt.
Verarbeitungskapazitäten
Nicht ineinandergreifende Doppelschneckenextruder werden häufig bevorzugt, wenn Entgasungs- oder reaktive Extrusionsprozesse erforderlich sind. Die unabhängigen Kanäle der Schnecken ermöglichen eine bessere Kontrolle dieser Prozesse. Ineinandergreifende Doppelschneckenextruder hingegen sind bei Compoundier- und Mischanwendungen äußerst effizient. Ihre ineinandergreifenden Schnecken gewährleisten eine ausgezeichnete distributive Mischung, wodurch sie sich für die gleichmäßige Dispersion von Additiven oder die Herstellung von Spezialverbindungen eignen.
Materialverträglichkeit
Beide Extrudertypen sind mit einer Vielzahl von Materialien kompatibel, darunter Kunststoffe, Gummi, Lebensmittelzutaten und pharmazeutische Verbindungen. Die Wahl des Extruders hängt jedoch vom jeweiligen Material und den gewünschten Verarbeitungsanforderungen ab. Nicht ineinandergreifende Doppelschneckenextruder werden häufig für wärmeempfindliche Materialien oder Prozesse bevorzugt, die eine präzise Temperaturregelung und Scherung erfordern. Ineinandergreifende Doppelschneckenextruder werden häufig zum Compoundieren, Mischen und Erreichen einer hervorragenden Mischleistung verwendet.
Wartungs- und Kostenüberlegungen
Wartungsanforderungen und -kosten können zwischen nicht ineinandergreifenden und ineinandergreifenden Doppelschneckenextrudern variieren. Nicht ineinandergreifende Doppelschneckenextruder haben aufgrund des fehlenden direkten Schneckenkontakts typischerweise weniger Verschleißteile. Dies kann zu einem geringeren Wartungsbedarf und einer längeren Lebensdauer der Maschine führen. Auf der anderen Seite haben ineinandergreifende Doppelschneckenextruder komplexe Schneckenprofile mit ineinandergreifenden Elementen, die häufigere Wartung und den Austausch von Verschleißteilen erfordern können. Die Kosten für nicht ineinandergreifende Doppelschneckenextruder können aufgrund ihrer präzisen Steuerungsmöglichkeiten zunächst höher sein, während ineinandergreifende Doppelschneckenextruder häufig aufgrund ihrer hervorragenden Mischleistung und Vielseitigkeit bevorzugt werden.
Zusammenfassend lässt sich sagen, dass nicht ineinandergreifende Doppelschneckenextruder und ineinandergreifende Doppelschneckenextruder in verschiedenen Anwendungen deutliche Vorteile bieten. Nicht ineinandergreifende Doppelschneckenextruder ermöglichen eine präzise Kontrolle der Verarbeitungsbedingungen und eignen sich für die Entgasung und reaktive Extrusion. Ineinandergreifende Doppelschneckenextruder eignen sich hervorragend zum Mischen, Compoundieren und Erreichen einer gleichmäßigen Dispersion von Additiven. Die Wahl zwischen den beiden hängt vom jeweiligen Material, den Verarbeitungsanforderungen und dem gewünschten Ergebnis ab.