Índice
AlternarThe Introduction of Twin Screw Compounding Extruder
In the fast-paced world of plastic manufacturing, the demand for efficient and versatile equipment has led to remarkable innovations. One such technological marvel is the twin screw compounding extruder, revolutionizing the production of various plastic granules. Let’s delve into the intricacies of this advanced machinery and explore its applications, benefits, and the impact it has on the plastic industry.
The compounding extrusion process has been a cornerstone in plastic manufacturing, ensuring the uniform distribution of additives and materials.At the same time, the additives will change its original plastic properties, so that it has its own single plastic does not have properties.
For example,PP and GF glass fiber reinforced blending significantly increases the mechanical properties of the plastic (tensile properties increase from 20-30MPa of pure only PP to 65-90MPa, and bending strength increases from 25-50MPa to 75-120MPa , the flexural modulus increases from the original 800-1500MPa to 3000-4500MPa) Such excellent mechanical properties can replace engineering plastics ABS and ABS additive materials.
At the same time its heat resistance is better than ABS; some engineering plastics pass through coexistence with other materials compounding, it can be made into plastic alloy materials, which have better mechanical properties and lower costs, and can be used to replace metal alloys. Traditional extruders played a crucial role, but the emergence of twin screw compounding extruders has elevated the game.
Evolution of Twin Screw Compounding Extruder for Plastic Granules
To appreciate the significance of twin screw compounding extruders, a glance at the historical evolution of plastic granule production is essential. Traditional extruders, though effective in their time, had limitations that hindered efficiency and flexibility.
Advancements in Twin Screw Compounding Extruder Technology
Recent years have witnessed remarkable advancements in compounding extrusion technology. The introduction of twin screw extruders has addressed many shortcomings, offering improved performance, enhanced homogeneity, and increased versatility.
How Twin Screw Compounding Extruders Work
At the heart of these extruders is a unique twin screw mechanism. The synchronized rotation and intermeshing of the screws facilitate a thorough mixing of materials, ensuring a precise and controlled compounding process.
Benefits of Using Twin Screw Compounding Extruders
The adoption of twin screw compounding extruders comes with a myriad of benefits. From heightened efficiency and productivity to superior material homogeneity, industries are experiencing a transformative shift in their manufacturing processes.
Applications of Twin Screw Compounding Extruders
Industries involved in plastic production have eagerly embraced the technology. The versatility of twin screw extruders allows for the processing of various plastic types, opening doors to diverse applications in the manufacturing sector.
- PLA/PBAT/PHA/PBS etc. corn starch 100% biodegradable granules
From the implementation of China’s plastic restriction order in 2008 to the full opening of the global plastic restriction order in early June 2023, it requires a complete ban on traditional PP and PE plastics and the use of 100% degradable materials.
Twin screw compounding extruders are at the forefront of this sustainable revolution, offering specialized applications for a range of biodegradable materials. Their role in processing PLA, PBAT, PHA, PBS, and corn starch is instrumental in achieving desired material properties.
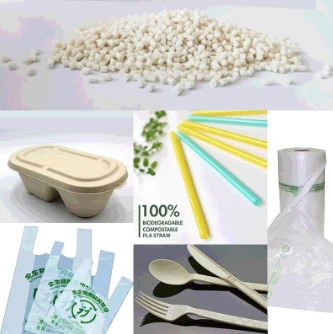
- Cable materials, low-smoke halogen-free cable materials, etc
Cable material manufacturing has undergone significant transformations, and twin screw compounding extruders have played a crucial role in enhancing efficiency. Their introduction has revolutionized the cable industry, ensuring not only increased productivity but also improved material homogeneity.
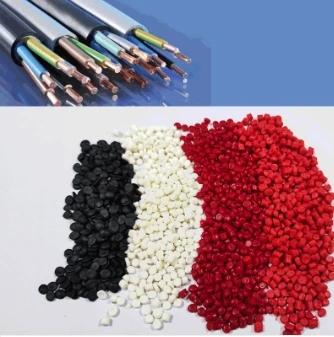
- Cable materials, low-smoke halogen-free cable materials, etc
The adoption of twin screw compounding extruders brings forth numerous advantages in elastomer processing. From increased productivity to ensuring material homogeneity, these extruders offer versatility in handling different elastomeric formulations, making them indispensable in the manufacturing landscape.

- Engineering plastics, such as ABS automotive interior materials, PA, PC, PBT, EVA, PE, PS, etc.
From increased productivity to ensuring material homogeneity, the extruders offer versatility in handling different engineering plastic formulations, making them indispensable in the manufacturing landscape.

- Various kinds of color masterbatch is providing the choosing for your fantastic life
The twin screw design offers several advantages in color masterbatch compounding. The dual screws provide better mixing and dispersion of colorants throughout the polymer melt. This results in a more uniform and consistent color distribution, leading to improved product quality. The extruder’s ability to control temperature and shear forces helps achieve precise color matching and enhances the dispersion of color particles.

