Tabla de contenido
Palanca¿Cuál es la diferencia entre extrusoras de plástico médicas y extrusoras de plástico industriales?
Respuesta breve:
Las extrusoras de plástico para uso médico y las extrusoras de plástico para uso industrial difieren en cuanto a diseño, aplicación y selección de materiales. Las primeras se centran más en la precisión del producto y los estándares de higiene, mientras que las segundas se centran más en la eficiencia de producción y la rentabilidad.
Las extrusoras médicas pueden requerir un mayor grado de automatización y control preciso para garantizar que las partículas de plástico producidas sean uniformes, densas y hermosas.
Las extrusoras industriales de un solo tornillo y de dos tornillos se centran más en la eficiencia de producción y la rentabilidad, y son adecuadas para la producción continua de grandes longitudes de productos plásticos.
Además, las extrusoras médicas pueden ser más estrictas en la selección de materiales y, por lo general, utilizan materiales como PVC de grado médico para cumplir con los requisitos especiales de los dispositivos médicos. Las extrusoras industriales pueden manipular una variedad de plásticos, incluidos termoplásticos, caucho, etc., y son adecuadas para una gama más amplia de aplicaciones industriales.

La extrusora de doble tornillo Thermofisher Process 16 facilita el desarrollo rápido y confiable de materiales en las industrias de polímeros, alimentos o farmacéutica. (Solo para uso en investigación. No apto para uso en procedimientos de diagnóstico).
Para obtener información más detallada sobre las extrusoras de plástico médico y las extrusoras de plástico industrial de doble tornillo, lea el contenido a continuación.
¿Qué es el plástico médico?
Los plásticos médicos suelen ser aquellos de grado médico que deben tener propiedades como biocompatibilidad, estabilidad química y resistencia al calor para garantizar que no provoquen reacciones adversas o infecciones al entrar en contacto con el cuerpo humano. Los plásticos médicos suelen estar hechos de polímeros sintéticos como polietileno (PE), polipropileno (PP), cloruro de polivinilo (PVC), etc., y se someten a rigurosas pruebas de biocompatibilidad para cumplir con estándares internacionales como la ISO 10993.
Los plásticos médicos sirven como materia prima que se utiliza para fabricar dispositivos médicos y equipos médicos, como jeringas, bolsas de infusión, dentaduras postizas, articulaciones artificiales, etc.



