Wenn wir eine Masterbatch-Maschine zur Herstellung von Masterbatches verwenden, stoßen wir häufig auf einige Probleme, sodass wir kein qualifiziertes Masterbatch erhalten. Beispielsweise ist eine ungleichmäßige Dispersion in schwarzem Masterbatch eines der üblichen Probleme während des Produktionsprozesses.
Dieser Artikel stellt zwei häufige Probleme vor, die bei der Verwendung einer Masterbatch-Maschine auftreten.
Inhaltsverzeichnis
Umschalten1. Ungleichmäßige Dispersion des Rußphänomens
sind Sie verwirrt oder nicht? Während des Herstellungsprozesses des schwarzen Masterbatches, das 40%-Ruß enthält und EVA-Wachs als Dispergiermittel verwendet, können Inkonsistenzen in der Dispersion des Rußes beobachtet werden. Diese Inkonsistenz äußert sich darin, dass einige Streifen sehr spröde sind, während andere unzerbrechlich sind. Bei der Herstellung wird ein Doppelschneckenextruder verwendet, bei dem die Mischung einer Vormischung mit einem Hochmischer unterzogen wird, bevor sie in den Trichter gegeben wird. Die Temperatur reicht von 160 °C bis 180 °C, wobei die Kopftemperatur auf 175 °C eingestellt ist.
Problem der ungleichmäßigen Dispersion bei der Masterbatch-Herstellungsmaschine
Häufiges Reißen der Streifen
Das Material im Trichter fällt nicht gleichmäßig nach unten, was häufig zum Brechen der Streifen führt. Zunächst wurde vermutet, dass es an Material mangelt, doch beim Einfüllen stellte sich heraus, dass sich im Trichter zu viel Material befand, das manuell nachgeschoben werden musste. Interessanterweise tritt dieses Problem nicht auf, wenn der Rußgehalt 20% oder 30% beträgt.
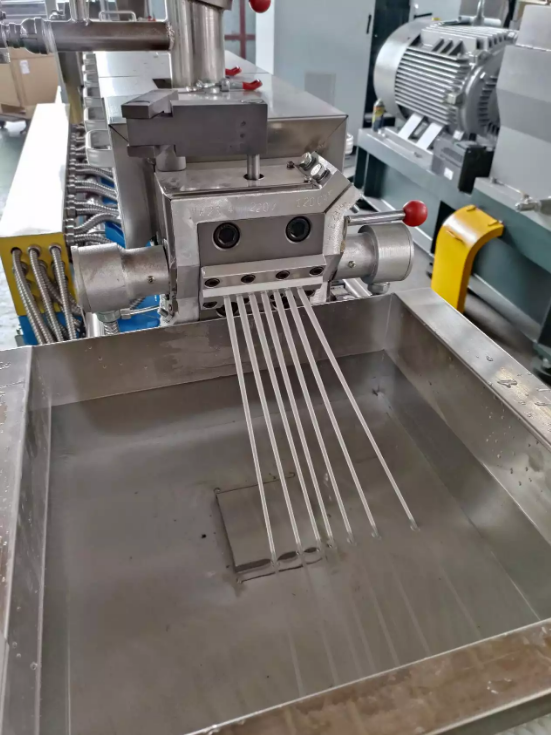
Inkonsistenz in der Geschwindigkeit des Matrizenkopfes
Darüber hinaus brechen die Streifen weiter, wenn Material vorhanden ist, und es gibt eine merkliche Inkonsistenz bei der Geschwindigkeit der Auslassöffnungen. Insbesondere die beiden mittleren Öffnungen arbeiten im Vergleich zu den anderen beiden Öffnungen schneller, was zu einer ungleichmäßigen Entladung führt.
Die ungleichmäßige Entladegeschwindigkeit des Maschinenkopfes wird genau durch die ungleichmäßige Verteilung des Materials verursacht. Schlecht verteilte Materialien haben eine schlechte Mobilität und gleichmäßig verteilte Materialien haben eine gute Mobilität. Das Material mit schlechter Fließfähigkeit bleibt zwangsläufig an der Innenwand des Strömungskanals haften. Die Entladung der beiden Enden der Führung ist langsam und die Entladung des Mittelstreifens ist schnell.