- PET bottles recycling granules, providing the whole set of production plan
Twin screw compounding extruders are commonly employed in the recycling of PET (Polyethylene Terephthalate) bottles to produce high-quality recycled granules.
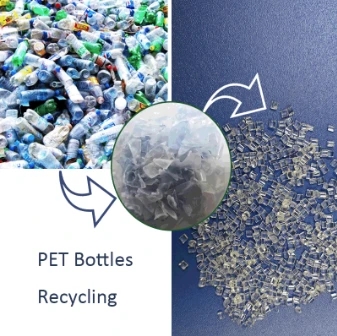
- PVA water soluble material for Laundry ball or hospital laundry bag with free formula
Twin screw compounding extruders find application in the production of PVA (Polyvinyl Alcohol) water-soluble material for items like laundry balls or hospital laundry bags.

- One-step extrusion of PLA + corn starch, PP + CaCO3 stone paper, PE + Mg(OH)2 flame retardant aluminum-plastic composite panels, PET sheets and other plastics
The combination of twin-screws and melt pumps can realize the direct extrusion of many special sheets. This equipment combination combines the excellent blending capabilities of the twin-screws with the pressure stabilizing and boosting capabilities of the melt pump to achieve to directly extrude the required sheets in one step.Its advantages are: low energy consumption, small floor space, and reduced material performance degradation caused by secondary melting of many materials.
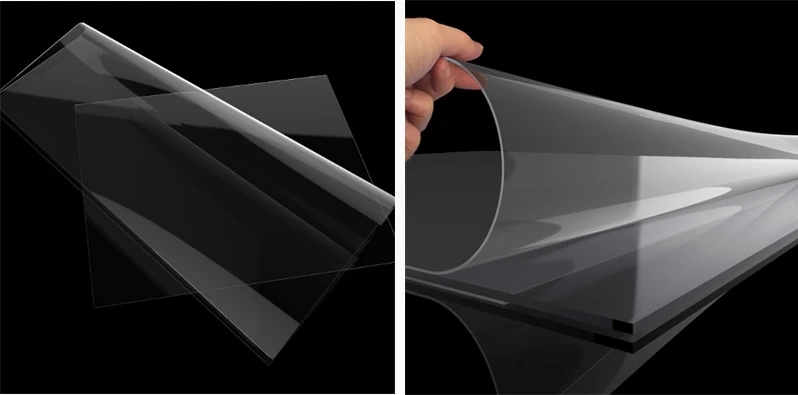
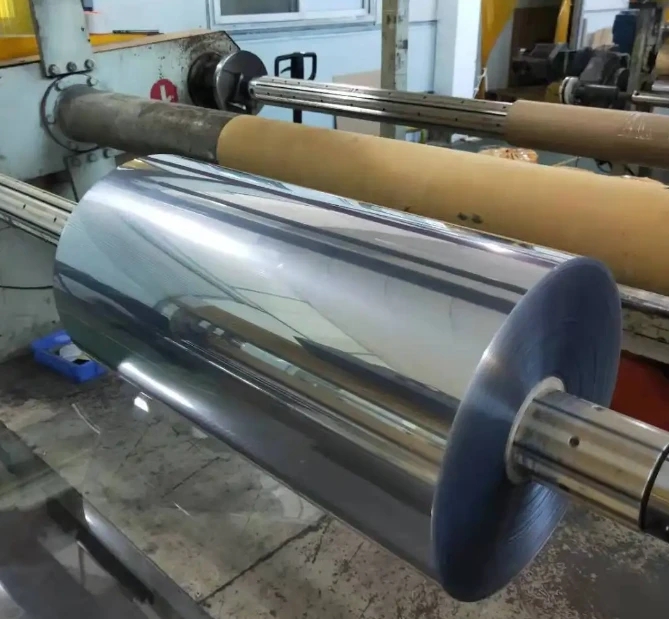

- Various kinds of recyling PPP,PE,ABS flakes or film etc.
Twin screw compounding extruders are widely utilized in the recycling and modification industry for processing various types of plastic materials, including PPP (Polypropylene), PE (Polyethylene), ABS (Acrylonitrile Butadiene Styrene), flakes, or films.
In the process of recycling granulation, additives can be added to modify the above plastics to improve their performance to achieve recycling. Thus slowing down the environmental pollution caused by plastics.

Comparative Analysis with Single Screw Extruders
A critical examination of twin screw extruders versus their single screw counterparts reveals distinct advantages. The twin screw’s ability to handle a wide range of materials and provide better mixing sets it apart in the competitive landscape.
Key Features to Look for in Twin Screw Compounding Extruders
For businesses considering the adoption of twin screw compounding extruders, understanding the key features is paramount. High torque and speed capabilities, modular design, and precise control systems contribute to optimal performance.
Considerations for Optimal Performance
While the technology promises groundbreaking results, proper maintenance and adherence to recommended cleaning procedures are crucial. Additionally, selecting the right screw configuration for specific materials ensures optimal performance.
Industry Trends and Future Outlook
A glimpse into current industry trends showcases the increasing integration of twin screw compounding extruders. The future looks promising, with anticipated developments that could further enhance the capabilities of this technology.
Conclusão
In conclusion, the twin screw compounding extruder stands as a game-changer in the plastic manufacturing landscape. Its ability to enhance efficiency, improve product quality, and contribute to sustainability makes it a must-have for forward-thinking industries.
