Table of Contents
TogglePreparations before operating plastic twin screw extruder
1. Check whether the place where the equipment needs to be oiled (or greased) has enough oil (grease).
2. Check whether there is leakage in the water, air pipelines and valves.
3. Check whether the oil level of the transmission box is between the maximum value and the minimum value of the oil level.
4. check whether the water level of the software water tank is at 2/3 of the water tank; check whether the water level of the vacuum air tank is at 1/3~2/3.
5. Test whether all valves, sensors and thermocouples are working normally.
6. Check the processing section for debris.
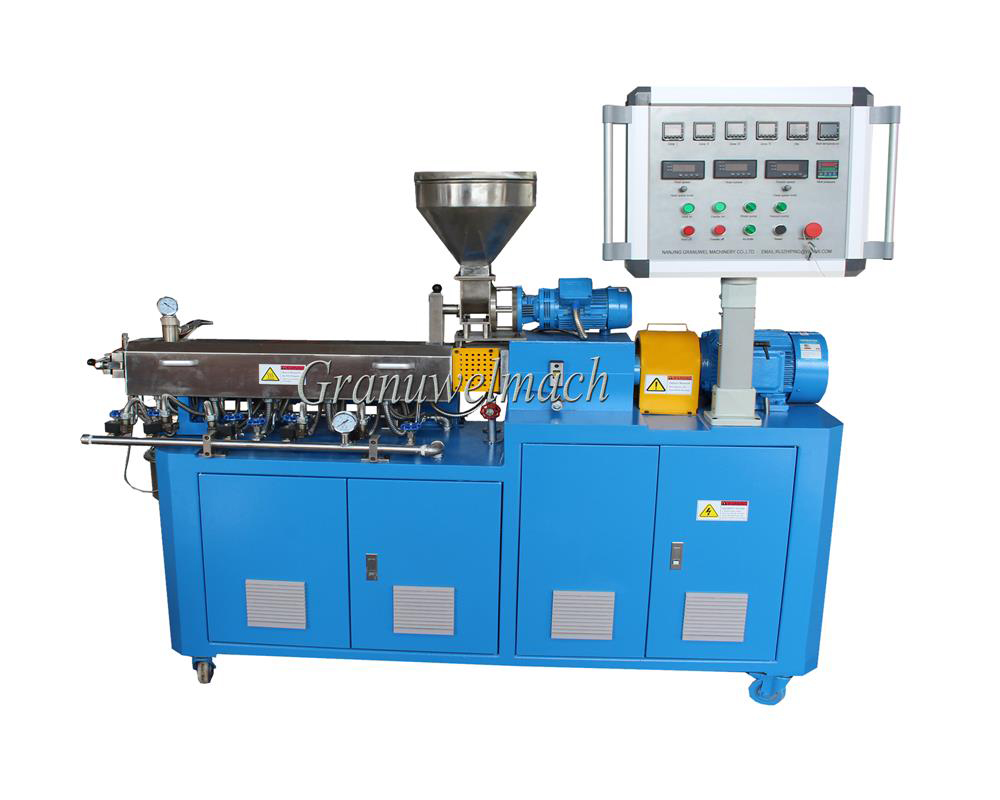
Start up
Starting sequence:
1. Heating: Electric heating equipment, set the temperature control meter to the set temperature of the material to be processed, and keep warm for at least half an hour after the temperature of all temperature control areas reaches the temperature (in winter or cold areas, the heat preservation time is at least 1 hour) before starting the plastic twin screw extruder.
Further, check whether the temperature control meter and solenoid valve are normal.
2. Open the oil lubrication system valve and turn on the oil cooler switch.
3. Turn the hand coupling at least three times to confirm the direction of the screw.
4. Turn on each auxiliary machine. Such as pelletizer, drier, cyclone fan, etc., and check the steering of auxiliary machines at the same time.
