Inhoudsopgave
SchakelaarInvoering:
In de moderne productie wordt de toepassing van warmtegevoelige kunststoffen steeds wijdverbreider vanwege hun unieke fysieke en chemische eigenschappen, waardoor ze een ideale keuze zijn voor talloze industriële sectoren. De verwerking van warmtegevoelige kunststoffen brengt echter aanzienlijke uitdagingen met zich mee, omdat ze gemakkelijk afbreken en verkleuren bij hoge temperaturen. Deze kenmerken maken het moeilijk om aan de productievereisten te voldoen met behulp van traditionele verwerkingstechnologieën. De moleculaire structuur van warmtegevoelige kunststoffen kan gemakkelijk afbreken in omgevingen met hoge temperaturen, wat leidt tot verminderde materiaalprestaties, zoals verkleuring en verzwakte sterkte. Traditionele enkelschroefsextruders vertonen beperkingen bij het plastificeren van warmtegevoelige kunststoffen, met name in de afschuifkrachtlevering en temperatuurregeling. Dit resulteert vaak in ongelijkmatige plastificatie of overmatige afbraak van het materiaal, wat de productkwaliteit, consistentie en stijgende schrootpercentages en kosten beïnvloedt. Om deze uitdaging aan te pakken, bieden tweetrapsextruders een efficiënte oplossing. Deze twee onderdelen, bestaande uit een GTE-type hogesnelheids co-roterende dubbelschroefsmenger en een GDS-serie lagesnelheids enkelschroefsextruder, zijn verticaal orthogonaal gerangschikt en werken samen om efficiënte plastificatie en uniforme menging te bereiken, terwijl oververhittingsdegradatieproblemen worden vermeden. De volgende tekst gaat dieper in op de technische kenmerken, toepassingsvoorbeelden en geoptimaliseerde gebruiksstrategieën van dubbeltrapsextruders bij de verwerking van warmtegevoelige kunststoffen, waarbij hun innovatieve potentieel en brede toepassingsmogelijkheden in moderne verwerkingstechnologie volledig worden getoond, met name hoe door hun unieke dubbeltrapsontwerp en procesontleding, onafhankelijke controle en optimalisatie van elke verwerkingsstap worden bereikt, waardoor de productie-efficiëntie en het materiaalgebruik worden verbeterd.
Uitdagingen bij de verwerking van warmtegevoelige kunststoffen:
- Hittegevoelige kunststoffen zijn gevoelig voor chemische en fysieke veranderingen bij hoge temperaturen, wat aanzienlijke uitdagingen oplevert voor de verwerking ervan. Wanneer ze worden blootgesteld aan omgevingen met hoge temperaturen, begint hun moleculaire structuur te veranderen, wat leidt tot een ernstige vermindering van hun fysieke eigenschappen. Hoge temperaturen kunnen de breuk van polymeerketens versnellen, wat leidt tot een afname van het molecuulgewicht, wat op zijn beurt de mechanische sterkte en chemische stabiliteit van het materiaal beïnvloedt. Bij hittegevoelige kunststoffen zoals polyvinylchloride (PVC) en polyoxymethyleen (POM) treedt niet alleen verkleuring op, maar kunnen er ook schadelijke gassen vrijkomen, die niet alleen de kwaliteit van het eindproduct beïnvloeden, maar ook de productieomgeving potentieel vervuilen.
- Traditionele enkelschroefsextruders hebben duidelijke beperkingen bij het verwerken van deze materialen. Vanwege hun ontwerpbeperkingen kunnen enkelschroefsextruders niet voldoende schuifkracht leveren om een uniforme plastificatie van warmtegevoelige kunststoffen te garanderen. Bovendien gebruiken deze machines meestal elektrische verwarming met externe oppervlakteventilatiekoeling, waardoor de temperatuurregeling niet nauwkeurig genoeg is, wat gemakkelijk resulteert in oververhitte gebieden tijdens de verwerking, wat lokale of algehele degradatie van het materiaal veroorzaakt. Omdat warmtegevoelige kunststoffen bij lagere temperaturen en met nauwkeurige schuifsnelheden moeten worden verwerkt, vormen deze tekortkomingen van enkelschroefsextruders knelpunten bij het verbeteren van de productkwaliteit en productie-efficiëntie.
- Het gebruik van traditionele technologie om warmtegevoelige kunststoffen te verwerken leidt vaak tot inconsistente productkwaliteit en hogere schrootpercentages. Ongelijkmatige plastificatie en materiaaldegradatie kunnen instabiliteit veroorzaken in de prestaties van het eindproduct, waardoor de productiekosten stijgen en de concurrentiepositie van een bedrijf op de markt afneemt. Deze problemen benadrukken de noodzaak om geavanceerdere en nauwkeurigere verwerkingstechnologieën te zoeken. Om deze uitdagingen het hoofd te bieden, is de toepassing van tweetrapsmengunits een doorbraak geworden op het gebied van warmtegevoelige kunststofverwerking. De structurele kenmerken zijn onder meer: de eerste fase gebruikt een GTE-type hogesnelheids co-roterende tweeschroefmachine voor het mengen in een open vat met bijna nul druk, en de tweede fase is een GDE lagesnelheids enkelschroefextruder die het gemengde en gerijpte materiaal extrudeert bij lage snelheid en temperatuur, waardoor thermische degradatie wordt vermeden en mengeffecten nauwkeurig worden gecontroleerd en geoptimaliseerd. De tweetrapsmachine verbetert niet alleen de productkwaliteit, maar vermindert ook aanzienlijk de schrootpercentages, wat aanzienlijke economische en technische voordelen oplevert voor productiebedrijven.

