The process of color masterbatch is that one or more pigments experiences concentration, activation, ground and stabilization, and then is blended and granulated with resin.
Therefore, the color masterbatch should not only have good color and dispersion, but also ensure that the mechanical properties will not be damaged and it is better to improve its mechanical properties.
The cost of color masterbatch is affected by many factors, and the price gap is relatively large.
The prices of different color masterbatch products are also different because of their different manufacturing technology and cost. From the current market trend, the price of color masterbatch and functional masterbatch is generally higher than that of white masterbatch and black masterbatch.
The factors that affect the price are market factors and production cost. The different production raw materials and the development of the market are all affecting the price of the coloring masterbatch.
Table of Contents
ToggleThe traditional mode of production of color masterbatch
Most color masterbatches are mainly made of powdered pigments.
The pigments needed for a single color are fully mixed with powdered plastic raw materials through dispersion auxiliaries, such as wax, and then heated and melted in a twin-screw extruder, distributed mixing and dispersion mixing are carried out and evenly distributed in the plastic carrier.

Note: with the same formula, the dispersion effect of the laboratory twin-screw extruder is not necessarily consistent with the actual situation on the production line, so in production, the color value must be checked at the beginning and necessary corrections must be made. before it is produced on the production line.
Using single component to produce color masterbatch
The production of single color masterbatch is completed through two steps. The first step is to produce single component, and then producing color masterbatch.
Note: The dispersion of pigments in plastic materials at the highest allowable concentration is called an single component method.
At present, organic pigments with the highest concentration of 40-50% and inorganic pigments with the highest concentration of 75% can be dispersed into plastics by extrusion to obtain a good dispersion effect.
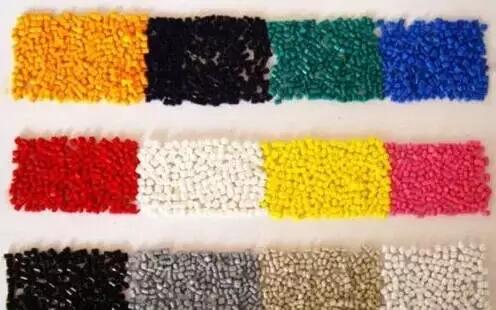
Pigment particles with good dispersion quality ensures that the pigment particles in the plastic are very fine and can obtain the best color penetration ability as possible. on the other hand, pigment caking of more than 5 microns is not allowed to avoid the formation of color spots.
In the laboratory, the color adjustment and sampling of single component and the production of masterbatch are done by single screw extruder.
Because the pigments have been dispersed, different single components only need to be melted and mixed in a single screw extruder.
Because the dispersion quality in the laboratory is the same as that in the actual production, the actual transferability of the color value of the raw materials obtained in the laboratory can be guaranteed in the actual production.
The cost factor of color masterbatch granulation
The production cost of color masterbatch includes equipment cost, energy consumption costs, labor costs, color change cleaning costs and waste costs, etc., which mainly depends on the granulator methods, equipment screw size, length-diameter ratio of screw and processing quantity.
Twin screw extruder granulation.
It is more expensive for organic pigments to be dispersed into plastics in a twin-screw extruder.
The length-diameter ratio of screw for parallel co-rotating twin-screw extruder is not less than 44. In order to ensure the addition of as many pigments as possible, the twin-screw structure has several mixing sections to mix the added pigments, but even so, the production yield of color masterbatch containing organic pigments in twin-screw granulation is relatively low.
Inorganic pigments have high density and are easier to disperse, so the output of twin-screw extruder is much higher.
Therefore, the dispersion cost per unit of inorganic pigments is lower than that of organic pigments.
The maximum pigment concentration is produced in large quantities by large machines, which can minimize the dispersion cost of single component per unit pigment.

