Inhaltsverzeichnis
UmschaltenWas ist eine Kunststoff-Pelletiermaschine?
Der Arbeitsvorgang einer Kunststoffpelletiermaschine besteht darin, dass zunächst Kunststoff und andere Hilfsmittel in den Extruder gegeben werden. Anschließend werden die Materialien geschmolzen, gemischt und bei einer bestimmten Schneckengeschwindigkeit und Temperatur durch den Kunststoffgranulator extrudiert. Die Kunststoffpartikel werden mit einem speziellen Granulierverfahren verarbeitet. Im Allgemeinen besteht die Kunststoffpelletiermaschine aus einer Hauptmaschine zur Kunststoffextrusion, einer Hilfsmaschine zur Granulierung und einem Trichter.
Je nach Produktionsbedarf und technologischem Verfahren wird der Kunststoffextruder in Einschneckenextruder, parallele, gleichlaufende Doppelschneckenextruder, Dreischneckenextruder usw. unterteilt. Einschneckenextruder werden hauptsächlich für Rückgewinnungsgranulierung, Folienextrusionsformen und andere Prozesse verwendet. Gleichlaufende Doppelschneckenextruder werden hauptsächlich für alle Arten von Kunststoffmischung, -modifizierung, Füllgranulierung oder reaktive Extrusion verwendet.
Der Dreischneckenextruder wird hauptsächlich zur Herstellung von Kunststoff-Masterbatches wie Kunststofffüllungen und schwarzen Masterbatches verwendet. Je nach Kühlmedium und Kühlreihenfolge kann der Granulator in wassergekühlte Streifengranulierung, luftgekühlte Streifengranulierung, Wasserring-Heißschneidgranulierung, luftgekühlte Heißschneidgranulierung und Unterwassergranulierung unterteilt werden. Im Folgenden finden Sie eine kurze Einführung in die relevanten Teile.

Komponenten des Einschneckenextruders
Der Einschneckenextruder besteht hauptsächlich aus Extrusionssystem, Übertragungssystem und Heiz- und Kühlsystem.
Extrusionssystem
Die Hauptfunktion des Extrusionssystems besteht darin, das Polymermaterial zu schmelzen und zu plastifizieren, um eine gleichmäßige Schmelze zu bilden und die Umwandlung vom Glaszustand in den viskosen Fließzustand zu realisieren. Bei diesem Vorgang wird ein bestimmter Druck aufgebaut und kontinuierlich extrudiert und durch die Schraube zur Düse transportiert. Daher spielt das Extrusionssystem eine wichtige Rolle bei der Formqualität und dem Ergebnis der Extrusionsverarbeitung.
Übertragungssystem
Das Getriebesystem besteht normalerweise aus Motor, Getriebegehäuse, Kupplung usw. Seine Hauptfunktion besteht darin, die Schnecke anzutreiben und das im Extrusionsprozess benötigte Drehmoment zu steuern. Beim Extrusionsprozess muss die Schneckendrehzahl stabil sein und darf sich nicht mit der Schneckenlast ändern, um eine gleichmäßige Qualität der Produkte zu gewährleisten.
In verschiedenen Situationen muss die Schnecke jedoch eine variable Geschwindigkeit erreichen, damit eine Anlage den Anforderungen des Extrudierens verschiedener Materialien oder Produkte unterschiedlicher Form gerecht wird. Bei den meisten Extrudern wird die Änderung der Schneckengeschwindigkeit durch Anpassen der Motordrehzahl erreicht, und das Übertragungssystem ist mit einem guten Schmiersystem ausgestattet.
Heiz- und Kühlsystem
Das Heiz- und Kühlsystem des Extruders besteht aus einer Heizvorrichtung und einer Kühlvorrichtung, was eine notwendige Voraussetzung für einen reibungslosen Ablauf des Extrusionsprozesses ist. Die Heizvorrichtung und die Kühlvorrichtung müssen sicherstellen, dass das Polymermaterial geschmolzen und plastifiziert wird und die Temperaturbedingungen im Formprozess den Prozessanforderungen entsprechen.
Die Kühlvorrichtung ist im Allgemeinen im Zylinder, in der Schnecke und im Einfüllstutzen des Extruders angeordnet. Die Zylinderkühlung kann wassergekühlt oder luftgekühlt sein. Kleine und mittelgroße Extruder verwenden im Allgemeinen eine Luftkühlung, während große Extruder meist eine Wasserkühlung oder eine Kombination der beiden Formen verwenden.
