Tabla de contenido
PalancaIntroducción:
En la fabricación moderna, la aplicación de plásticos sensibles al calor se está extendiendo cada vez más debido a sus propiedades físicas y químicas únicas, lo que los convierte en una opción ideal para numerosos sectores industriales. Sin embargo, el procesamiento de plásticos sensibles al calor plantea desafíos importantes porque se degradan y decoloran fácilmente a altas temperaturas. Estas características dificultan el cumplimiento de los requisitos de producción utilizando tecnologías de procesamiento tradicionales. La estructura molecular de los plásticos sensibles al calor puede descomponerse fácilmente en entornos de alta temperatura, lo que reduce el rendimiento del material, como la decoloración y la resistencia debilitada. Las extrusoras tradicionales de un solo tornillo presentan limitaciones al plastificar plásticos sensibles al calor, particularmente en la entrega de fuerza de corte y la regulación de la temperatura. Esto a menudo da como resultado una plastificación desigual o una degradación excesiva del material, lo que afecta la calidad y la consistencia del producto y aumenta las tasas de desechos y los costos. Para abordar este desafío, las extrusoras de dos etapas ofrecen una solución eficiente. Compuesto por un mezclador de doble tornillo co-rotativo de alta velocidad tipo GTE y una extrusora de un solo tornillo de baja velocidad serie GDS, estas dos partes están dispuestas verticalmente de manera ortogonal, trabajando juntas para lograr una plastificación eficiente y una mezcla uniforme mientras se evitan problemas de degradación por sobrecalentamiento. El siguiente texto profundizará en las características técnicas, ejemplos de aplicación y estrategias de uso optimizadas de las extrusoras de dos etapas en el procesamiento de plásticos sensibles al calor, mostrando completamente su potencial innovador y amplias perspectivas de aplicación en la tecnología de procesamiento moderna, especialmente cómo a través de su diseño único de dos etapas y descomposición del proceso, se logra el control independiente y la optimización de cada paso de procesamiento, mejorando la eficiencia de producción y la tasa de utilización del material.
Desafíos en el procesamiento de plásticos sensibles al calor:
- Los plásticos sensibles al calor son propensos a sufrir cambios químicos y físicos a altas temperaturas, lo que plantea importantes desafíos para su procesamiento. Cuando se exponen a entornos de alta temperatura, su estructura molecular comienza a cambiar, lo que lleva a una reducción severa de sus propiedades físicas. Las altas temperaturas pueden acelerar la rotura de las cadenas de polímeros, lo que provoca una disminución del peso molecular, que a su vez afecta la resistencia mecánica y la estabilidad química del material. En el caso de los plásticos sensibles al calor, como el cloruro de polivinilo (PVC) y el polioximetileno (POM), no solo se produce decoloración, sino que también pueden liberarse gases nocivos, lo que afecta no solo a la calidad del producto final, sino que también puede contaminar el entorno de producción.
- Las extrusoras monohusillo tradicionales tienen limitaciones obvias al procesar estos materiales. Debido a sus limitaciones de diseño, las extrusoras monohusillo no pueden proporcionar suficiente fuerza de corte para garantizar una plastificación uniforme de los plásticos sensibles al calor. Además, estas máquinas suelen emplear calefacción eléctrica con refrigeración por ventilación de la superficie externa, por lo que el control de la temperatura no es lo suficientemente preciso, lo que fácilmente da lugar a sobrecalentamientos en áreas durante el procesamiento, lo que provoca la degradación local o completa del material. Dado que los plásticos sensibles al calor deben procesarse a temperaturas más bajas y con velocidades de corte precisas, estas deficiencias de las extrusoras monohusillo se convierten en cuellos de botella a la hora de mejorar la calidad del producto y la eficiencia de la producción.
- El uso de tecnología tradicional para procesar plásticos sensibles al calor a menudo conduce a una calidad inconsistente del producto y mayores tasas de desechos. La plastificación desigual y la degradación del material pueden causar inestabilidad en el rendimiento del producto final, aumentando los costos de producción y reduciendo la competitividad de mercado de una empresa. Estos problemas resaltan la necesidad de buscar tecnologías de procesamiento más avanzadas y precisas. Para superar estos desafíos, la aplicación de unidades de mezcla de dos etapas se ha convertido en un gran avance en el campo del procesamiento de plásticos sensibles al calor. Sus características estructurales incluyen: la primera etapa utiliza una máquina de doble tornillo co-rotativo de alta velocidad tipo GTE para mezclar en un barril abierto con presión casi cero, y la segunda etapa es una extrusora de un solo tornillo de baja velocidad GDE que extruye el material mezclado y madurado a baja velocidad y temperatura, evitando así la degradación térmica y controlando y optimizando con precisión los efectos de mezcla. La máquina de dos etapas no solo mejora la calidad del producto, sino que también reduce significativamente las tasas de desechos, lo que aporta importantes beneficios económicos y técnicos a las empresas manufactureras.

