Masterbatch is a key ingredient in producing plastic products. The process of preparing masterbatch is complex, with each step playing a crucial role in determining its color, functionality, and characteristics. In this article, Granuwel will walk you through the masterbatch manufacturing process and the equipment used for masterbatch manufacturing.
Índice
AlternarWhat Is Masterbatch?
What is color masterbatch? It is essentially a granular material made from a mixture of various base resins, fillers, additives, and a small amount of carrier resin. The concentration in the color masterbatch is usually high, and only a small proportion of the masterbatch needs to be added to the injection molding machine during the molding extrusion process (including extrusion and injection molding). This process is used in plastic manufacturing, making the operation easier, more environmentally friendly, and more convenient.
Base resin: Base resin refers to the type of resin used in the masterbatch, which is usually the same type of resin, or two completely miscible plastics, as the plastic substrate that is to be colored. For example, if the plastic substrate to be colored is polyethylene (PE), the base resin of the masterbatch should also be polyethylene.
Carrier resin: Carrier resin serves as the matrix of the masterbatch, with its primary function being to carry pigments and additives, ensuring they are evenly dispersed within plastic products. Choosing a suitable carrier resin directly affects the dispersibility, stability, weather resistance and other properties of the masterbatch.
Filler: Fillers are used to improve the physical properties of masterbatch, such as heat resistance, rigidity, hardness, dimensional stability, wear resistance and flame retardancy. Common fillers include calcium carbonate, wollastonite, kaolin, talc and barium sulfate.
Color masterbatch pigments: Pigments can be divided into organic and inorganic types. Commonly used organic pigments include phthalocyanine red, phthalocyanine blue, phthalocyanine green, etc., while inorganic pigments include cadmium red, cadmium yellow, titanium dioxide, carbon black, iron oxide red, iron oxide yellow, etc. These pigments play a crucial role in color masterbatches, providing the basic color foundation for the masterbatches.
Additives: Additives enhance the performance and processing characteristics of the masterbatch, including brightening, antibacterial, antistatic, and antioxidant properties, among others. These additives can improve the overall quality and application effect of masterbatch.
The main steps involve measuring, mixing, melting, extruding, and pelletizing.
The end product, called masterbatch, contains a ten times higher concentration of additives or fillers compared to that in the final plastic products.
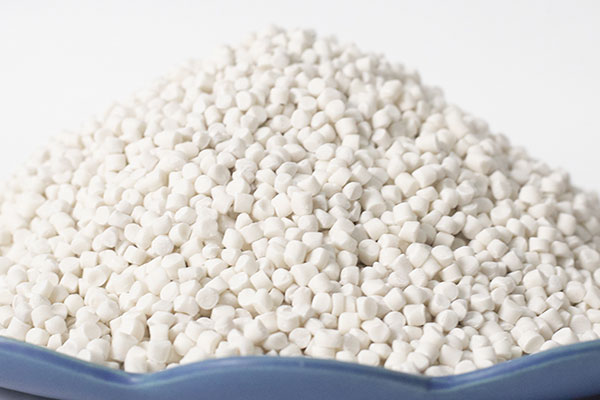

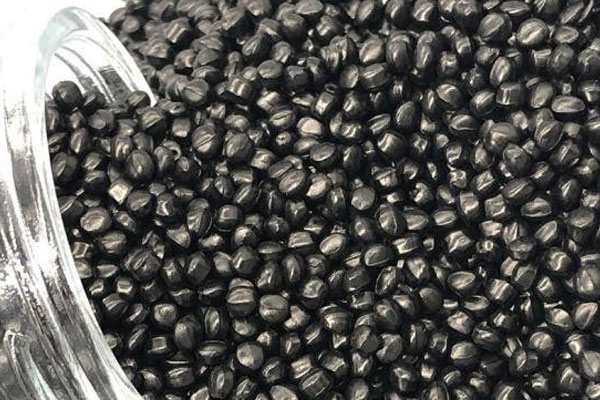

The Manufacturing Process of Masterbatch: How it’s Made?
The production process of masterbatch can be divided into several main stages, each of which has its key steps and operating points. The following is a detailed production process:
Raw material processing:
After the raw materials arrive at the manufacturer, the materials used for masterbatch are generally granular new materials, and the raw materials must be dry and clean. Only a few materials can be sheet-like because of their particularity. For example, PET chips.
Premixing:
Weigh the additives such as color powder, carrier resin, lubricant, dispersant, etc. according to the process requirements. The higher the accuracy, the better.
Put the weighed additives into the high mixer in order according to the process flow for preliminary mixing.
Melt extrusion:
The premixed materials are then fed into the extruder for melting and extrusion, a crucial stage in the formation of the masterbatch. Through high temperature and pressure, the mixture is melted and extruded into strips.
The extruded material needs to be cooled and pelletized to form uniform pellets.