Bei der Schneckenkühlung wird hauptsächlich eine zentrale Wasserkühlung verwendet, die darauf abzielt, die Feststoffförderrate zu erhöhen, die Leistung zu stabilisieren und die Produktqualität zu verbessern. Der Hauptzweck der Kühlvorrichtung an der Auslassöffnung besteht darin, den Feststofftransport zu verbessern, das Anhaften von Materialpartikeln durch Erhitzung zu verhindern und die Materialöffnung zu blockieren, um die Zufuhr zu beeinträchtigen. Im Allgemeinen muss bei Extrudern mit einem Schneckendurchmesser über 90 mm oder Hochgeschwindigkeitsextrudern am Boden des Trichters eine Kühlvorrichtung installiert werden.

Komponenten des Doppelschneckenextruders
Der Aufbau eines Doppelschneckenextruders ähnelt dem eines Einschneckenextruders und besteht ebenfalls aus Extrusionssystem, Übertragungssystem und Heiz- und Kühlsystem. Der Aufbau des Getriebes im Doppelschneckenübertragungssystem ist viel komplexer als der des Einschneckengetriebes, das das Drehmoment des Motors gleichmäßig auf zwei Wellen mit gleicher Geschwindigkeit und Drehrichtung verteilt, um die Arbeit der beiden Schnecken zu ermöglichen.
Das Extrusionssystem der Doppelschnecke besteht aus Zylinder und Schnecke, die modular aufgebaut sind. Hersteller können die Länge des Zylinders und die Struktur der Schnecke je nach Prozessprojekt frei anpassen, um ein breiteres Anwendungsspektrum zu erreichen.
Der Maschinenkopf ist ein wichtiger Bestandteil der Kunststoff-Pelletiermaschine. Die Spitzen verschiedener Materialien sind möglicherweise nicht genau gleich. Je nach Granuliermodus kann es in Kaltschneidemaschinenköpfe, Heißschneidemaschinenköpfe und Unterwasserschneidemaschinenköpfe unterteilt werden.
Das Prinzip des Kaltschneidemaschinenkopfes besteht darin, die Schmelze durch einen flachen Kanal in Streifen zu extrudieren. Zuerst kühlen (wassergekühlt und luftgekühlt), um sie zu trocknen, und dann in Pellets schneiden. Das Prinzip des Heißschneidemaschinenkopfes besteht darin, die Schmelze durch einen kreisförmigen Kanal in Streifen zu extrudieren. Der rotierende Fräser schneidet sie in Partikel. Und dann durch Trocknen, Kühlen (Wasserkühlung oder Windkühlung).
Die Unterwassergranulierdüse wird in Wasser getaucht. Nachdem die Schmelze durch den Fließkanal extrudiert wurde, schneidet der rotierende Schneider das Granulat im Wasser und bringt es zum Entwässerer, um es durch das fließende Wasser zu trocknen.

Energieeinsparung des Extruders
Abhängig vom Druck und der Scherkraft, die durch die Drehung der Schnecke erzeugt werden, kann der Schneckenextruder das Material vollständig plastifizieren, gleichmäßig mischen und durch die Düse formen. Kunststoffextruder können grundsätzlich in Doppelschneckenextruder, Einschneckenextruder und selten in Mehrschneckenextruder und Nichtschneckenextruder unterteilt werden.
Die Energiesparteile des Extruders sind: einer ist der Antriebsteil, der andere ist der Heizteil.
Leistungsteil
Meistens wird ein Frequenzumrichter verwendet. Die Energiesparmethode besteht darin, die Restenergie des Motors zu sparen. Beispielsweise beträgt die tatsächliche Leistung des Motors 50 Hz. Tatsächlich werden nur 30 Hz benötigt, um den Produktionsbedarf zu decken, und der übermäßige Energieverbrauch ist sinnlos. Bei Verschwendung ändert der Frequenzumrichter die Leistungsabgabe des Motors. Der Motor erzielt den Effekt der Energieeinsparung.
Heizteil
Die meisten Heizteile verwenden elektromagnetische Heizgeräte und ihre Energiesparrate beträgt etwa 30 TP3T bis 70 TP3T gegenüber der alten Widerstandsspule.
Das Kunststoffmaterial wird durch den Trichter in den Extruder gegeben und durch die Drehung der Schnecke vorwärts transportiert. Während sich das Material vorwärts bewegt, wird es durch den Zylinder erhitzt und nach der Scherung und Kompression durch die Schnecke geschmolzen, wodurch die Umwandlung zwischen dem glasartigen Zustand, dem hochelastischen Zustand und dem viskosen Fließzustand realisiert wird.
Bei erhöhtem Druck durchläuft das Material im viskosen Fließzustand die Form mit einer bestimmten Form und wird dann zu einem Kontinuum mit einem Querschnitt ähnlich der Form. Dann wird es abgekühlt und in einen glasartigen Zustand geformt, wodurch die zu bearbeitenden Teile entstehen.