Technische kenmerken van de Nanjing Granuwel Twin-Stage Extruder:
- De eerste fase is een GTE-type hogesnelheids co-roterende dubbelschroefsmenger, en de tweede fase is een GDS-serie lagesnelheids enkelschroefs extruder, beide verticaal orthogonaal gerangschikt om een dual-stage compound unit te vormen. Dit ontwerp combineert de voordelen van dubbelschroefs en enkelschroefs, waardoor efficiënte plastificatiemenging en schuifdispersie wordt bereikt, terwijl tegenstrijdigheden tussen hoge schuifoververhitting en hogedrukextrusie worden vermeden.
- De dubbele schroef zorgt voor transport, wat zorgt voor een gelijkmatige menging en plastificatie van het materiaal tijdens de verwerking. De unieke schroefstructuur bevordert betere mengeffecten, waardoor hittegevoelige kunststoffen gelijkmatig kunnen worden verwarmd en gemengd. De geometrische vorm en configuratie van de schroef zijn zorgvuldig berekend om de schuif- en distributie-effecten op het materiaal te maximaliseren, waardoor de vloeibaarheid van het materiaal en de verwerkingsefficiëntie worden verbeterd.
- De enkele schroef voert hogedruk-extrusie uit, maar gebruikt een lage snelheid, lage schuifmethode, waardoor tegenstrijdigheden door oververhitting worden vermeden. Dit ontwerp zorgt ervoor dat de tweetrapsextruder de productkwaliteit kan behouden en tegelijkertijd de productie-efficiëntie kan verbeteren en de productiekosten kan verlagen.
- De combinatie van twee- en enkele schroef breekt de procesfuncties af, waardoor onafhankelijke operationele variabelen toenemen, wat bevorderlijk is voor stapsgewijze optimalisatie van elk proces. Deze multifunctionaliteit garandeert niet alleen productkwaliteit, maar verbetert ook de productie-efficiëntie en verlaagt de productiekosten.
- De twin-stage extruder wordt veel gebruikt in verschillende warmtegevoelige materiaalsystemen en grote capaciteit devolatilisatiebewerkingen, zoals PVC, XLPE, halogeenvrije vlamvertragende kabelmaterialen, afschermingsmaterialen, koolstofzwarte materialen met een hoge concentratie en nabewerkingsbewerkingen na rubberdehydratie. Door het operationele proces te vereenvoudigen en het materiaalgebruik te verbeteren, biedt de twin-stage extruder een kosteneffectieve oplossing voor productiebedrijven, die volledig voldoet aan de behoeften van moderne productie.
De juiste granulatiemethoden kunnen ook het risico op oververhitting van warmtegevoelige materialen verminderen. Vanwege de neiging van PVC om water te absorberen, wordt echter over het algemeen luchtgekoeld heet snijden gebruikt; de meeste warmtegevoelige materialen moeten waterring- of onderwatergranulatormethoden gebruiken: Waterringpelletiseringssystemen en onderwaterpelletiseringssystemen werken goed met tweetrapsextruders bij de verwerking van warmtegevoelige kunststoffen. Door effectieve koelmechanismen zorgen ze voor de stabiliteit van gevoelige materialen tijdens de verwerking, waardoor problemen met materiaaldegradatie door hoge temperaturen worden verminderd.
Waterringpelletiseringssysteem:
Op het punt waar de plastic strip wordt gesneden, wordt water gespoten om een cirkelvormige waterband te vormen. Deze waterband omringt niet alleen de vers gesneden plastic strip, maar koelt het materiaal ook snel af door het snelle koeleffect van water. Dit snelle koelproces is cruciaal voor warmtegevoelige kunststoffen, omdat het voorkomt dat het materiaal te lang aan hoge temperaturen wordt blootgesteld, waardoor de fysieke en chemische eigenschappen van het materiaal worden beschermd tegen aantasting. Een bijkomend voordeel van waterringgranulatie is de relatief eenvoudige bediening, lage onderhoudskosten en het vermogen om plastic strips van verschillende groottes en vormen te verwerken, wat een economische en effectieve oplossing biedt.
