Índice
AlternarIntrodução
As global awareness of environmental protection deepens, biodegradable materials have gained widespread attention as an effective way to reduce environmental burdens. These materials can decompose under natural conditions, reducing the reliance on traditional plastics and thereby helping to alleviate the pressure on landfills and reduce plastic pollution. Although biodegradable materials can fully decompose under suitable natural conditions, considering their long degradation time and cycle, along with the high cost of bio-based plastics, there is a promising market outlook for the recycling of biodegradable materials. In the recycling chain of biodegradable materials, twin-screw extruders play a key role by efficiently processing various biodegradable materials such as polylactic acid (PLA) and starch-based plastics through precise control of temperature and shear rate, achieving effective processing and modification. Twin-screw extruders are not only suitable for processing new materials but also show great potential in improving the quality of recycled materials and expanding the scope of reuse.
This article aims to analyze the application of twin-screw extruders in the processing and reuse of recycled biodegradable materials, discuss their technical advantages and challenges, and propose possible optimization strategies. The article will also discuss the environmental impact and economic feasibility of processing biodegradable materials using twin-screw extruders.
Main Sources
The sources of recycled biodegradable materials are extensive, covering multiple industries and consumer sectors. Agricultural waste is one important source, with global production exceeding 1 billion tons annually. This waste includes straw, bran, and animal and plant residues, which can be converted into biodegradable plastics through mechanical or chemical methods.
Food packaging is another key source, especially with the growing demand for eco-friendly packaging in supermarkets and the food service industry. According to data from Plastics Europe, the consumption of biodegradable plastics for food packaging in Europe was approximately 75,000 tons in 2019.
Common Types
The types of recycled biodegradable materials are diverse, mainly including polylactic acid, starch-based plastics, and biodegradable polyesters.
- Polylactic acid is a bioplastic made from renewable plant resources such as cornstarch and sugarcane through fermentation and polymerization processes. It has excellent transparency and processability, widely used in packaging, textiles, and medical fields.
- Starch-based plastics are made by mixing natural starch with degradable polymers like polyvinyl alcohol, with their biodegradability depending on the starch content, commonly used for producing shopping bags and trash bags.
- Biodegradable polyesters like polyhydroxyalkanoates have good mechanical properties and biocompatibility, suitable for manufacturing durable goods such as 3D printing filaments and medical equipment.
Diversity in Material Combinations and Mixtures
Due to the potential for recycled biodegradable materials to come from different production batches and usage environments, their combinations and mixtures exhibit significant diversity. This diversity is reflected in the physical form, chemical composition, and degradation rates of the materials. For example, variations in the molecular weight and crystallinity of PLA affect its mechanical properties and degradation behavior. Similarly, the type and content of starch in starch-based plastics can alter the final product’s performance.
In the production process of biodegradable materials, selecting appropriate pelletizing equipment is crucial for ensuring product quality and efficiency. Especially for materials like PLA and starch-based plastics, Nanjing Granuwel Machinery Equipment Company recommends using underwater pelletizing systems and water cooling strand pelletizing systems. These systems are specifically designed for processing temperature- and shear-sensitive biodegradable materials, ensuring that the materials maintain their biodegradability and mechanical properties during processing.
Underwater pelletizing systems are suitable for most polymer granulation, especially for large-volume granulation, microparticles, and soft material granulation, such as PLA, TPU, EPS, etc. They consist of a melt pump, filter, start-up valve, die head, underwater granulator, water circulation system, and dehydration system. By cutting molten plastic underwater, the system effectively controls the temperature of the granulation process and prevents material degradation due to high temperatures. This system is particularly suitable for processing thermally sensitive materials like PLA, ensuring that the cut particles have uniform size and good shape, facilitating subsequent processing and application.

Water cooling strand pelletizing systems mainly include a strand die head, cooling trough, blower, granulator, and vibrating screen. This system is simple in structure, easy to operate and maintain, and does not require high skill levels from operators, suitable for pelletizing most materials. Using water cooling to cool molten plastic before cutting can also effectively control the temperature during the granulation process, reducing the risk of material degradation due to exposure to high temperatures. The water cooling strand system is suitable for processing various biodegradable materials, including bio-based plastics, as it provides a milder cooling and cutting environment, protecting the biodegradability of the materials.