Leider gibt es keine Methode zur Erkennung vor Ort und das Masterbatch wird direkt für die Produktion verwendet. Daher fehlt das Verständnis dafür, wie sich die Qualität des Masterbatches einfach beurteilen lässt.
Lösung
Zur Behebung der aufgetretenen Probleme können mehrere potenzielle Lösungen implementiert werden.
Erhöhung der Menge an EVA-Wachs
Erstens kann eine Erhöhung der EVA-Wachsmenge im Herstellungsprozess zu einer besseren Dispersion des Rußes beitragen und so die Streifenqualität verbessern.
Reduzierung der Temperatur um 10℃
Darüber hinaus kann eine Reduzierung der Temperatur um 10 °C zur Optimierung der Verarbeitungsbedingungen und zur Verbesserung der Gesamtleistung des Masterbatches beitragen.
Passen Sie die Drehzahl des Doppelschneckenextruders an
Ein anderer Ansatz besteht darin, die Drehzahl des Doppelschneckenextruders anzupassen. Dies kann durch Reduzieren oder Erhöhen der Drehzahl erfolgen, um die optimale Einstellung zu finden, die eine gleichmäßigere und einheitlichere Streifenbildung ermöglicht.
Verwendung spezieller Mischschneckenelemente zur Verbesserung der Dispergierfähigkeit
Da Ruß eine komplexe und feine Struktur hat, besteht er aus vielen Schichten von Graphitmolekülen und zwischen jeder Schicht von Graphitmolekülen und anderen Schichten befinden sich winzige Lücken und Ecken. Seine Struktur ist eine mehrschalige Struktur, die durch die Ansammlung vieler Schichten von Graphitmolekülen gebildet wird. Die Moleküle jeder Schicht sind dick und dünn und können eine komplexe Schichtstruktur bilden. Daher besteht der idealste Zustand bei der Dispersion von Ruß darin, seine winzigen Lücken und Ecken nicht zu zerstören. Der üblicherweise verwendete Scherblock ist jedoch zu stark, was die Ecken der Rußmoleküle zerstört und dazu führt, dass Ruß agglomeriert. Daher wird ein spezielles Schraubgewinde verwendet. Originale wie S-Originale und Sechskantprismen-Originale verbessern die Verteilung und Mischfähigkeit von Ruß.
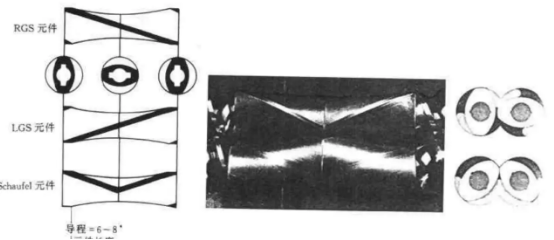
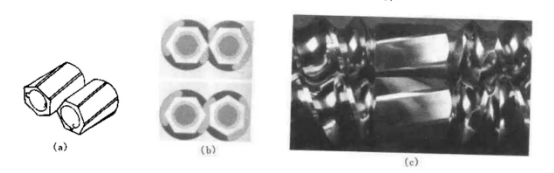
2. Brückenbildungsphänomen
Der Trichter dient als Lagereinheit für Kunststoffrohstoffe, und einige Trichter sind mit Heiz- und Blasmechanismen ausgestattet, um einen Trockentrichter zu bilden. Normalerweise ist der Trichter unten konisch und oben zylindrisch. Die optimale Neigung des konischen Abschnitts variiert je nach Faktoren wie Partikelgröße, Partikelform, Reibungskoeffizienten zwischen den Partikeln und Bindungskoeffizienten. Unter Brückenbildung versteht man die Nichtbeachtung dieser Faktoren, die zu einer Vergeudung von Trichterkapazität oder Problemen wie „Brückenbildung“ oder einem „Trichterrohreffekt“ führen kann, was wiederum eine schlechte Zufuhr oder ein Versagen der Materialentladung zur Folge hat. Das Brückenphänomen tritt auf, wenn sich der Durchmesser des Trichters in der Nähe der Einfüllöffnung des Extruders zu schnell verengt. Diese schnelle Durchmesseränderung führt dazu, dass das Material verdichtet und verfestigt wird, wodurch der Zufluss der Rohstoffe in den Extruder behindert wird.
