When using a masterbatch machine to produce masterbatches, we often meet some problems so can’t get the qualified masterbatch. For example, uneven dispersion in black masterbatch is one of the usual problems during the production process.
This article introduces 2 usual problems met when using a masterbatch machine.
Table of Contents
Toggle1.Uneven Dispersion Of Carbon Black Phenomenon
whether you have the below confusion or not? During the manufacturing process of the black masterbatch, which contains 40% carbon black and utilizes EVA wax as a dispersant, inconsistencies in the dispersion of carbon black can be observed. This inconsistency manifests as some strips being very brittle while others are unbreakable. The production involves the use of a twin screw extruder, where the mixture undergoes high mixer pre-mixing before being added to the hopper. The temperature ranges from 160°C to 180°C, with the head temperature set at 175°C.
Uneven Dispersion Problem for Masterbatch Making Machine
Frequent breakage of the strips
The material in the hopper fails to descend smoothly, resulting in frequent breakage of the strips. Initially, it was suspected that there was a lack of material, but upon feeding, it was discovered that there was an abundance of material in the hopper, requiring manual pushing. Interestingly, this issue does not arise when the carbon black content is 20% or 30%.
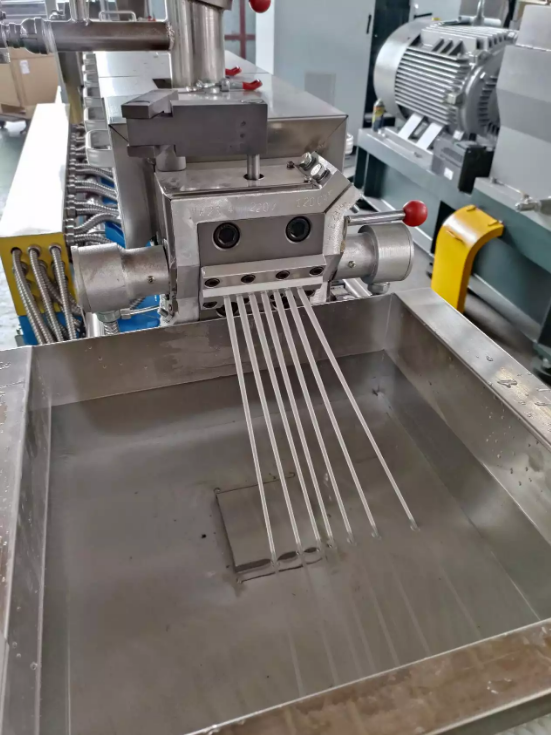
Inconsistency in the speed of the die head
Moreover, when there is material present, the strips continue to break, and there is a noticeable inconsistency in the speed of the discharge ports. Specifically, the two middle ports operate at a faster rate compared to the other two ports, resulting in an uneven discharge.
The uneven discharge speed of the machine head is precisely caused by the uneven dispersion of the material.Poorly dispersed materials have poor mobility, and evenly dispersed materials have good mobility. The material with poor fluidity is forced to stick to the inner wall of the flow channel. The discharge of the two ends of the guide is slow, and the discharge of the middle strip is fast.
Unfortunately, there is no on-site detection method available, and the masterbatch is directly used for production. Consequently, there is a lack of understanding regarding how to easily assess the quality of the masterbatch.
Solution
To address the issues encountered, several potential solutions can be implemented.
Increasing the amount of EVA wax
First, increasing the amount of EVA wax in the manufacturing process can aid in achieving better dispersion of carbon black, resulting in improved strip quality.
Reducing the temperature by 10℃
Additionally, reducing the temperature by 10℃ can help optimize the processing conditions and enhance the overall performance of the masterbatch.
Adjust the rotational speed of twin screw extruder
Another approach is to adjust the rotational speed of the twin screw extruder. This can be done by either reducing or increasing the speed to find the optimal setting that promotes more consistent and uniform strip formation.
Using the Special mixing screw elements to improve dispersion ability
Because carbon black has a complex and fine structure, it is composed of many layers of graphite molecules, and there are tiny gaps and corners between each layer of graphite molecules and other layers. Its structure is a multi-shell structure, which is formed by the accumulation of many layers of graphite molecules. The molecules of each layer are thick and thin, and can form a complex layered structure. Therefore, the most ideal state in the dispersion of carbon black is not to destroy its tiny gaps and corners, but the shear block usually used is too strong, which will destroy the corners of carbon black molecules and cause carbon black to agglomerate, so a special screw thread is used Originals such as S originals and hexagonal prism originals improve the distribution and mixing ability of carbon black.
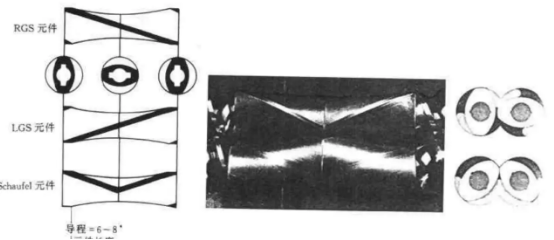
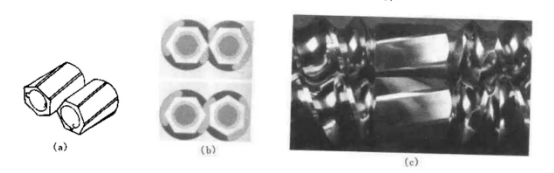
2. Bridge Formation Phenomenon
The hopper serves as a storage unit for plastic raw materials, and some hoppers are equipped with heating and blowing mechanisms to create a drying hopper. Typically, the hopper has a conical shape at the bottom and a cylindrical shape at the top. The optimal slope of the conical section varies depending on factors such as particle size, particle shape, friction coefficients between particles, and bonding coefficients. Bridge formation refers that failure to consider these factors that can result in a waste of hopper capacity or issues like “bridging” or a “funnel pipe” effect, leading to poor feeding or complete failure to unload the materials. The bridging phenomenon occurs when the diameter of the hopper narrows too rapidly near the extruder’s feed port. This rapid change in diameter causes the material to compact and solidify, obstructing the entry of raw materials into the extruder.
