Índice
AlternarWhat is plastic pelletizer machine?
The working process of plastic pelletizer machine is that, first, adding plastic and other auxiliaries to the extruder, and then the materials are melted, mixed and extruded by the plastic granulator at a certain screw speed and temperature. The plastic particles are processed by a specific granulation method. Generally, the plastic pelletizer machine is composed of a plastic extrusion main machine, granulation auxiliary machine and hopper.
According to the production needs and technological process, the plastic extruder is divided into single-screw extruder, parallel co-rotating twin-screw extruder, triple-screw extruder and so on. Single screw extruder is mainly used for recovery granulation, sheet extrusion molding and other processes. co-rotating twin screw extruder is mainly used for all kinds of plastic blending, modification, filling granulation, or reactive extrusion.
The three screw extruder is mainly used for the preparation of plastic masterbatch such as plastic filling and black masterbatch. According to the cooling medium and cooling order, the granulator can be divided into water-cooled strip granulation, air-cooled strip granulation, water ring hot-cutting granulation, air-cooled hot-cutting granulation and underwater granulation. The following is a brief introduction to the relevant parts.

Components of single screw extruder
The single screw extruder is mainly composed of extrusion system, transmission system and heating and cooling system.
Extrusion system
The main function of the extrusion system is to melt and plasticize the polymer material to form a uniform melt and realize the transformation from the glass state to the viscous flow state. and in this process, a certain pressure is established and continuously extruded and transported to the die by the screw. Therefore, the extrusion system plays an important role in the forming quality and output of extrusion processing.
Transmission system
The transmission system is usually composed of motor, transmission box, coupling and so on. Its main function is to drive the screw and control torque needed in the extrusion process. In the process of extrusion, the screw speed is required to be stable and does not change with the screw load, so as to ensure the uniform quality of the products.
However, in different situations, the screw is required to achieve variable speed, so that an equipment can meet the requirements of extruding different materials or products of different shapes. In most extruders, the change of screw speed is realized by adjusting the speed of motor, and the transmission system is equipped with a good lubrication system.
Heating and cooling system
The heating and cooling system of the extruder consists of a heating device and a cooling device, which is a necessary condition for the extrusion process to proceed smoothly. The heating device and cooling device must ensure that the polymer material is melted and plasticized and the temperature conditions in the molding process meet the process requirements.
The cooling device is generally arranged in the barrel, screw and feed port of the extruder. Barrel cooling can be water-cooled or air-cooled, generally small and medium-sized extruders use air cooling, while large extruders mostly use water cooling or a combination of the two forms.
Screw cooling mainly adopts central water cooling, which aims to increase the solid conveying rate of materials, stabilize the output and improve the quality of products. The main purpose of the cooling device at the discharge port is to strengthen the transportation of solid materials, to prevent the stickiness of material particles due to heating, and to block the material mouth and then affect the feed. Generally speaking, for extruders with screw diameter above 90mm or high-speed extruders , a cooling device must be installed at the bottom of the hopper.

Components of twin screw extruder
The structure of twin-screw extruder is similar to that of single-screw extruder, which is also composed of extrusion system, transmission system and heating and cooling system. The structure of the gearbox in the twin-screw transmission system is much more complex than that of the single-screw gearbox, which uniformly distributes the torque input of the motor to two shafts with the same speed and rotation direction, so as to realize the work of the two screws.
The extrusion system of twin screw is composed of cylinder and screw, which are designed by modularization. Manufacturers can freely match the length of the cylinder and the structure of the screw according to different process projects in order to achieve a wider range of applications.
The Machine head is a key part of the plastic pelletizer machine. The nose of different materials may not be exactly the same. According to the granulation mode, it can be divided into cold cutting machine head, hot cutting machine head and underwater cutting machine head.
The principle of cold cutting machine head is to extrude the melt into strips through a flat runner. First cool (water-cooled and air-cooled) to dry, and then cut into pellets. The principle of the hot cutting machine head is to extrude the melt into strips through a circular runner. The rotating cutter cuts it into particles. And then by drying, cooling (water cooling or wind cooling).
The underwater granulation die is immersed in water. After the melt is extruded through the flow channel, the rotating cutter cuts the granule in water and takes it to the dehydrator to dry through the flowing water.