Características técnicas de la extrusora de dos etapas Nanjing Granuwel:
- La primera etapa es una mezcladora de doble tornillo co-rotativo de alta velocidad tipo GTE, y la segunda etapa es una extrusora de un solo tornillo de baja velocidad serie GDS, ambas dispuestas verticalmente de manera ortogonal para formar una unidad compuesta de dos etapas. Este diseño combina las ventajas del doble tornillo y del tornillo único, logrando una mezcla de plastificación eficiente y una dispersión por cizallamiento, al mismo tiempo que evita contradicciones entre el sobrecalentamiento por cizallamiento alto y la extrusión a alta presión.
- El tornillo doble refuerza el transporte, asegurando una mezcla uniforme y plastificación del material durante el procesamiento. Su estructura única de tornillo promueve mejores efectos de mezcla, permitiendo que los plásticos sensibles al calor se calienten y mezclen de manera uniforme. La forma geométrica y la configuración del tornillo se calculan cuidadosamente para maximizar sus efectos de cizallamiento y distribución sobre el material, mejorando así la fluidez del material y la eficiencia del procesamiento.
- El tornillo único realiza una extrusión a alta presión, pero adopta un método de baja velocidad y bajo esfuerzo cortante, evitando igualmente contradicciones por sobrecalentamiento. Este diseño permite que la extrusora de dos etapas mantenga la calidad del producto a la vez que mejora la eficiencia de producción y reduce los costos de producción.
- La combinación de tornillo doble y tornillo simple descompone las funciones del proceso, aumentando las variables operativas independientes, lo que favorece la optimización gradual de cada proceso. Esta multifuncionalidad no solo garantiza la calidad del producto, sino que también mejora la eficiencia de la producción y reduce los costos de producción.
- La extrusora de dos etapas se utiliza ampliamente en diversos sistemas de materiales sensibles al calor y operaciones de desvolatilización de gran capacidad, como PVC, XLPE, materiales de cable retardantes de llama sin halógenos, materiales de protección, materiales de negro de carbono de alta concentración y operaciones de posprocesamiento después de la deshidratación del caucho. Al simplificar el proceso de operación y mejorar la utilización del material, la extrusora de dos etapas proporciona una solución rentable para las empresas manufactureras, que satisface plenamente las necesidades de la fabricación moderna.
Los métodos de granulación adecuados también pueden reducir el riesgo de sobrecalentamiento de los materiales sensibles al calor. Sin embargo, debido a la tendencia del PVC a absorber agua, generalmente se utiliza el corte en caliente enfriado por aire; la mayoría de los materiales sensibles al calor deben adoptar métodos de granulación por anillo de agua o bajo el agua: Los sistemas de granulación por anillo de agua y los sistemas de granulación bajo el agua funcionan bien con extrusoras de dos etapas en el procesamiento de plásticos sensibles al calor. A través de mecanismos de enfriamiento efectivos, garantizan la estabilidad de los materiales sensibles durante el procesamiento, lo que reduce los problemas de degradación del material causados por las altas temperaturas.
Sistema de peletización de anillo de agua:
En el punto donde se corta la tira de plástico, se rocía agua para formar una banda circular de agua. Esta banda de agua no solo rodea la tira de plástico recién cortada, sino que también enfría rápidamente el material mediante el efecto de enfriamiento rápido del agua. Este proceso de enfriamiento rápido es crucial para los plásticos sensibles al calor porque evita que el material se exponga a altas temperaturas durante demasiado tiempo, protegiendo así las propiedades físicas y químicas del material. Una ventaja adicional de la granulación con anillo de agua es su operación relativamente simple, los bajos costos de mantenimiento y la capacidad de acomodar tiras de plástico de diferentes tamaños y formas, lo que ofrece una solución económica y eficaz.
