Inhaltsverzeichnis
UmschaltenWas ist eine Anlage zum Extrudieren und Pelletieren abbaubarer Polymer-Masterbatches?
Abbaubare Polymer-Masterbatches – Extrusions- und Pelletieranlagen bezieht sich auf Spezialmaschinen, die bei der Herstellung abbaubarer Polymer-Masterbatches verwendet werden. Dabei handelt es sich um konzentrierte Mischungen aus abbaubaren Additiven und Polymeren.

Was ist abbaubares Masterbatch?
Das abbaubare Masterbatch bezieht sich auf kleine Körnchen einer konzentrierten Mischung biologisch abbaubarer Zusatzstoffe, die während der Herstellung hergestellt werden, um den Abbau unter bestimmten Umweltbedingungen zu beschleunigen. Um die Kosten zu senken, wird in dieser Masterbatch-Formel ein bestimmter Anteil an CaCO3, Maisstärke und anderen anorganischen Substanzen erhitzt. Gleichzeitig beschleunigen sie aufgrund der Eigenschaften von Maisstärke und CaCO3 den Abbau von Kunststoffprodukten. Die Zugabemenge variiert je nach Endprodukt zwischen 15 und 601 TP3T.
Arten von abbaubarem Masterbatch
Biologisch abbaubares Masterbatch:
Verbessert die biologische Abbaubarkeit von Kunststoffen und ermöglicht deren Zersetzung durch Mikroorganismen in natürliche Substanzen wie Wasser, Kohlendioxid und Biomasse.
Zu den Hauptbestandteilen des biologisch abbaubaren Masterbatches gehören:
- Basispolymere: PE, PP, PS.
- Photoabbaubare Additive: UV-Absorber, Photooxidantien, Metallstearate.
- Mischmittel: Kompatibilisierungsmittel, Weichmacher.
- Funktionelle Additive: Antioxidantien, Stabilisatoren, Farbstoffe.
- Füllstoff: CaCO3, Maisstärke usw.
Wird in Agrarfolien, Verpackungen und Outdoor-Produkten verwendet, um Plastikmüll durch lichtinduzierten Abbau zu reduzieren.
Photoabbaubares Masterbatch:
Enthält Zusatzstoffe, die den Abbau bei Sonneneinstrahlung, typischerweise UV-Licht, fördern.
Zu den Hauptbestandteilen des photoabbaubaren Masterbatches gehören:
- Basispolymere: Polyethylen (PE), Polypropylen (PP), Polystyrol (PS).
- Photoabbaubare Additive: UV-Absorber, Photooxidantien und abbaufördernde Zusatzstoffe (z. B. Metallstearate).
- Mischmittel: Kompatibilisierungsmittel und Weichmacher für eine gleichmäßige Dispersion und verbesserte Verarbeitbarkeit.
- Funktionelle Additive: Antioxidantien, Stabilisatoren und Farbstoffe.
- Füllstoff: CaCO3, Maisstärke usw.
Diese Materialien werden in Anwendungen wie Agrarfolien, Verpackungen und Outdoor-Produkten eingesetzt, um Plastikmüll zu reduzieren, indem der Abbau bei Lichteinwirkung beschleunigt wird.
Oxoabbaubares Masterbatch:
Verwendet Zusatzstoffe, die die Oxidation und Fragmentierung von Kunststoffen bei Einwirkung von Hitze und Sauerstoff beschleunigen, sodass diese schließlich in Mikroplastik zerfallen, das dann durch Mikroorganismen biologisch abgebaut wird.
Zu den Hauptbestandteilen des oxoabbaubaren Masterbatches gehören:
- Basispolymere: PE, PP, PS.
- Oxoabbaubare Additive: Metallstearate, abbaufördernde Zusatzstoffe.
- Mischmittel: Kompatibilisierungsmittel, Weichmacher.
- Funktionelle Additive: Antioxidantien, Stabilisatoren, Farbstoffe.
- Füllstoff: CaCO3, Maisstärke usw.
Wird in Verpackungen, Agrarfolien und Einwegprodukten verwendet, um Plastikmüll durch beschleunigte Oxidation und anschließenden biologischen Abbau zu reduzieren.
Ganz gleich, welche Art von abbaubarem Masterbatch Sie produzieren müssen, unsere Extrusions- und Pelletierproduktionslinie kann Ihnen dabei helfen, eine effiziente und qualitativ hochwertige Produktion zu erreichen.
Ganz gleich, welche Art von abbaubarem Masterbatch Sie herstellen müssen – die Extrusions- und Pelletierproduktionslinie von Granuwel unterstützt Sie bei einer effizienten und qualitativ hochwertigen Produktion.
Wie wird abbaubares Masterbatch hergestellt?
Abbaubare Masterbatches werden in Extrusions- und Pelletieranlagen für abbaubare Masterbatches hergestellt, wie in der Abbildung unten dargestellt.

Die Produktion umfasst mehrere wichtige Schritte, von der Auswahl der Rohstoffe bis zum abschließenden Extrusions- und Pelletierungsprozess. Hier ist eine detaillierte Aufschlüsselung, wie abbaubare Masterbatches hergestellt werden:
1. Auswahl der Rohstoffe
- Basispolymer: Häufig verwendete Polymere wie Polyethylen (PE), Polypropylen (PP) oder andere Arten von Kunststoffharzen.
- Füllstoff: CACO3-Pulver, Maisstärkepulver, im Allgemeinen Maschenweite größer als 1250 Maschen
- Abbaubare Zusatzstoffe: Hierzu zählen Stoffe, die den Abbau fördern, wie etwa organische Verbindungen, Metallstearate oder stärkebasierte Zusatzstoffe.
- Andere Zusatzstoffe: Abhängig von den gewünschten Eigenschaften können weitere Zusatzstoffe wie Antioxidantien, UV-Stabilisatoren und Weichmacher enthalten sein.
2. Wiegen und Mischen
- Genaues Wiegen: Die Rohstoffe werden genau abgewogen, um die richtigen Anteile an Basispolymer und abbaubaren Zusatzstoffen sicherzustellen.
- Vormischen: Um eine gleichmäßige Verteilung der Zusatzstoffe zu gewährleisten, werden die Materialien vorgemischt, bevor sie in den Extrusionsprozess gelangen.

