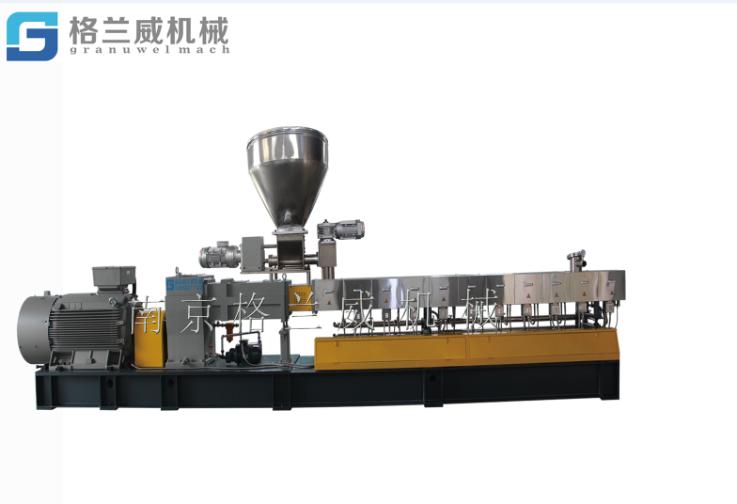
Table of Contents
TogglePreface
Twin Screw screw extruders are used very widely, besides plastic compounding, they’re also used in a wide variety of other industries such as pharma, biotech, food, aerospace and medical manufacturing and, 3D printing field. During the crisis of the Covid-19,the total whole world market for Co-rotating Twin Screw Extruders estimated around US$935.9 Million in 2020, and will be reach to US$1 Billion in 2027, according on researcher’s predict.
The co-rotating twin screw extruder has been gaining popularity recently because of its high performance and versatility, however there’re not all people know how it works to produce these or what factors may affect its performance that would lead to failures or product defects during production.
As for this reason, we will go over the basic components of co-rotating twin screw extruder and describe its functions and the effects that have on your product.
The basic concept behind a co-rotating twin screw extruder is that there are one pair screw combinations and some barrel sections. The material screws spin inside of each other in same directions which creates a compounding or reacting process known as mixing or homogeny.
To achieve this, the barrel sections are designed in such a way that the materials can be deposited at different rates, allowing for co-mixing.
This one can be based on the design of the internal material of the double-barrel machine without considering the characteristics of the internal light source, the heat dissipation of the matrix, etc., and at the same time, the appropriate material can be selected according to the characteristics of the processing point.
And based on this, the design of the Co-rotating twin-screw barrel should not only considering the rationality of the internal cooling channels, the matrix thermal conductivity, etc. meanwhile, choosing the appropriate materials selection according to the characteristics of the processed materials is also need to take into consideration. For example, when the raw material is PA+GF, the basal body /matrix of barrel is #45 steel, the alloy bushing with high hardness and strong wear resistance is used in the contact part with the materials, such as Cr26, etc. If the raw material is Corrosive materials(such PTFE modification and so on), the basal body /matrix of barrel must be with SUS304, and the lining sleeve must be Ha C alloy or some corrosion resistant nickel base alloy sleeve.
Components of Co-rotating Twin Screw Extruder
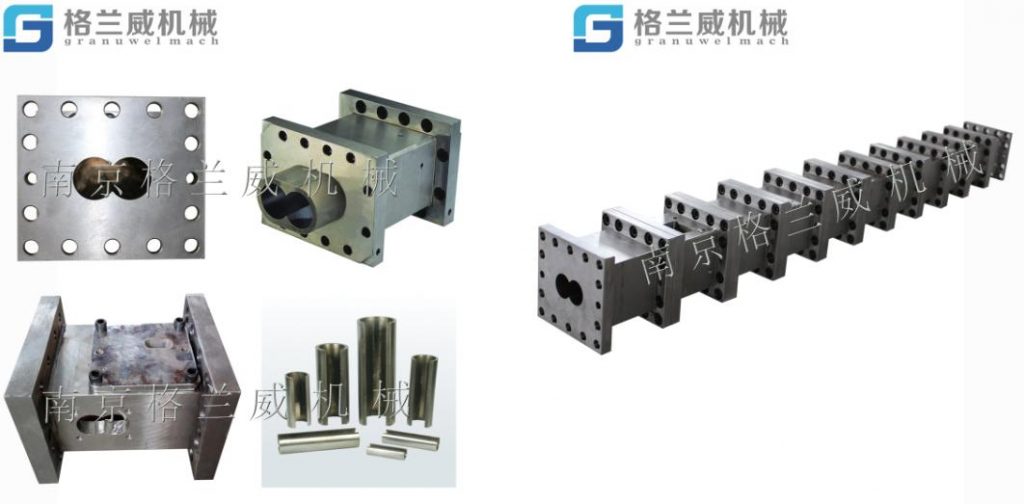
- The barrel section(s)- The barrel section is where the material and liquid are combined. Here the co-rotating twin screw extruder works in the mixing process in which they mix the material and liquid at different viscosity and different ratio mixing to meet the mixing requirements.