5. Start the main engine: When ensuring that the setting of the main engine is 0, press the oil pump on the analog board and the touch switch of the main engine in turn, and then slowly increase the speed of the main engine by rotating the setting knob of the main engine. The screw speed is generally around 50r/min when idling , the time does not exceed 2 minutes.
After the feeder starts, increase the screw speed of the host machine. For the two-stage machine, the single-screw should be opened first, and then the twin-screw can be opened.
6. Start the feeder: After the main machine of the plastic twin screw extruder is idling and there is no abnormality, press the feeding touch switch on the simulation board, and adjust the speed of the feeding screw according to the requirements of the inverter manual. In the process of feeding, the feeding amount should be gradually increased, and it should not change abruptly or exceed the bearing capacity of the screw of the main engine, that is, the current of the main engine should not exceed the rated value. If it is a multi-feeding system, the user should first adjust the main feeder to make it run well, and then start the other auxiliary feeders and side feeders in sequence.
7. After the equipment is running stably, turn on the water circulation system. Pay attention to observe the temperature changes in each section, use the manual adjustment valve to adjust the water intake of each section, and adjust repeatedly until the temperature control accuracy is within ±1-2°C of the set temperature control.
8. Finally, the vacuum pump can be turned on. First of all, close the valve between the vacuum system and the vacuum chamber, then open the water inlet valve of the vacuum pump, pay attention to observe the material at the exhaust port, if it has been completely plasticized and there is no material leakage, close the cover of the vacuum chamber, and turn on the vacuum pump , open the vacuum line valve to maintain a high vacuum.
Risk of burns from equipment heated surfaces and material! Be careful of being hurt by the gas discharged from the material! Wear a gas mask or face shield!
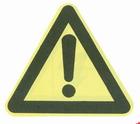
Risk of burns from equipment heated surfaces and material!
Be careful of being hurt by the gas discharged from the material!
Wear a gas mask or face shield!
Be careful of burns on the heating surface and materials of the equipment!
Be careful to be injured by poisonous gas discharged from the material!
Wear a gas mask or protective mask!
In-run inspection
1.Whether the current of the main motor is stable. If it fluctuates greatly or rises rapidly, the feeding amount should be temporarily reduced, and then gradually increase after the main current is stable. The screw should be adjustable smoothly within the specified speed range (100 ~ 500r/min).
2. Check whether there is any abnormal noise in the deceleration distribution box and the barrel of the main engine. If the abnormal noise occurs in the transmission box, it may be caused by bearing damage and poor lubrication. If the noise comes from the barrel, it may be due to foreign matter mixed in the material or excessive friction between the hard material and the barrel due to the low temperature setting, or the screw combination is unreasonable. If there is any abnormal phenomenon, it should be shut down immediately to eliminate it.
3. There should be no abnormal vibration, stagnation, etc. during the operation of the machine, and there should be no loosening of the fastening parts.
4. Pay close attention to whether the lubrication system is working normally, check the oil level and oil temperature, and the oil temperature should be within the range of 20-50°C depending on the season.
5. Check whether the temperature control, heating and cooling systems of plastic twin screw extruder are working normally.
6. Water cooling, oil lubricating pipelines are unimpeded, and there is no leakage.
7. Regularly check whether the extrusion of the head is stable and even, whether there is any phenomenon such as broken strands, blockage, poor plasticization or discoloration due to overheating, and whether the material pressure indication of the head is normal and stable. When the filter is installed, it can be determined whether the filter needs to be cleaned and replaced according to the measured value after driving. Head pressure should be less than 12.0MPa.
8. Check whether the vacuum degree of the exhaust chamber is close to the vacuum degree of the condensate tank used. If the former is significantly lower than the latter, it indicates that the filter plate of the condensate tank needs to be cleaned or the vacuum pipe is blocked.
Stop the machine
1. Close the vacuum system: close the valve of the pipeline from the vacuum tank to the pumping chamber, and open the vacuum chamber cover. Press the touch switch of the vacuum pump on the simulation board, and close the water inlet valve of the vacuum pump at the same time. It is forbidden to stop the vacuum pump first. Because if the valve is not closed, the water in the condensation tank may be poured into the barrel.