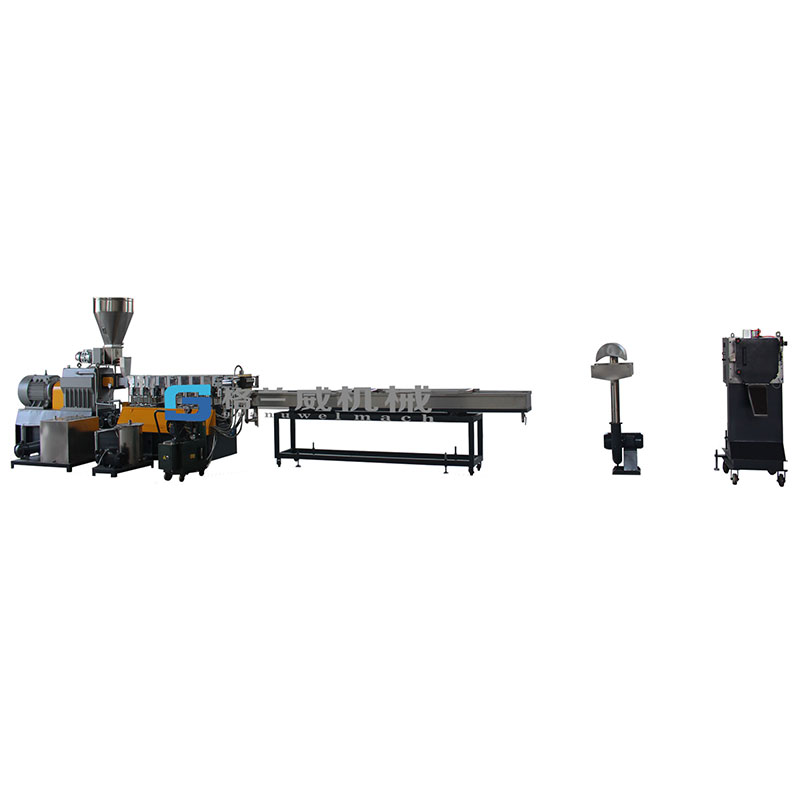
As a key equipment supplier for the production of biodegradable materials, Nanjing Granuwel Machinery Equipment Company provides underwater pelletizing systems and water cooling strand pelletizing systems that are not only technologically advanced but also highly efficient and reliable. These systems are specially designed for eco-friendly materials, ensuring that the production process not only follows the highest standards but also maintains the critical biodegradability of the materials. They are your ideal choice for eco-friendly material production.
Overall, underwater granulation and water cooling strand granulation systems provide ideal solutions for the efficient and high-quality production of biodegradable materials. These systems not only optimize the production process but also ensure that the final products meet environmental and functional performance requirements, making them indispensable technical equipment for producing biodegradable materials.
Technical Challenges of Granuwel Twin-Screw Extruders
1.Capability to Process Different Quality Recycled Materials
Due to the inconsistency in molecular weight distribution, moisture content, and additive content of recycled materials, our twin-screw extruder can adjust operating parameters such as temperature profile, screw speed, and shear rate to accommodate various material characteristics.
For recycled materials with higher moisture content, Granuwel twin-screw extruders are equipped with an effective drying system or pre-drying treatment. Additionally, Granuwel twin-screw extruders can add a vacuum venting section in the material melting zone, separating the moisture contained in the material through negative pressure vacuum to avoid melt fracture and bubble formation.
Impact of Impurities and Contaminants on Equipment and Product Quality
The inclusion of non-biodegradable materials may not only cause wear to the screw and die but also lead to uneven product performance. For example, the inclusion of metal fragments may damage the screw, while the inclusion of paper and other cellulose materials may affect the mechanical properties of the product. Furthermore, contaminants such as food residues and grease may cause the product to have an odor, discoloration, or microbial contamination. Therefore, Granuwel twin-screw extruders are equipped with effective filtration systems and detection equipment to ensure the purity of the material and the quality of the product.
2.Challenges to Processing Stability Due to Material Inconsistency
Due to batch-to-batch differences in recycled materials, such as variations in melting point, viscosity, and thermal stability, the extruder must operate under constantly changing conditions, which may lead to production interruptions and unstable product quality. To address this challenge, Granuwel twin-screw extruders possess high flexibility and precise control systems. The modular design of the twin-screw elements allows for adjustments to the screw combination at any time. For example, by real-time monitoring of processing temperature and pressure and timely adjusting the screw configuration and shear rate, the impact of material inconsistency can be mitigated to some extent.