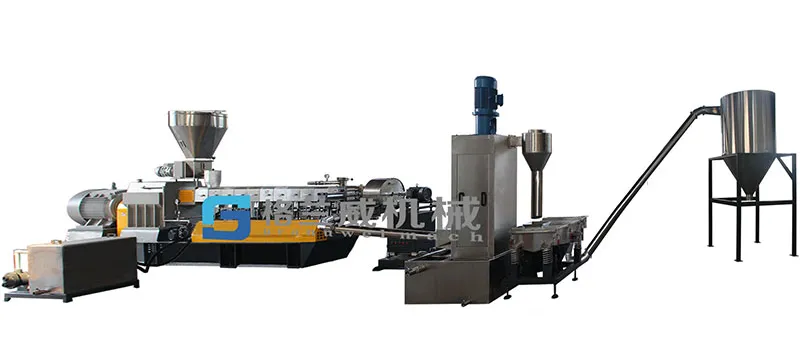
Onderwaterpelletiseringssysteem:
Het snijproces van de kunststof strip wordt volledig onder water uitgevoerd. Wanneer de kunststof strip wordt gesneden, valt deze direct in het water. Het water fungeert niet alleen als koelmedium, maar transporteert de gesneden deeltjes ook naar de volgende verwerkingsstap. Het grootste voordeel van deze methode is de extreem snelle verwijdering van gegenereerde warmte van gevoelige materialen, waardoor het risico op materiaalschade door oververhitting vrijwel volledig wordt geëlimineerd. Onderwatergranulatie zorgt voor het behoud van materiaaleigenschappen, met name geschikt voor warmtegevoelige kunststoffen die zeer gevoelig zijn voor temperatuur. Hoewel onderwaterpelletiseersystemen mogelijk complexere apparatuur en hogere initiële investeringen vereisen, zijn hun voordelen op de lange termijn bij het behouden van de productkwaliteit en het verminderen van schrootpercentages aanzienlijk.

Toepassingsvoorbeelden:
Op het gebied van de verwerking van warmtegevoelige kunststoffen wordt de toepassing van extruders met twee fasen steeds wijdverbreider, met de voordelen die met name duidelijk zijn bij de verwerking van materialen zoals polyvinylchloride en polyoxymethyleen. Bedrijven die zich bijvoorbeeld richten op de productie van PVC-kabelmaterialen, kampen met problemen van lage productie-efficiëntie en onstabiele productkwaliteit. Door de introductie van extruders met twee fasen verhogen bedrijven niet alleen de output van PVC-kabelmaterialen aanzienlijk, maar verminderen ze ook de problemen met materiaaldegradatie die worden veroorzaakt door te hoge temperaturen. De nauwkeurige temperatuurregeling en uniforme mengmogelijkheden van extruders met twee fasen zorgen voor de consistente kwaliteit van PVC-kabelmaterialen, terwijl de afvalpercentages worden verlaagd en de algehele productie-efficiëntie wordt verbeterd.
Casestudies tonen aan dat extruders met twee fasen niet alleen het verwerkingsproces optimaliseren en de output verhogen bij het verwerken van hittegevoelige kunststoffen zoals PVC en POM, maar ook zorgen voor consistente productkwaliteit door nauwkeurige procescontrole. Dit vertegenwoordigt een enorm technisch en economisch voordeel voor productiebedrijven die hoge kwaliteitsnormen nastreven.
Conclusie:
Met zijn onderzoek en toepassing op het gebied van warmtegevoelige kunststofverwerking is de twin-stage extruder van Granuwel een betrouwbaar stuk apparatuur geworden dat het productieproces en de productkwaliteit aanzienlijk verbetert. Door nauwkeurige controle van temperatuur en schuifsnelheid lost de twin-stage extruder veel uitdagingen op die traditionele enkelschroefsextruders tegenkomen bij de verwerking van warmtegevoelige kunststoffen, zoals materiaaldegradatie, ongelijkmatige menging en lage productie-efficiëntie. Deze technologische vooruitgang verbetert niet alleen de verwerkingsefficiëntie van warmtegevoelige kunststoffen, maar zorgt ook voor hoge normen in productkleur, sterkte en consistentie.
Productiebedrijven hebben aanzienlijke economische en concurrerende voordelen behaald door de invoering van de twin-stage extrudertechnologie. Kostenbesparingen worden weerspiegeld in minder materiaalverspilling, lager energieverbruik en lagere onderhoudskosten. Ondertussen kunnen bedrijven, dankzij de verbeterde productconsistentie en -kwaliteit, de concurrentiepositie van hun producten op de markt verbeteren, meer klanten aantrekken en hun marktaandeel vergroten. Deze directe en indirecte economische voordelen maken de twin-stage extruder een essentieel stuk apparatuur voor elk bedrijf dat zich inzet voor het verbeteren van productienormen en winstgevendheid.
Naarmate de zorg voor milieubescherming en duurzame productie blijft groeien, zullen toekomstige extruders met dubbele fase zich ook meer richten op het optimaliseren van energie-efficiëntie en materiaalgebruik. Bovendien zullen extruders met dubbele fase zich, met de ontwikkeling van opkomende markten en de diversificatie van industriële eisen, aanpassen aan een breder scala aan materialen en toepassingsgebieden, en zo een grotere bijdrage leveren aan innovatie en ontwikkeling in de wereldwijde productie.