Aby poprawić jakość swoich produktów końcowych, niektórzy producenci zainwestowali w kosztowne podwodne granulatory, tylko po to, aby odkryć, że zawartość wilgoci w granulatach pozostaje wysoka. Czy naprawdę nie ma różnicy między drogimi podwodnymi granulatorami a tymi tańszymi? W rzeczywistości jest to po prostu niedopatrzenie w procesie produkcyjnym.
W produkcji granulatu tworzyw sztucznych podstawowymi metodami peletyzacji są peletyzacja z chłodzeniem powietrzem/wodą, peletyzacja z pierścieniem wodnym i peletyzacja podwodna. W systemach peletyzacji, w których woda jest używana jako medium chłodzące, wybór metody peletyzacji bezpośrednio wpływa na wilgotność powierzchniową cząstek plastiku, co z kolei wpływa na jakość końcowych cząstek. Spośród tych metod kontrolowanie zawartości wody w peletyzacji podwodnej okazuje się stosunkowo trudne.
Jakie zatem czynniki wpływają na zawartość wody w produktach peletyzowanych pod wodą?
Wpływ ostrzy peletyzujących:
1. W trakcie pracy ostrza granulatora mogą się zużywać.
Po zużyciu mogą tworzyć zadziory na ciętych cząstkach, które mają tendencję do adsorbowania wody. Ta wchłonięta woda jest trudna do usunięcia podczas kolejnych procesów odwadniania, co skutkuje podwyższoną zawartością wody.
2. Wpływ sit filtracyjnych:
Długotrwałe stosowanie sit filtracyjnych może prowadzić do nadmiernego ciśnienia głowicy i ciśnienia zmiany sita. Po wyjściu z formy materiał doświadcza nagłego uwolnienia ciśnienia, powodując pęcznienie, które łatwo zatrzymuje parę wodną, tworząc puste przestrzenie. W rezultacie woda zatrzymana w materiale nie może zostać usunięta podczas późniejszego suszenia.
3. Niskie ciśnienie głowicy:
Niewystarczające ciśnienie głowicy zmniejsza gęstość materiału wytłaczanego z matrycy, co pozwala wodzie wnikać w cząsteczki podczas transportu. Ta przesiąkająca woda okazuje się trudna do uwolnienia podczas odwodnienia.
4. Nieodpowiedni dehydrator:
Moc suszarki jest zbyt niska, średnica wirnika jest zbyt mała — niekompatybilne suszarki mogą powodować niewystarczające odwadnianie i skrócenie odległości, jaką pokonują cząstki w procesie odwadniania, co utrudnia skuteczne usuwanie wilgoci.
5. Niska temperatura zbiornika na wodę:
Odwadnianie gorącą wodą jest bardziej wydajne niż odwadnianie zimną wodą. Nawet w peletyzacji pasma chłodzącego najskuteczniejsza metoda odwadniania polega na wdmuchiwaniu gorącego powietrza. Początkowo materiał granulowany często zachowuje wysoką zawartość wilgoci ze względu na konieczność obniżenia temperatury zbiornika wody, gdy woda wchodzi do układu cyrkulacyjnego, a następnie wzrasta jej temperatura, gdy materiał granulowany przenosi ciepło z granulatora.
6. Wysoka temperatura zbiornika na wodę:
Zbyt wysoka temperatura w zbiorniku z wodą może spowolnić chłodzenie cząstek, co prowadzi do wżerów na powierzchni i pęcznienia cząstek, zatrzymując wodę, która kurczy się podczas chłodzenia.
7. Mała ilość wody w zbiorniku na wodę:
Niewystarczająca ilość wody w zbiorniku może utrudniać cyrkulację wody, wydłużać czas wsiąkania cząstek i powodować infiltrację wody, co prowadzi do wysokiej zawartości wilgoci w cząsteczkach.
8. Niestabilne karmienie:
Nierównomierne podawanie może prowadzić do znacznych różnic w wielkości cząstek, a większe rozbieżności mogą skutkować wyższą zawartością wilgoci w większych cząstkach.
Zalety podwodnego systemu granulacji: wysoki stopień automatyzacji, piękny kształt produktu końcowego, szczególnie odpowiedni do produkcji średniej i dużej objętości. Nadaje się do modyfikowanej granulacji większości tworzyw sztucznych. Jednak w przypadku niektórych łatwo wchłanialnych materiałów nie zaleca się stosowania podwodnego systemu granulacji, poza tym tworzywa sztuczne o ultra wysokiej temperaturze w tworzywach sztucznych do zastosowań inżynieryjnych również nie są zalecane do stosowania takiego podwodnego systemu granulacji.
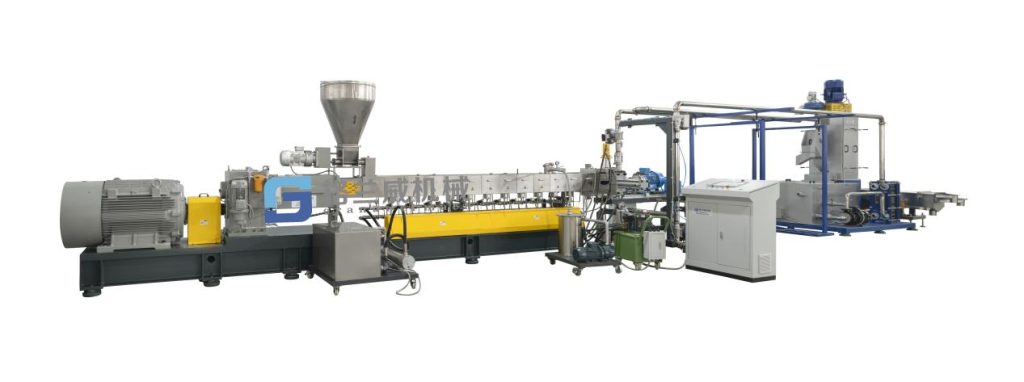