Gránulos de plástico de grado médico Fuente de la imagen:
¿Cómo se fabrican los plásticos médicos?
Todo el proceso de producción de grado médico debe cumplir con regulaciones como:
ISO 10993: Para pruebas de biocompatibilidad.
FDA 21 CFR: Para materiales destinados a uso médico.
ISO 13485: Para la gestión de la calidad en la fabricación de dispositivos médicos.
Selección de materia prima
Polímero base: A menudo se utilizan plásticos de alta pureza como polietileno (PE), polipropileno (PP), policarbonato (PC), politetrafluoroetileno (PTFE) y cloruro de polivinilo (PVC).
Aditivos: Sólo aditivos aprobados por la FDA Se permite el uso de estabilizadores, plastificantes y colorantes en la producción de gránulos de plástico de grado médico.
Purificación de materiales
El polímero base debe purificarse para eliminar contaminantes a fin de cumplir con los estándares de grado médico.
Este paso puede incluir otras técnicas de purificación como filtración, destilación, extracción, etc.
Compuesto (utilizando extrusor médico)
El polímero purificado se mezcla con aditivos en una extrusora médica para lograr las propiedades mecánicas, químicas y térmicas deseadas. En este paso, se ejecutan controles estrictos para evitar la contaminación durante la preparación.
La extrusora de doble tornillo Thermofisher Process 16 facilita el desarrollo rápido y confiable de materiales en las industrias de polímeros, alimentos o farmacéutica. (Solo para uso en investigación. No apto para uso en procedimientos de diagnóstico).
Para obtener más información sobre esta máquina de extrusión de doble tornillo, visite el sitio web de Thermofisher.
Prueba de materiales compuestos
El material compuesto debe someterse a pruebas rigurosas para lograr la biocompatibilidad y compatibilidad de esterilización requeridas.
(Biocompatibilidad: Para garantizar que no haya reacciones adversas con los tejidos humanos.
Compatibilidad de esterilización: Los materiales deben soportar métodos de esterilización comunes, como autoclave, gas de óxido de etileno (EO) o irradiación gamma.
Moldeado y conformación
El plástico médico se forma en las formas requeridas utilizando técnicas como extrusión, moldeo por inyección, moldeo por soplado, etc.
Esterilización y envasado
Los productos plásticos para uso médico terminados se esterilizan para eliminar la contaminación microbiana y luego se envasan en un entorno de sala limpia para mantener la esterilidad.
¿Qué es el plástico de uso industrial?
Los plásticos industriales son materiales sintéticos o semisintéticos diseñados específicamente para su uso en aplicaciones industriales. Para adaptarse a entornos exigentes y propósitos especializados, los plásticos industriales también deben combinarse y modificarse para lograr ciertas características, como durabilidad, resistencia al calor, resistencia química, versatilidad, ligereza, etc.
Los plásticos industriales se utilizan principalmente en campos industriales generales.
Construcción: Tuberías de PVC, láminas para techos y materiales aislantes.
Automotriz: Tableros, parachoques y componentes debajo del capó.
Embalaje: Películas industriales, contenedores y envoltorios protectores.
Electrónica: Cables, carcasas y materiales aislantes.
Agricultura: Películas para invernaderos y tuberías de riego.
¿Cómo se fabrican los plásticos industriales?
Selección de materia prima
Polímeros base: Los polímeros comúnmente utilizados incluyen polietileno (PE), polipropileno (PP), policarbonato (PC), cloruro de polivinilo (PVC) y politetrafluoroetileno (PTFE).
Aditivos: Dependiendo de la aplicación, se pueden agregar aditivos como estabilizadores, plastificantes, colorantes y rellenos para mejorar propiedades específicas como resistencia, flexibilidad o resistencia al calor.
Polimerización
El polímero base se crea a través de procesos químicos como:
Polimerización por adición: Para plásticos como PE y PP.
Polimerización por condensación: para plásticos de ingeniería como poliamidas (nailon).
Los monómeros se unen químicamente para formar largas cadenas de polímeros, creando el tipo de plástico deseado.
Compuesto (utilizando máquinas para mezclar plástico)
El polímero base se combina con aditivos en una extrusora de compuestos para lograr las características deseadas.
Los ingredientes se funden, se mezclan y se homogeneizan para garantizar una distribución uniforme de los aditivos.
El producto resultante se enfría y se peletiza en gránulos o masterbatch para su posterior procesamiento.


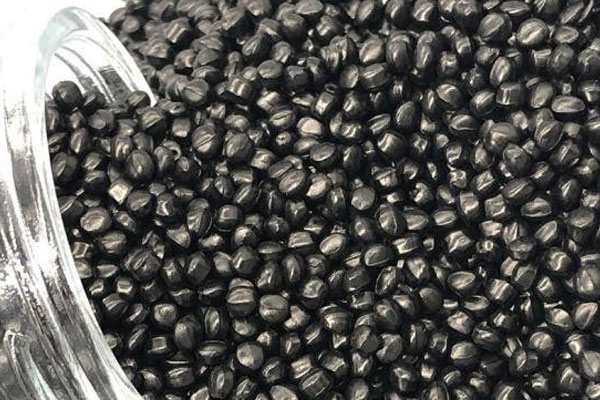

Dar forma y moldear
Los plásticos industriales se moldean hasta obtener formas utilizables mediante diversas técnicas:
Moldeo por inyección: ideal para piezas complejas como componentes de automóviles o carcasas de máquinas.
Extrusión: Se utiliza para productos continuos como tuberías, tubos y láminas.
Moldeo por soplado: Adecuado para productos huecos como tanques y contenedores industriales.
Moldeo por compresión: a menudo se utiliza para plásticos termoendurecibles de alta resistencia.
Termoformado: para dar forma a láminas de plástico en componentes grandes y livianos.
Granuwel es un fabricante profesional de extrusoras industriales de doble tornillo para plástico en China. Nuestras máquinas de extrusión se pueden utilizar para producir algunos productos plásticos para masterbatches de polímeros para la producción de algunos marcos de dispositivos médicos, barreras de protección, etc. Con nuestras décadas de experiencia en el desarrollo y fabricación de extrusoras de doble tornillo, Granuwel confía en brindarle máquinas de extrusión de alta calidad y soluciones que se adapten mejor a sus necesidades. ¡No dude en contactarnos si tiene alguna pregunta sobre nuestras máquinas de extrusión!