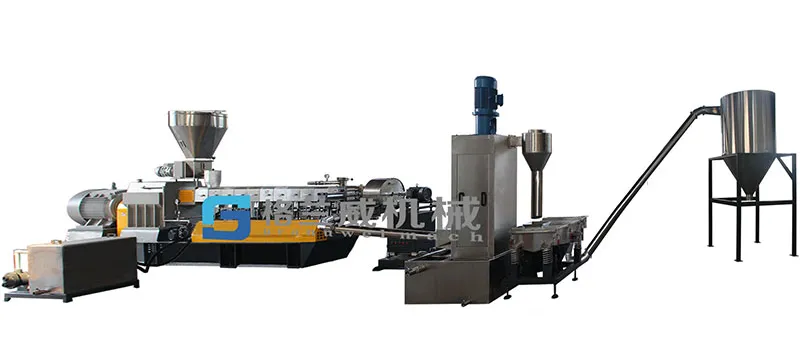
Sistema de peletización subacuática:
El proceso de corte de la tira de plástico se lleva a cabo completamente bajo el agua. Cuando se corta la tira de plástico, cae directamente al agua. El agua no solo actúa como medio de enfriamiento, sino que también transporta las partículas cortadas al siguiente paso de procesamiento. La mayor ventaja de este método es la eliminación extremadamente rápida del calor generado por los materiales sensibles, eliminando casi por completo el riesgo de daños materiales causados por el sobrecalentamiento. La granulación bajo el agua garantiza la conservación de las características del material, especialmente adecuada para plásticos sensibles al calor que son muy susceptibles a la temperatura. Aunque los sistemas de granulación bajo el agua pueden requerir equipos más complejos e inversiones iniciales más altas, sus beneficios a largo plazo en el mantenimiento de la calidad del producto y la reducción de las tasas de desechos son significativos.

Ejemplos de aplicación:
En el campo del procesamiento de plásticos sensibles al calor, la aplicación de extrusoras de dos etapas se está extendiendo cada vez más, con sus ventajas particularmente evidentes al manipular materiales como el cloruro de polivinilo y el polioximetileno. Por ejemplo, las empresas que se centran en la producción de materiales para cables de PVC se enfrentan a problemas de baja eficiencia de producción y calidad inestable del producto. Al introducir extrusoras de dos etapas, las empresas no solo aumentan significativamente la producción de materiales para cables de PVC, sino que también reducen los problemas de degradación del material causados por temperaturas excesivas. El control preciso de la temperatura y las capacidades de mezclado uniforme de las extrusoras de dos etapas garantizan la consistencia de la calidad de los materiales para cables de PVC, al tiempo que reducen las tasas de desechos y mejoran la eficiencia general de la producción.
Los estudios de casos muestran que las extrusoras de dos etapas no solo optimizan el proceso de procesamiento y aumentan la producción al manipular plásticos sensibles al calor como el PVC y el POM, sino que también garantizan la consistencia de la calidad del producto mediante un control preciso del proceso. Esto representa un enorme beneficio técnico y económico para las empresas de producción que persiguen estándares de alta calidad.
Conclusión:
Gracias a su investigación y aplicación en el campo del procesamiento de plásticos sensibles al calor, la extrusora de dos etapas de Granuwel se ha convertido en un equipo fiable que mejora enormemente el proceso de producción y la calidad del producto. Mediante un control preciso de la temperatura y la velocidad de corte, la extrusora de dos etapas resuelve muchos de los desafíos que enfrentan las extrusoras tradicionales de un solo tornillo al procesar plásticos sensibles al calor, como la degradación del material, la mezcla desigual y la baja eficiencia de producción. Este avance tecnológico no solo mejora la eficiencia de procesamiento de los plásticos sensibles al calor, sino que también garantiza altos estándares en cuanto a color, resistencia y consistencia del producto.
Las empresas manufactureras han obtenido importantes beneficios económicos y competitivos al adoptar la tecnología de extrusoras de dos etapas. Los ahorros de costos se reflejan en una reducción del desperdicio de material, un menor consumo de energía y una disminución de los gastos de mantenimiento. Mientras tanto, debido a la mejora de la consistencia y la calidad del producto, las empresas pueden mejorar la competitividad de sus productos en el mercado, atraer más clientes y ampliar la participación en el mercado. Estos beneficios económicos directos e indirectos hacen que la extrusora de dos etapas sea un equipo esencial para cualquier empresa comprometida con la mejora de los estándares de producción y la rentabilidad.
A medida que la preocupación por la protección del medio ambiente y la producción sostenible sigue creciendo, las futuras extrusoras de dos etapas también se centrarán más en optimizar la eficiencia energética y las tasas de utilización de materiales. Además, con el desarrollo de los mercados emergentes y la diversificación de las demandas industriales, las extrusoras de dos etapas se adaptarán a una gama más amplia de materiales y campos de aplicación, lo que hará mayores contribuciones a la innovación y el desarrollo en la fabricación global.