Weitere Optionen: Die Gewichtsabnahme kann verwendet werden, um den Doppelschneckenwirt automatisch entsprechend der Rezepturanteile zu füttern. Dadurch wird eine Umweltverschmutzung durch Staub während des Mischvorgangs des Hochgeschwindigkeitsmischers vermieden. Dies kann auch die Arbeitsintensität der Arbeiter verringern. Es muss jedoch beachtet werden: CaCO3 und Maisstärke müssen beschichtete Materialien sein.
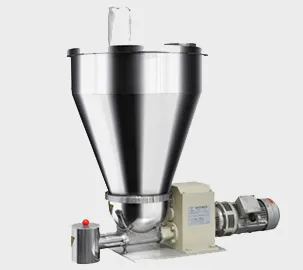
3. Extrusionsprozess
- Fütterung: Die vorgemischten Materialien werden über ein Dosiersystem (volumetrisch oder gravimetrisch) in den Extruder gefördert.
- Schmelzen und Compoundieren: Im Extruder werden die Materialien erhitzt, um das Basispolymer zu schmelzen. Der Schneckenmechanismus vermischt das Polymer mit den abbaubaren Zusatzstoffen und sorgt so für eine homogene Mischung.
- Doppelschneckenextruder: Aufgrund der besseren Mischfähigkeit für komplexere Formulierungen bevorzugt.
4. Formen und Abkühlen:
- Schneidkopf: Die geschmolzene Mischung wird durch einen Düsenkopf gedrückt und so in durchgehende Stränge geformt.
- Kühlung: Die extrudierten Stränge werden gekühlt, normalerweise mit Luftkühlsystemen, um das Material zu verfestigen. Es wird empfohlen, luftgekühlte Streifen zu verwenden und möglichst keine Wasserkühlung zu verwenden. Denn die Partikel zersetzen sich bei Kontakt mit Wasser und aufgrund des einen Meters Stärke nehmen sie Wasser auf. Anschließend muss getrocknet werden.
5. Pelletieren:
Schneiden: Die abgekühlten Stränge werden mit einem Pelletierer in gleichmäßige Pellets geschnitten. Dies kann erfolgen mit:
- Strangpelletierer: Schneidet die Stränge nach dem Abkühlen.
- Unterwasserpelletierer: Schneidet die Stränge, während sie sich noch im Wasser befinden, um gleichmäßigere Pelletgrößen zu erzielen.
6. Trocknen:
Feuchtigkeit entfernen: Die Pellets werden getrocknet, um die restliche Feuchtigkeit zu entfernen. Hierzu werden beispielsweise folgende Methoden eingesetzt:
- Zentrifugaltrocknung: Nutzt die Zentrifugalkraft, um Wasser zu entfernen.
- Wirbelschichttrocknung: Verwendet heiße Luft zum Trocknen der Pellets.
7. Sieben und Klassieren:
- Einheitliche Größe: Die Pellets werden gesiebt und klassifiziert, um sicherzustellen, dass sie eine einheitliche Größe haben und frei von zu großen oder zu kleinen Partikeln sind.
8. Qualitätskontrolle:
Während des gesamten Produktionsprozesses werden Qualitätskontrollmaßnahmen durchgeführt, um sicherzustellen, dass das abbaubare Masterbatch die erforderlichen Spezifikationen und Leistungsstandards erfüllt. Dazu gehören:
- Testen: Proben werden auf Konsistenz, Abbaueigenschaften und andere relevante Parameter getestet.
- Anpassungen: Um die Produktqualität aufrechtzuerhalten, werden alle notwendigen Anpassungen an der Formulierung oder den Prozessbedingungen vorgenommen.
Vorteile der Verwendung abbaubarer Masterbatches
Auswirkungen auf die Umwelt: Beschleunigt den Abbau von Kunststoff und reduziert so die langfristige Abfallansammlung.
Kostengünstig: Bietet im Vergleich zu vollständig biologisch abbaubaren Kunststoffen eine kostengünstige Lösung.
Vielseitigkeit: Kompatibel mit verschiedenen Polymeren und Anwendungen, einschließlich Verpackung und Landwirtschaft.
Ressourceneffizienz: Nutzt erneuerbare Ressourcen und reduziert die Abhängigkeit von fossilen Brennstoffen.
Einhaltung gesetzlicher Vorschriften: Hilft bei der Einhaltung von Umweltvorschriften und -standards.
Verbesserte Produktleistung: Verbessert Eigenschaften wie Flexibilität, Festigkeit und UV-Beständigkeit.
Markenimage: Verbessert die Nachhaltigkeitsnachweise und spricht umweltbewusste Verbraucher an.
Abfallmanagement: Reduziert die mit der Abfallentsorgung und -bewirtschaftung verbundenen Kosten.
Wenn Sie weitere Fragen zur Extrusion und Pelletierung von abbaubaren Polymer-Masterbatches haben, wenden Sie sich bitte an GRANUWEL MASCHINEN.