Adjustment of Screw Design and Optimization of Processing Parameters
1.Adaptive Adjustment of Screw Design
Adaptive adjustment of screw design, including aspect ratio and screw element configuration, is key to improving the efficiency and quality of equipment processing recycled biodegradable materials. A larger aspect ratio provides a longer residence time and greater shear area, beneficial for the full mixing and reaction of materials but may also increase energy consumption and the risk of material degradation. For example, for recycled materials containing unstable components, a smaller aspect ratio may be chosen to reduce thermal decomposition.
Screw element configuration, including the arrangement and proportion of conveying elements, shear elements, and mixing elements, must also be adjusted according to the physical properties of the material. For example, for recycled materials with high moisture content, more shear elements can be used to promote the evaporation and drying of moisture.
Nanjing Granuwel Machinery Equipment is a professional manufacturer of twin-screw extruders, with many experienced design engineers and equipment commissioning engineers. For different material processing needs, the company has a comprehensive screw database and can quickly and accurately design suitable screw structures based on customer material characteristics. Granuwel Company can also provide customers with a trial platform, offering material testing before placing orders to help customers choose the correct and appropriate equipment.
Optimization of Processing Parameters
Precise adjustment of temperature control, shear rate, and residence time is crucial for ensuring material stability and uniformity during extrusion. Temperature settings need to be adjusted according to the material’s melting point and thermal stability to avoid overheating or insufficient plasticization. For example, the processing temperature of PLA is usually controlled between 170-20°C to maintain the stability of its molecular chains.
Control of shear rate significantly affects the mixing and plasticization effects of the material. Appropriate shear rate can promote uniform mixing of materials, but too high a shear rate may lead to material degradation. Adjustment of residence time relates to the processing time of the material in the extruder; too long residence time may lead to unnecessary energy consumption and material degradation, while insufficient residence time may result in incomplete plasticization of the material.
2.Application of Pretreatment and Post-Treatment Technologies
The application of pretreatment and post-treatment technologies is equally important for improving the efficiency and quality of twin-screw extruders in processing recycled biodegradable materials. These technologies include cleaning, drying, sorting, etc., aimed at enhancing material purity and consistency and reducing the impact of impurities and contaminants on the processing process.
Cleaning and sorting can reduce the inclusion of non-biodegradable materials and metal fragments and other impurities, thereby reducing equipment wear and product defects. Drying helps control the moisture content of the material, avoiding melt fracture and bubble formation. For example, by using infrared drying or hot air drying technology, the moisture content of PLA can be reduced to below 0.5%, thereby improving its stability and product quality during extrusion.
Environmental Impact and Economic Considerations
1.Environmental Benefits of Recycling Biodegradable Materials
The use of recycled biodegradable materials has significant environmental benefits in reducing environmental pollution and resource consumption. Taking polylactic acid as an example, as a bio-based plastic, its carbon dioxide emissions during production are about 50-80% lower than those of traditional petroleum-based plastics. Moreover, biodegradable materials can decompose under natural conditions after disposal, reducing reliance on landfills and the risk of soil pollution.
2.Role of Twin-Screw Extruders in Improving Recycled Material Quality
Twin-screw extruders play a key role in enhancing the quality of recycled biodegradable materials. Through precise temperature control, shear rate adjustment, and mixing efficiency, twin-screw extruders can improve the processing performance and final product performance of recycled materials. For example, by properly drying and plasticizing recycled PLA, its tensile strength can be increased by 20-30%, thereby expanding its application range in the high-end market.
3.Production Cost and Economic Benefit Analysis
Although the processing and application of recycled biodegradable materials may require higher initial investment, in the long run, their economic benefits are significant. Firstly, the use of recycled materials reduces dependence on raw resources, lowering raw material costs. Secondly, the high efficiency and versatility of twin-screw extruders make the production process more flexible and economical. For example, by adjusting screw configuration and processing parameters, the same equipment can process various types of recycled materials, reducing equipment investment and operational costs.
Furthermore, as consumer demand for eco-friendly products increases, products made from biodegradable materials often command higher market pricing. For example, the price of biodegradable plastic bags is usually 10-20% higher than that of traditional plastic bags, providing higher profit margins for manufacturers. At the same time, government support and subsidies for environmental projects also bring additional economic incentives for businesses.
Conclusão
Twin-screw extruders play a crucial role in processing recycled biodegradable materials. Through precise temperature control, shear rate adjustment, and mixing efficiency, these devices can effectively enhance the performance of recycled materials, making them more suitable for high-end applications. Future research and technological innovation will continue to focus on improving processing efficiency, adapting to new material characteristics, and reducing the environmental footprint during production. By increasing the added value of recycled materials, enterprises’ market competitiveness can be enhanced, promoting the development of sustainable business models.