Energy conservation of extruder
Depending on the pressure and shear force produced by the rotation of the screw, the screw extruder can fully plasticize, evenly mix the material and form it through the die. Plastic extruders can basically be divided into twin-screw extruders, single-screw extruders and rare multi-screw extruders and non-screw extruders.
The energy saving parts of the extruder are that, one is the power part, the other is the heating part.
Power part
mostly use frequency converter, energy-saving method is to save the residual energy of the motor. For example, the actual power of the motor is 50Hz, in fact, only 30Hz is needed to meet the production needs, and the excess energy consumption is futile. If wasted, the frequency converter will change the power output of the motor. The motor achieves the effect of energy saving.
Heating part
Most heating parts use electromagnetic heaters, and its energy-saving rate is about 30% to 70% of the old resistance coil.
The plastic material is put in the extruder through the hopper and is transported forward through the rotation of the screw. In the process of the material moving forward, the material is heated by the barrel, and the material is melted after the shear and compression by the screw, thus realizing the transformation between the glassy state, the high elastic state and the viscous flow state.
In the case of increased pressure, the material in the viscous flow state passes through the mould with a certain shape and then becomes a continuum with a cross-section similar to the mould. Then it is cooled and shaped to form a glassy state, thus obtaining the parts to be machined.
Eight Points need to be paid attention in the production operation
- The correct operation of the waste plastic extruder can prolong the service life of the equipment, however, the use of the plastic extruder often does not get enough attention in our daily life, which will cause some unnecessary problems. So what problems should we pay attention to when using plastic machinery?
- Pay attention to fire safety. Fire extinguishers should be placed near the equipment that uses heat-conduction oil.
- When there is a failure or abnormal situation, it is necessary to report it to the relevant personnel, and professional maintenance personnel will be asked to deal with it. If you find that there are abnormal phenomena, remind to press the emergency stop switch immediately.
- Do not use low-quality recycled materials with metal impurities or sediment, and do not place metal objects that may fall near the feed port, so as to avoid aggravating the wear and tear of the screw and barrel or causing jam or damage. In order to prevent the metal that may be contained in materials, a strong magnet can be placed at the discharge outlet.
- The gearbox should be filled with lubricating oil that meets the requirements, and the new lubricating oil should be checked and replaced regularly in strict accordance with the equipment operating instructions.
- Plastic machinery should be operated in strict accordance with the requirements of the operating rules, and shall not be operated in violation of regulations in non-operating stations. To ensure the safety the reliability of the whole device, do not destroy the safety of the machine in pursuit of efficiency and protective measures.
- Operators need to be familiar with plastic pelletizer machine structure, performance and operation procedures.
- It is not allowed to turn on the screw once material temperature does not reach the set temperature and the holding time is not enough.
Sobre nós
A Nanjing Granuwel Machinery CO., LTD é especializada em P&D, design e fabricação de extrusoras de alto polímero. Nossa equipe de profissionais de extrusão de alto nível fornece a extrusora certa para sua aplicação exata.
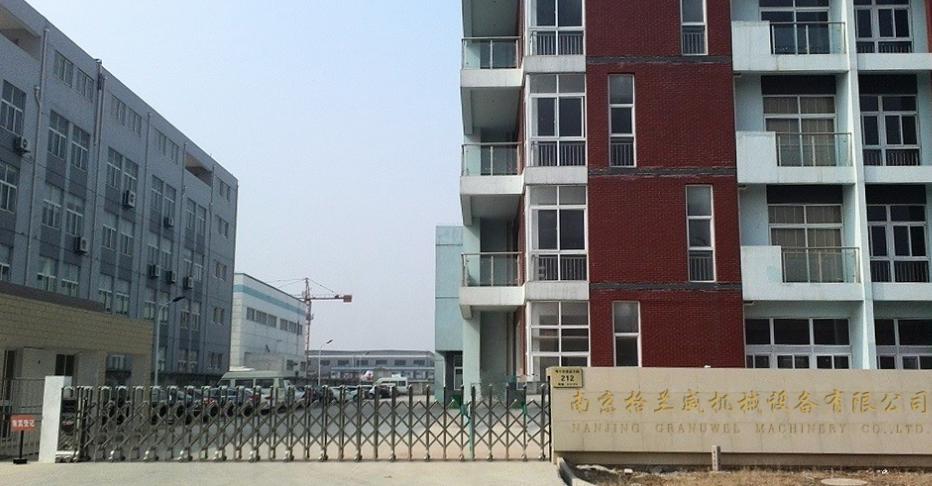
Possuímos excelente capacidade de inovação e desenvolvimento de produtos e desejamos fornecer os melhores produtos para nossos clientes por meio da melhoria da estrutura do equipamento e da redução do consumo de energia do equipamento por meio de nossas experiências práticas e inovação técnica.
Para qualquer dúvida ou consulta, sinta-se à vontade para entrar em contato conosco!!!
Telefone: +86-25-86199956
Celular: +86-13813371123
Rede: https://toolant.net