Bridge Formation Problem for using masterbatch machine
Plastic particles accumulate
When plastic particles accumulate and form an open bridge at the narrow opening of the hopper, providing support for the material above, the bridging phenomenon is more likely to occur. This is particularly common in recycled materials with larger particles and irregular shapes.
“Funnel into tubes” effect
The “funnel into tubes” effect can contribute to bridging. This happens when the downward flow of particles lacks sufficient force to pull their adjacent particles together. It is more prevalent when the plastic particle size is small.
Material being packed is extremely lightweight
The bridging phenomenon tends to be more problematic in cases where the material being packed is extremely lightweight or contains a high proportion of filler. To minimize or eliminate bridging, it is necessary to take certain measures. These include separating the mixed air from the powder before it enters the twin screw extruder, reducing the vertical distance between the feeding port and the screw as much as possible, and ensuring that the powder enters the bottom of the screw rather than directly adding it to the top. The screw structure should facilitate the movement of air along the screw groove and discharge it in the exhaust section, while preventing the gas from flowing back to the feeding port for discharge. Manufacturers often address the issue of bridging by adding 1-2% white oil to the mixture and vigorously mixing it for 2-3 minutes, provided the product allows for it. It is important to pay attention to the mixing time and method, as it is generally better to transform the powder into agglomerates. This approach effectively removes air from the filler, compacting it in some form and eliminating undesirable air. Once the filler becomes agglomerated, its bulk density increases, and the distance and direction of feeding in relation to the screw groove become less significant.
Solution
Installing a vibrating device or reducing the cone slop
The bridging phenomenon in hoppers can be addressed by installing a vibrating device or reducing the cone slope. High temperatures in the hopper can cause plastic pellets to soften and bond, leading to the formation of bridges or blockages. Difficulties in unloading can occur when adding calcium powder due to its poor flowability and the hindrance caused by external lubricants. To overcome this, it is recommended to mix heavy calcium with light calcium, consider adding a vibrator to the lower hopper, and increase the amount of internal lubricant. Vibrator installation is the most effective solution.
Temperature control
The temperature in the feeding area of the extruder, where material is transported by friction dragging, should be controlled between 120-160 °C. Low temperatures result in a shortage of material in the molten zone, while high temperatures cause premature melting and the formation of a lubricating ring-shaped molten film. The compression ratio of the solid bed in the feeding section is crucial for achieving the necessary density for melting. Particle materials are easier to compress due to their deformability, while powder materials lag behind in compression due to their sliding properties and low material density, leading to slower melting and exhaust processes.
Using special screw elements to improve the conveying capacity of materials.
Refer to the feeding of some lighter, easy-to-float raw materials (such as carbon black, nano-scale calcium carbonate, etc.), we usually use some large-lead thread elements, or customize some larger-lead thread elements, and use Special thread structure—reducing the angle of pushing material to a right angle (SK thread original)—to improve the material conveying capacity of the feeding port.
Improving the aspect ratio of the feeding section
The processing of thermoplastic elastomer particles, which have high internal friction and viscosity, often leads to material shortages, production yield fluctuations, and material degradation. This can be addressed by improving the aspect ratio of the feeding section, implementing forced cooling, and using vibration feeding. Some granulation raw materials contain elastomers, filler oils, fillers, resins, and other components, making material feeding challenging due to the presence of oil. It is generally not recommended to crush such materials into very small particles. Additionally, increasing the friction coefficient of the screw edge in the feeding section screw is necessary.
Proper pre-dispersion
When pigment is mixed with resin and undergoes pre-dispersion (“rubbing powder”), attention must be given to ensure proper dispersion. The dispersant and pre-dispersion process during pigment preparation significantly affect the post-processing dispersion. Failure to pre-disperse the toner can result in uneven mixing, causing different colors (“decors”) in various areas of the material. Blending manufacturers should be cautious if they observe color variations during production. Masterbatches, which are pre-dispersed with a carrier, theoretically should not experience poor dispersion. However, it is important to note that carriers of the same color can perform differently during processing. Significant differences in bulk MFR between the masterbatch and blended resin can cause color mixing. Additionally, if the natural color flexibility of the masterbatch leads to the formation of fine debris during the mixing process, it may result in different shades of color in the final product (“color mixing”).
About us
Nanjing Granuwel Machinery CO., LTD is specializing in R&D design and manufacture of high polymer extruders, our team of top-level extrusion professionals provides the right extruder for your exact application.

We possess excellent capability of innovation and product development, and desire to provide best products for our customers through the improvement of equipment structure and reduction of equipment energy consumption through our practical experiences and technical innovation.
For any question/inquiry,warmly welcome to contact us!!!
Tel: +86-25-86199956
Mobile: +86-13813371123