2. Stop the feeding system: Turn the feed setting potentiometer to the left to the end and press the feeding touch switch on the analog board once. If there is a multi-feeding system, liquid filling should be stopped first, followed by sider feeder and auxiliary feeder, and finally main feeder.
3. Stop the main engine: gradually reduce the speed of the main screw of plastic twin screw extruder, and try to drain the remaining materials in the cylinder (for heat-sensitive materials that are easy to decompose when heated, clean the main engine with polyolefin materials before stopping). After the machine head is out of the material, adjust the main screw speed to zero, and press the touch switch of the main machine in turn. For a two-stage machine, the twin-screw should be stopped first, and then the single-screw.
4. Stop the main motor fan, oil pump and water pump in order. Turn off all heat zones on the control panel.
5. Stop the auxiliary machine: stop the pelletizer and other downstream auxiliary machines. If it is a water-cooling strands pelletizing system, the blow dryer and pelletizer should be stopped, and the compressed air source of the pelletizer should be cut off at the same time.
6. Cut off the power supply of the heater and each motor, and then cut off the main power switch.
7. Close the cooling water inlet valves of the oil cooler and the soft water system cooler (note, do not close the manually adjusted cut-off valve of the cylinder cooling water pipe).
8. Clean the exhaust chamber, die head template, feeder and the whole unit.
9.In case of emergency and need to stop the main engine, you can quickly press the emergency stop button on the control cabinet, and then turn the main engine and the feeding speed control knob back to zero, close the vacuum valve and the water inlet valve, find out the cause of the failure. After the fault is eliminated, start the car again according to the normal procedure. When stopping suddenly, since the screw is full of materials, the machine head should be opened, and then the screw should be rotated slowly to remove the materials in the barrel.

Disassembly and assembly of the screw
The screw of this plastic twin screw extruder is designed based on integrated principle, and the combination can be replaced according to the needs of the operation. When disassembling the screw, the material in the main engine should be drained as much as possible (if the material is high-viscosity plastic such as PC or medium-viscosity plastic such as ABS and POM, PP or PE material can be added to clear the chamber before parking)and then stop the main engine and auxiliary machinery, each section of the electric heater can still work normally, and then replace the screw as the below steps.
1. Unload the pressure measuring and temperature measuring originals,unload the machine head parts, and clean up the material at the end of the head “∞” hole and the end of the head screw while it is hot.

2. Remove the screw cap (left-handed thread) and replace it with the screw removal tool (screw ring).
3. Loosen the locking cap of the spline sleeve near the screw.
4. Pull out the two screws synchronously and slowly, use a wire brush and a copper shovel to quickly clean the material on the surface of the screw while it is hot, apply an appropriate amount of paraffin wax on the surface of the screw, and wipe the surface of the screw with a cotton cloth, and it will also have a good effect. Until all the screws are cleaned, pull it out and lay it flat on a plank or two sleepers.
5. Remove the screw removal ring (left-handed thread) on the screw, and then disassemble the screw element while it is hot. Use a wooden hammer, copper rod or aluminum rod to tap lightly along the periphery of the screw element. Avoid hitting the thin wall of the end face of the threaded block . If material seeps into the surface of the mandrel and makes disassembly difficult, it can be heated. After the material in the gap softens, it can generally be disassembled while it is hot.
6. The end face, inner hole and keyway of the removed screw components should be cleaned up in time, and placed neatly on the shelf, and collisions with each other are strictly prohibited. The screw components that are not in use should be coated with anti-rust grease, and the surface of the mandrel should also be thoroughly cleaned of residual materials Clean, if not assembled temporarily, the mandrel should be suspended vertically to prevent deformation, and coated with anti-rust grease.
7. The inner hole of the cylinder can be cleaned with a stick wrapped cloth.
8. The assembly configuration of the two screws must be exactly the same. When assembling, the inner hole of each component and the surface of the mandrel must be evenly coated with a layer of molybdenum disulfide high-temperature lubricating oil. When each screw component is set on the mandrel, it must be Clean the end face, and finally tighten the compression screw (ie the screw head).