Acht Punkte müssen im Produktionsbetrieb beachtet werden
- Der korrekte Betrieb des Extruders für Kunststoffabfälle kann die Lebensdauer des Geräts verlängern. Der Verwendung des Kunststoffextruders wird in unserem täglichen Leben jedoch häufig nicht genügend Aufmerksamkeit geschenkt, was zu unnötigen Problemen führt. Auf welche Probleme sollten wir also beim Einsatz von Kunststoffmaschinen achten?
- Achten Sie auf den Brandschutz. Feuerlöscher sollten in der Nähe von Geräten aufgestellt werden, die Wärmeleitöl verwenden.
- Wenn ein Fehler oder eine ungewöhnliche Situation auftritt, muss dies dem zuständigen Personal gemeldet werden, und professionelles Wartungspersonal wird gebeten, sich darum zu kümmern. Wenn Sie ungewöhnliche Phänomene feststellen, denken Sie daran, sofort den Not-Aus-Schalter zu drücken.
- Verwenden Sie keine minderwertigen Recyclingmaterialien mit Metallverunreinigungen oder Ablagerungen und platzieren Sie keine Metallgegenstände, die in die Nähe des Einfüllstutzens fallen könnten, um den Verschleiß von Schnecke und Zylinder zu verschlimmern oder Staus oder Schäden zu vermeiden. Um zu verhindern, dass möglicherweise in den Materialien Metall enthalten ist, kann am Auslass ein starker Magnet angebracht werden.
- Das Getriebe sollte mit einem den Anforderungen entsprechenden Schmieröl gefüllt sein und das neue Schmieröl sollte regelmäßig und streng nach der Betriebsanleitung des Geräts überprüft und ausgetauscht werden.
- Kunststoffmaschinen müssen in strikter Übereinstimmung mit den Anforderungen der Betriebsvorschriften betrieben werden und dürfen nicht unter Verletzung der Vorschriften in nicht in Betrieb befindlichen Stationen betrieben werden. Um die Sicherheit und Zuverlässigkeit des gesamten Geräts zu gewährleisten, dürfen Sie die Sicherheit der Maschine nicht durch Effizienz- und Schutzmaßnahmen zerstören.
- Die Bediener müssen mit dem Aufbau, der Leistung und den Betriebsabläufen der Kunststoff-Pelletiermaschine vertraut sein.
- Sobald die Materialtemperatur die eingestellte Temperatur nicht erreicht und die Haltezeit nicht ausreicht, darf die Schraube nicht eingeschaltet werden.
Über uns
Nanjing Granuwel Machinery CO., LTD ist auf die Forschung und Entwicklung sowie die Herstellung von Hochpolymer-Extrudern spezialisiert. Unser Team aus Extrusionsexperten der Spitzenklasse liefert den richtigen Extruder für Ihren genauen Anwendungszweck.
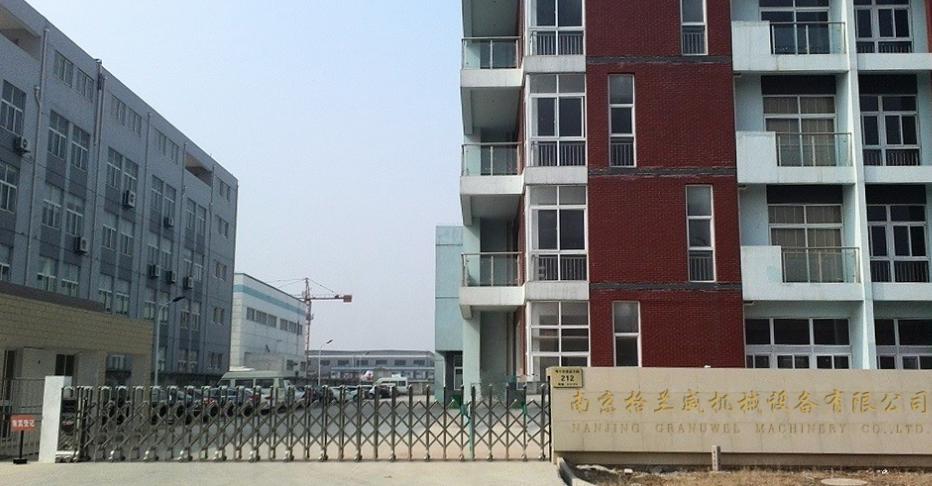
Wir verfügen über hervorragende Innovations- und Produktentwicklungsfähigkeiten und möchten unseren Kunden die besten Produkte bieten, indem wir auf Grundlage unserer praktischen Erfahrungen und technischen Innovationen die Gerätestruktur verbessern und den Energieverbrauch der Geräte senken.
Bei Fragen oder Anfragen können Sie sich jederzeit gerne an uns wenden!!!
Tel: +86-25-86199956
Handy: +86-13813371123
Netz: https://toolant.net