Because the single screw extruder does not have to be dispersed, it may only need melting and mixing, so it is much simpler in structure than the twin screw extruder.
Not only are people more willing to buy, but it also has the following advantages: easy to clean, low production loss, easy to operate, clean granular materials, dust-free, and fast mixing.
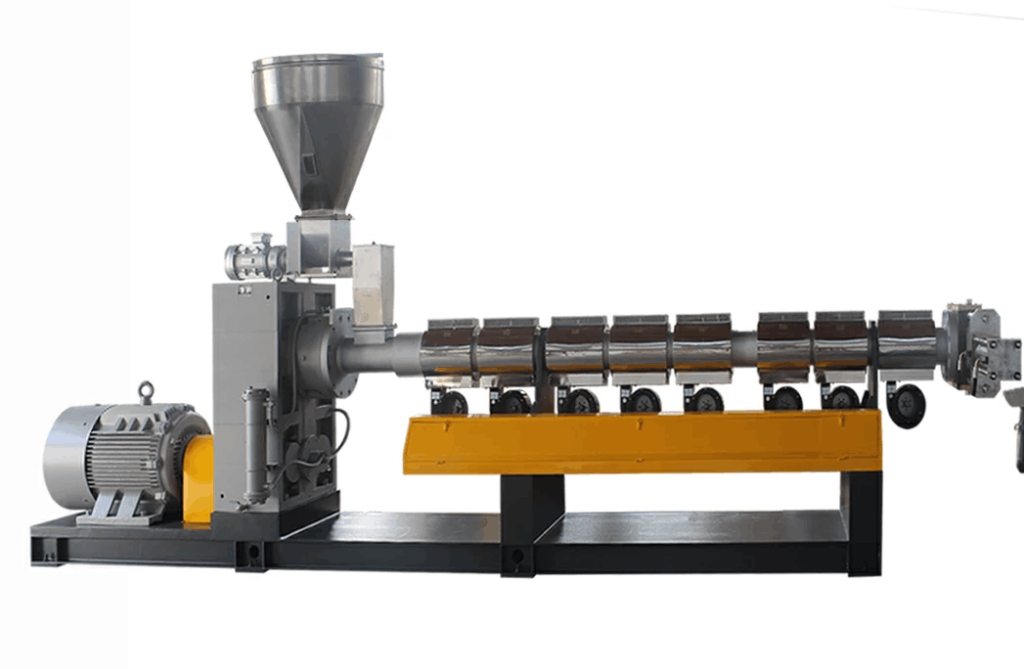
Select extruder type according to order quantity.
Small order (< 1t).
When processing small batches of color masterbatch from 25 to 1000 kilograms, smaller machines are generally used, and extruders with smaller screw diameters (such as 35,52mm screw diameter) have the most obvious advantages in processing batches up to 500kg. Because the color can be changed very quickly, the color masterbatch manufacturer can save workers and material costs.

Larger order (> 3t).
If the production of color masterbatch is more than 3 tons, the production cost of single-screw extruder and twin-screw extruder is the same, at this time, the most economical way must be determined according to the formula.
If the mixture of inorganic pigments (e.g. TiO2) and organic pigments is to be dispersed in a twin-screw extruder, the organic pigment can be added as a single component, so as long as the inorganic pigments are distributed).
Because organic pigments no longer need to be dispersed, inorganic pigments can be dispersed faster, so that the extrusion speed of equipment increases, the output increases and the cost is reduced.
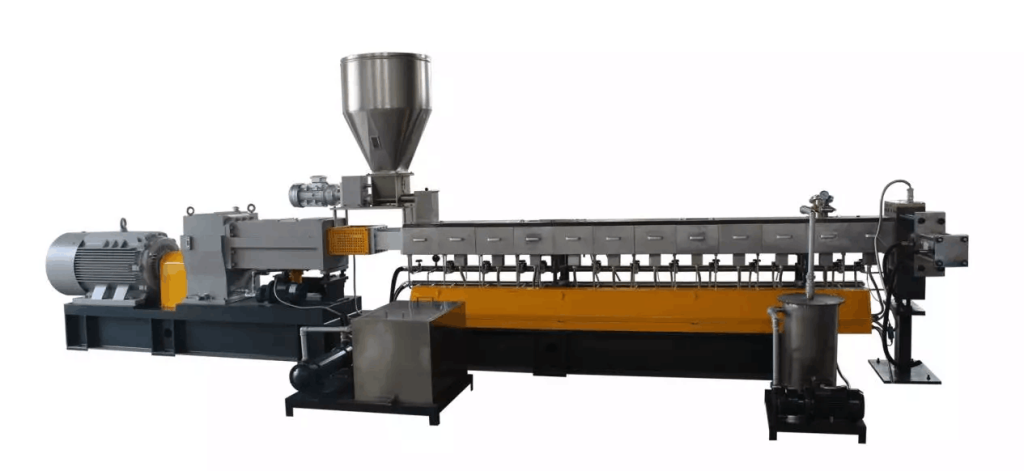
About us
Nanjing Granuwel Machinery CO., LTD is specializing in R&D design and manufacture of high polymer extruders, our team of top-level extrusion professionals provides the right extruder for your exact application.

We possess excellent capability of innovation and product development, and desire to provide best products for our customers through the improvement of equipment structure and reduction of equipment energy consumption through our practical experiences and technical innovation.
For any question/inquiry,warmly welcome to contact us!!!
Tel: +86-25-86199956
Mobile: +86-13813371123