Brückenbildungsproblem bei der Verwendung einer Masterbatch-Maschine
Plastikpartikel sammeln sich
Wenn sich Kunststoffpartikel ansammeln und an der schmalen Öffnung des Trichters eine offene Brücke bilden, die dem darüber liegenden Material Halt gibt, tritt das Brückenphänomen eher auf. Dies kommt besonders häufig bei recyceltem Material mit größeren Partikeln und unregelmäßigen Formen vor.
„Trichter in Röhren“-Effekt
Der „Trichter-in-Röhren“-Effekt kann zur Brückenbildung beitragen. Dies geschieht, wenn der Abwärtsfluss der Partikel nicht genügend Kraft hat, um die benachbarten Partikel zusammenzuziehen. Dies tritt häufiger auf, wenn die Kunststoffpartikel klein sind.
Das zu verpackende Material ist extrem leicht
Das Brückenbildungsphänomen ist tendenziell problematischer, wenn das zu verpackende Material extrem leicht ist oder einen hohen Füllstoffanteil enthält. Um die Brückenbildung zu minimieren oder zu vermeiden, müssen bestimmte Maßnahmen ergriffen werden. Dazu gehört die Trennung der Mischluft vom Pulver, bevor es in den Doppelschneckenextruder gelangt, die möglichst geringe vertikale Entfernung zwischen der Zufuhröffnung und der Schnecke und die Gewährleistung, dass das Pulver von unten in die Schnecke gelangt und nicht direkt von oben hinzugefügt wird. Die Schneckenstruktur sollte die Bewegung der Luft entlang der Schneckennut erleichtern und sie im Abgasabschnitt ablassen, während gleichzeitig verhindert wird, dass das Gas zum Ablassen zurück zur Zufuhröffnung strömt. Hersteller gehen das Problem der Brückenbildung häufig an, indem sie der Mischung 1-2%-Weißöl hinzufügen und es 2-3 Minuten lang kräftig mischen, sofern das Produkt dies zulässt. Es ist wichtig, auf die Mischzeit und -methode zu achten, da es im Allgemeinen besser ist, das Pulver in Agglomerate umzuwandeln. Dieser Ansatz entfernt effektiv Luft aus dem Füllstoff, verdichtet ihn in irgendeiner Form und eliminiert unerwünschte Luft. Sobald der Füllstoff agglomeriert, erhöht sich seine Schüttdichte und die Entfernung und Richtung der Zufuhr im Verhältnis zur Schneckennut verlieren an Bedeutung.
Lösung
Einbau einer Rüttelvorrichtung oder Reduzierung des Kegelspiels
Das Brückenphänomen in Trichtern kann durch den Einbau einer Vibrationsvorrichtung oder durch die Reduzierung der Kegelneigung behoben werden. Hohe Temperaturen im Trichter können dazu führen, dass Kunststoffpellets weich werden und sich verkleben, was zur Bildung von Brücken oder Verstopfungen führt. Beim Hinzufügen von Kalziumpulver können aufgrund seiner schlechten Fließfähigkeit und der Behinderung durch externe Schmiermittel Schwierigkeiten beim Entladen auftreten. Um dies zu überwinden, wird empfohlen, schweres Kalzium mit leichtem Kalzium zu mischen, den Einbau eines Vibrators in den unteren Trichter in Betracht zu ziehen und die Menge des internen Schmiermittels zu erhöhen. Der Einbau eines Vibrators ist die effektivste Lösung.