Granulation:
The cooled material is then processed further in the granulator to produce the final masterbatch product.
During the granulation process, the temperature and time need to be strictly controlled to ensure the quality and stability of the pellets.
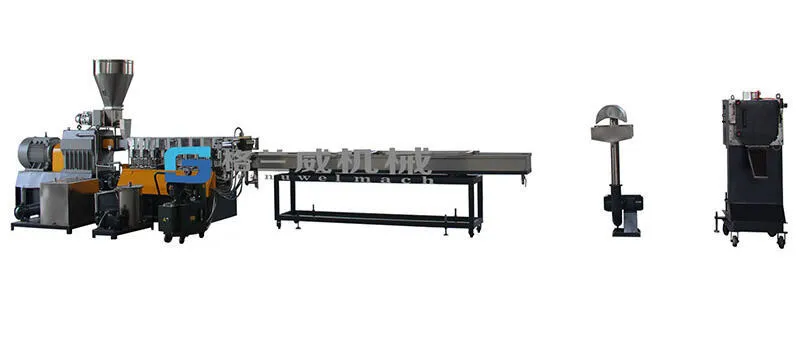
Screening and packaging:
Finally, the particles undergo screening to eliminate any unqualified ones, ensuring product quality.
The qualified particles after screening are packaged for easy storage and transportation.
Through the above steps, the production process of masterbatch is crucial from raw material processing to final packaging, and each step directly affects the quality and performance of the masterbatch.
Main Equipment Used In Masterbatch Manufacturing Process
The equipment used in the production of masterbatch is crucial for ensuring consistency and quality in the final product. Here’s a rundown of the key equipment involved:
Mixers/Blenders: These machines are essential for combining the base resin, pigments, and carrier resin to create a uniform mixture. They ensure that pigments and additives are evenly dispersed.
Extruders: Extruders are used to melt and process the mixed resin compounds. They transform the blended materials into a consistent, high-quality molten form ready for granulation. Based on various process requirements, extruders can be classified into single screw, co-rotating parallel twin screw, co-rotating parallel triple screw, and two-stage extruders. Single screw extruder is mainly used for the preparation of single function masterbatch, and suitable for the preparation of weak shear masterbatch, co-rotating parallel twin screw can be used for the preparation of most plastic masterbatch, it is simple to operate, easy to clean, can achieve a multi-purpose function of the machine. The three-screw is mainly used for the preparation of high-filled masterbatch, black and white masterbatch, its advantage is high yield, because the mixing effect of the three-screw is better, so it has unique advantages for difficult to disperse carbon black or titanium dioxide. The two-stage machine is mainly used for the preparation of PVC masterbatch.
Granulating Equipment: This equipment shapes the molten resin mixture into uniform granules or pellets. This step is vital for handling, storing, and further processing the masterbatch.
Quality Control Instruments: Various instruments, such as spectrophotometers, rheometers, and other testing devices, are indispensable for quality control during the manufacturing process. They help ensure that the masterbatch meets the required specifications and performance standards.
By carefully selecting the right ingredients and using the appropriate equipment, masterbatch manufacturers can produce products that meet the demands of different industries and applications. The complex interaction between ingredients and equipment is key to producing masterbatch with consistent quality and tailored performance.
The Vital Role Of Extruders In Masterbatch Production
Extruders play a vital role in masterbatch production, which is mainly reflected in the following aspects:
Raw material melting and mixing:
The extruder converts solid plastic into a uniform melt through heating and shearing, and fully mixes it in the process. This step is the key to ensure the uniformity of the color and quality of the masterbatch.
Efficiency and precision:
Twin-screw extruders are characterized by efficiency and precision, which can increase production capacity and ensure the uniformity and quality of masterbatch. Its advanced control system can achieve precise control of parameters such as temperature, pressure and rotation speed to ensure product quality.
Improving the compatibility of dyes and resins:
During the extrusion process, high temperature and shear force help improve the compatibility between dyes and plastics and improve the stability and uniformity of masterbatches.
Application of multiple process flows:
Masterbatch production processes include ink method, flushing method, kneading method and metal soap method, all of which require the use of different types of extruders, such as single-screw or twin-screw extruders.
Equipment design and optimization:
In order to meet the special needs of masterbatch production, the design of the extruder has also been optimized. For example, Granuwel GTE- 35B&D series extruders are designed for masterbatch applications, with good mixing performance and easy-to-clean operation mode.

Production efficiency and flexibility:
Twin-screw extruders are not only suitable for large-scale production, but also can quickly change formulations to meet the needs of small-scale samples and mass production. Its excellent performance and flexible process make it an ideal choice for masterbatch production.
Environmental impact and operational convenience:
Temperature control and equipment design during extrusion (such as quick-release blanking boxes) not only reduce the generation of organic waste gas and noise, but also improve the convenience of operation and the service life of the equipment.
In summary, extruders play a core role in masterbatch production. From raw material melting and mixing to the molding of the final product, every step is inseparable from the efficient operation and precise control of the extruder. Therefore, choosing a suitable extruder and optimizing its configuration are important factors to ensure the quality and production efficiency of masterbatch products.
Extrusion Machine Manufacturer & Factory – Granuwel
Granuwel, a professional extruder manufacturer and factory, provides high-quality lab extruders, twin screw extruders, single screw extruders, triple screw extruders and two-stage extruders. Feel free to contact us if you have any problems in masterbatch manufacturing process, we’re happy to be of help.