2. Gear Box- Gear box is the key component of the Co-rotating twin-screw extruders. The role of the gear box is to convert the kinetic energy provided by the motor. Through the deceleration of the gear box, evenly distribute to the two output shafts that rotate in the same direction and have the same rotational speed. The more reasonable the structure of the distribution box, the greater the bearing torque. It can be adapted to a larger motor power, and the output of the extruder is relatively higher.
3. The screws- The twin screws are perhaps one of the most important components in co-rotating twin screw extruders as they are what carry material through the process effectively.
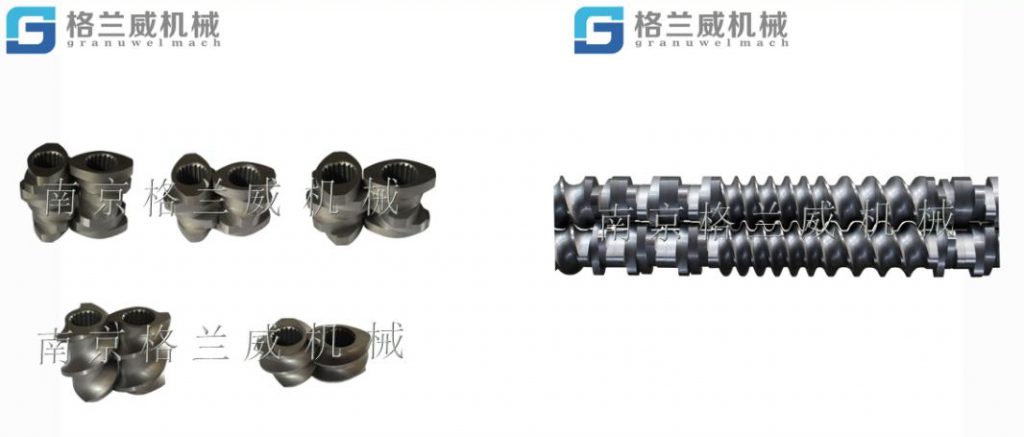
4. Screw Shaft- The screw shaft is the core component of the twin screw. According to its different functions are divided into: conveying screw shaft and mixing screw shaft.
The material of the screw shaft can also be selected according to the properties of the materials to be processed (wear resistance, corrosion resistance, etc.), different raw material systems, and different process engineering related to the different design of the screw shaft structure. The molten material to reach the mixing through the action of screw elements with different functions, reactions, etc. Unreasonable screw shaft structure will make the material over-plasticized or not completely plasticized.

5. Temperature Control System- Temperature Control System including heating system and cooling system. The heating system is wrapped on the outer wall of the barrel, and is generally divided into electric heating or far-infrared heaters. The cooling system is external to the equipment, and it mainly including with a water pump, Heat exchanger, water tank and pipelines. In general, the raw materials need to be quickly heating to molten status after entering into the extruder barrel, then the molten materials are conveyed through the screw shaft and extrusion after mixing. The mixing process may be an endothermic process. It may also be an exothermic process, at that time the cooling system will work. Its function is to tealize the controllability of the material processing temperature. Too high or too low processing temperature will affect the properties of the raw materials.

6. Die Head- Die Head is the extrusion part of the Co-rotating Twin Screw Extruder. The die head structure of different materials is not the same, for example: Hot-cutting die head will be needed for PE filling while strands die head will be used for PA+GF, ABS and other such high temperature plastics.
Common Uses for Co-rotating Twin Screw Extruder
There are many different kinds, shapes, sizes and uses for co-rotating twin screw extruders, including:
1. Pharmaceuticals- Where co-rotating twin screw extruders are used for production of pharmaceutical pellets with a wide range of applications ranging from the synthesis of proteins and peptides to drug delivery;
2. Oil and gas extraction- Co-rotating twin screw extruders are used for the production of oil, gas and other liquid hydrocarbon products such as benzene, gasoline, kerosene and even propane.
3. Nano chemistry- Co-rotating twin screw extruders are used in the production of nanoparticles by both organic and inorganic materials such as nanoporous plastics, nanostructured metals or materials with a high density that can be easily produced in a wide variety of shapes.
4. Food Packaging- Co-rotating twin screw extruders are used in the production of food packaging to create a variety of shapes and sizes that can hold a wide range of foods such as condensed milk, walnuts or even ice cream.
In Conclusion:
From the above, you can have a simple understanding for the co-rotating twin screw extruders, and you can be able to confirm what factors may affect their performance based on your production requirements so as to ensure optimal productivity. You’ll also be able to determine if you need one machine or multiple machines for your production line which can help save cost and time when scaling up during production.
For any further information, welcome to contact us—Nanjing Granuwel is here for serving you!