Temperaturkontrolle
Die Temperatur im Einzugsbereich des Extruders, wo das Material durch Reibungsschleppen transportiert wird, sollte zwischen 120 und 160 °C geregelt werden. Niedrige Temperaturen führen zu einem Materialmangel in der Schmelzzone, während hohe Temperaturen zu vorzeitigem Schmelzen und der Bildung eines schmierenden ringförmigen Schmelzfilms führen. Das Kompressionsverhältnis des Feststoffbetts im Einzugsbereich ist entscheidend, um die zum Schmelzen erforderliche Dichte zu erreichen. Partikelmaterialien lassen sich aufgrund ihrer Verformbarkeit leichter komprimieren, während Pulvermaterialien aufgrund ihrer Gleiteigenschaften und geringen Materialdichte bei der Kompression hinterherhinken, was zu langsameren Schmelz- und Absaugprozessen führt.
Durch den Einsatz spezieller Schneckenelemente kann die Förderleistung von Materialien verbessert werden.
Bezogen auf die Zufuhr einiger leichter, leicht zu schwebender Rohstoffe (wie etwa Ruß, Kalziumkarbonat in Nanogröße usw.) verwenden wir normalerweise einige Gewindeelemente mit großer Führung oder passen einige Gewindeelemente mit größerer Führung individuell an und verwenden eine spezielle Gewindestruktur – die den Winkel des Materialschubs auf einen rechten Winkel reduziert (Original SK-Gewinde) – um die Materialförderkapazität der Zufuhröffnung zu verbessern.
Verbesserung des Seitenverhältnisses im Zuführbereich
Die Verarbeitung von thermoplastischen Elastomerpartikeln, die eine hohe innere Reibung und Viskosität aufweisen, führt häufig zu Materialmangel, Schwankungen in der Produktionsausbeute und Materialabbau. Dem kann durch die Verbesserung des Längen-/Breitenverhältnisses des Zuführabschnitts, die Implementierung einer Zwangskühlung und den Einsatz einer Vibrationszuführung begegnet werden. Einige Granulierrohstoffe enthalten Elastomere, Füllöle, Füllstoffe, Harze und andere Komponenten, die die Materialzuführung aufgrund des Ölgehalts erschweren. Es wird im Allgemeinen nicht empfohlen, solche Materialien in sehr kleine Partikel zu zerkleinern. Darüber hinaus ist es notwendig, den Reibungskoeffizienten der Schneckenkante in der Zuführabschnittsschnecke zu erhöhen.
Richtig Vordispergierung
Wenn Pigment mit Harz gemischt und vordispergiert wird („Reibpulver“), muss auf eine ordnungsgemäße Dispersion geachtet werden. Das Dispergiermittel und der Vordispergierungsprozess während der Pigmentherstellung beeinflussen die Dispersion nach der Verarbeitung erheblich. Wenn der Toner nicht vordispergiert wird, kann dies zu einer ungleichmäßigen Mischung führen, die unterschiedliche Farben („Dekore“) in verschiedenen Bereichen des Materials verursacht. Hersteller von Mischungen sollten vorsichtig sein, wenn sie während der Produktion Farbabweichungen feststellen. Masterbatches, die mit einem Träger vordispergiert sind, sollten theoretisch keine schlechte Dispersion aufweisen. Es ist jedoch wichtig zu beachten, dass Träger derselben Farbe während der Verarbeitung unterschiedlich reagieren können. Erhebliche Unterschiede in der Massen-MFR zwischen dem Masterbatch und dem gemischten Harz können zu Farbmischungen führen. Wenn außerdem die natürliche Farbflexibilität des Masterbatches während des Mischvorgangs zur Bildung feiner Rückstände führt, kann dies zu unterschiedlichen Farbtönen im Endprodukt führen („Farbmischung“).
Über uns
Nanjing Granuwel Machinery Co., Ltd. ist auf die Forschung und Entwicklung sowie die Herstellung von Hochpolymer-Extrudern spezialisiert. Unser Team aus Extrusionsexperten der Spitzenklasse liefert den richtigen Extruder für genau Ihren Anwendungszweck.

Wir verfügen über hervorragende Innovations- und Produktentwicklungsfähigkeiten und möchten unseren Kunden die besten Produkte bieten, indem wir auf Grundlage unserer praktischen Erfahrungen und technischen Innovationen die Gerätestruktur verbessern und den Energieverbrauch der Geräte senken.
Bei Fragen/Anfragen können Sie sich gerne an uns wenden!!!
Tel: +86-25-86199956
Handy: +86-13813371123