9.Place the two screws side by side at the working position with a phase angle of 90°, and slowly insert them into the barrel. After the spline at the end of the screw corresponds to the position of the spline sleeve, push the two screws in at the same time, so that the end of the screw is closely attached to the end surface of the output shaft of the transmission box. Before installing the screw, apply a thin layer of grease evenly on the spline at the end.
10. After the screw is installed, it should be turned manually to make the screw rotate for more than two weeks. After confirming that there is no abnormal phenomenon such as interference and scraping, the screen changer and head assembly can be installed. When installing, apply high temperature resistant grease evenly on the surface of each screw thread.
11. After the cylinder and machine head are heated to the set temperature and stabilized, the machine can be started according to the normal procedure.
Maintenance
1.No sundries are allowed in the material, and hard objects such as metal and sand are strictly prohibited from being mixed into the screw and barrel of the main host.
2. When opening the pumping chamber or barrel cover, be careful to prevent foreign objects from falling into the main machine barrel and screw.
3. The screw is only allowed to start at a low speed when idling, and the time does not exceed two minutes, and the screw speed can be gradually increased until after feeding.
4. Frequently check the lubricating parts and oil level, and replace all lubricating oil with new lubricating oil after running for 500 hours. Thereafter, the lubricating oil should be replaced after every 4000 hours of operation, and the time should not exceed 1 year, and the oil filter should be cleaned frequently.
5. Check the wear of the barrel and screw frequently.
6. Regularly check the wear of the sealing ring at the end of the screw.
7. Regularly check the operation of the gearbox and the oil seal.
8. When parking for a long time, anti-rust and anti-pollution measures should be taken for the machine, and the machine should be re-checked according to the installation and debugging procedures when it is restarted.
About us
Nanjing Granuwel Machinery CO., LTD is specializing in R&D design and manufacture of high polymer extruders, our team of top-level extrusion professionals provides the right extruder for your exact application.
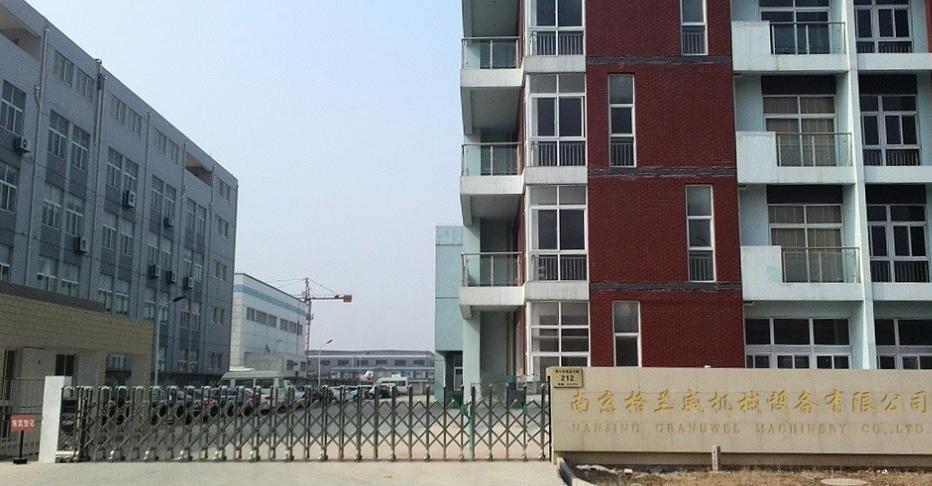
We possess excellent capability of innovation and product development, and desire to provide best products for our customers through the improvement of equipment structure and reduction of equipment energy consumption through our practical experiences and technical innovation.
For any question/inquiry,warmly welcome to contact us!!!
Tel: +86-25-86199956
Mobile: +86-13813371123
Web:https://toolant.net