Table of Contents
ToggleIntroduction
Co-rotating parallel twin-screw extruders play a crucial role in the processing and modification of polymer materials. With their unique structural design and efficient mixing capabilities, they have become powerful tools for achieving precise control and modification of polymer materials. In recent years, with the increasing awareness of environmental protection and the demand for sustainable development, the degradability of polymer materials has become a hot research topic. This article will delve into the application and advantages of co-rotating parallel twin-screw technology in the field of polymer material degradation.
Overview of Co-Rotating Parallel Twin-Screw Extruders
Co-rotating parallel twin-screw extruders consist of two screws that rotate parallel to each other in the same direction within a barrel. They rotate within the barrel and, through the interaction of the threads, convey, compress, mix, and plasticize materials. The characteristics of this equipment include high shear force, excellent self-cleaning ability, and flexible process adjustment, making it widely applicable in polymer material processing.
Challenges of Polymer Material Degradation
Polymer materials such as plastics and rubber are difficult to degrade in natural environments, and long-term accumulation can cause serious damage to ecosystems. Therefore, the development of technologies that can promote or achieve the degradation of polymer materials is particularly important. Degradation of polymer materials typically requires physical, chemical, or biological methods, and co-rotating parallel twin-screw extruders demonstrate unique advantages in this process.
Application of Co-Rotating Parallel Twin-Screws in Degradation
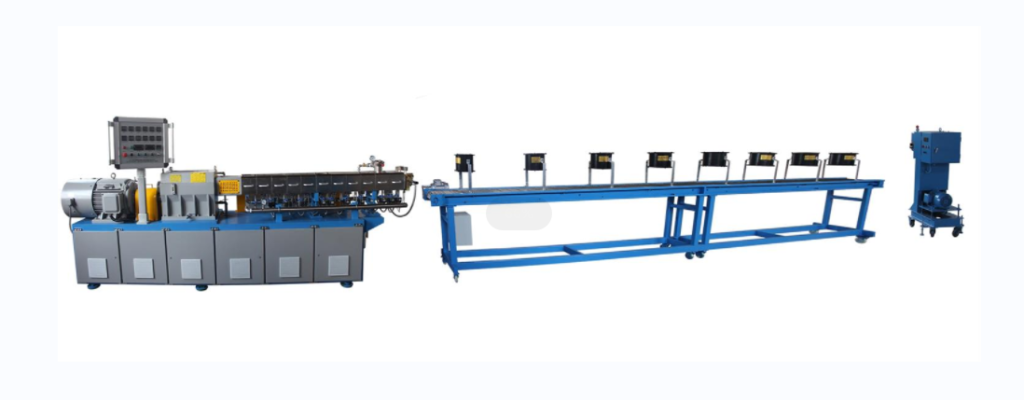
Physical degradation: Co-rotating parallel twin-screw extruders can reduce the molecular weight of polymer materials through intense shear force and high temperature conditions, thereby achieving physical degradation. This method is suitable for processing materials that are difficult to degrade through chemical or biological methods.
Chemical degradation: Specific chemical agents, such as peroxides, can be added in co-rotating parallel twin-screw extruders to initiate chemical reactions in polymer materials, promoting their degradation. This method can be carried out under controlled conditions, reducing environmental pollution.
Biological degradation: Through the mixing function of co-rotating parallel twin-screw extruders, biodegradable additives such as enzymes or microorganisms can be uniformly dispersed into polymer materials, enhancing their biodegradation performance.
Advantages of Co-Rotating Parallel Twin-Screws
Efficient mixing: Ensures uniform dispersion of degradation agents and other additives.
Precise control: Allows precise control of temperature, pressure, and residence time, optimizing the degradation process.
Flexibility: Applicable to various polymer materials and different types of degradation processes.
Energy saving and environmental protection: Lower energy consumption compared to traditional methods, reducing environmental impact.
Conclusion
The application of co-rotating parallel twin-screw extruders in the field of polymer material degradation demonstrates its versatility and efficiency. With continuous technological advancements and increasing environmental requirements, the role of co-rotating parallel twin-screw extruders in promoting the degradation of polymer materials will receive more attention. Through ongoing technological innovation and process optimization, co-rotating parallel twin-screw extruders are expected to make greater contributions to achieving the green and sustainable development of polymer materials.