It is common knowledge that many different types of machinery are required for the processing and production of modified plastic products. Among these equipment are twin screw extruders, which are used to both create polymers and process them efficiently.
In order to achieve a radical improvement in both form and function, twin screw extruder manufacturers are continually pushing the development of technology. Users can also get high-quality twin screw extruders that meet their needs thanks to the equipment’s adaptability.
A screw extruder is a device that incorporates the physical steps of melt conveying, melting, solid conveying, exhaust, pressurization, and dehumidification within the screw itself. Twin-screw extruders are preferred over single screw extruders because they blend the melt more thoroughly. These days, twin-screw extruders are the workhorses of the polymer processing industry.
Innehållsförteckning
VäxlaTypes of Twin Screw Extruder
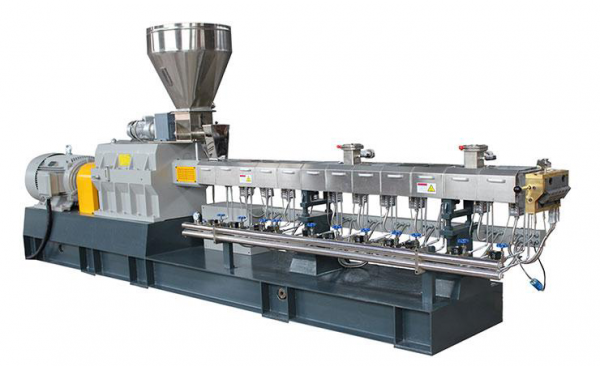
According to the direction of the twin screw rotation, the extruder can be classified as either the same direction or the opposite direction. A co-rotating extruder has screws that rotate in the same direction, while a non-rotating extruder has screws that rotate in opposite directions.
It is possible to classify extruders into two parallel categories, those with a parallel axis and those with an intersecting axis, depending on the orientation of the twin screw. There are two types of twin-screw extruders: those with parallel axes, and those with intersecting axes, commonly referred to as conical.
Parallel Twin Screw Extruder
Because the distance between the two screws is small, the screws have good self-cleaning properties, that is, during the forward conveying process of the materials, due to the close meshing of the two screws, the materials are continuously pushed forward without staying, so the materials will not accumulate in the screw and deteriorate due to high temperature, and always keep the screw clean.
Because the two screws are parallel, the length of the screw can theoretically be extended indefinitely. In fact, the length of the screw, or length-to-diameter ratio, has a very flexible range. Depending on the material processing technology, from the short 32:1 to the extra long 64:1 are available. In our practical application, the commonly used specifications of 40:1, 44:1, 48:1 can be adapted to the modification, filling and blending process of most materials.
It is possible to adopt the length-to-diameter ratio according to the needs of the plastics processing technology, making it larger or smaller depending on the molding conditions. Compared to conical twin-screw extruders, parallel twin screw extruders have much more parallel capabilities. Good mixing and plasticizing potential and degassing capability, as well as similar adaptability to materials and plastic product molding processes, are the characteristics of the conveying mechanism of the parallel twin-screw extruder that drives plastics forward.
Conical Twin Screw Extruder
Two conical screws are placed into a barrel at an included angle, with the screws themselves aligned horizontally. The two output shafts in the transmission gearbox have a greater centre distance because the centre distance of the two axes keeps rising from the small end to the large end.
There is plenty of room for larger radial and thrust bearings to be installed in these transmission systems because of the lack of gears and gear shafts. The conical twin screw extruder’s large working torque and huge load-bearing capacity are made
possible by the extruder’s drive shafts, each of which has a shaft diameter adequate to satisfy the transmission torque. This extruder with two screws that run in parallel is unparalleled.
What to look for when buying a twin screw extruder?
The price range
The cost of twin-screw extruders varies depending on the model, specs, and type of material being processed. Large price gaps exist between domestically produced twin-screw extruders and foreign mainframe models, which can cost tens of millions of dollars. Those looking to purchase twin screw extruders should do it in a manner consistent with their specific requirements and resources.
Accuracy
Design processing accuracy is a rigid index that is mostly dependent on the parallelism of the screw shaft, which in turn impacts the quality of the material’s processing. The distance between the screw edge and the inner wall of the barrel, as well as the distance between the meshing areas, are both determined by how parallel the screw shaft is.
As for the second, the carburization depth of the barrel’s inner wall and the screw surface is what ultimately decides the longevity of the service life. Last but not least, as long as the torque divider and gearbox are accurate, they can be ignored.
Processing Requirements
Confirming the configuration of the equipment according to the performance requirements of material, such as temperature zone, aspect ratio, opening and closing method, kneading block specifications, heating power, material wear resistance, as well as permutation, and the combination is the best way to select a twin screw extruder.
Choose the twin-screw extruder that can fulfil these specifications. In most cases, the intermeshing co-rotating twin-screw extruder is utilized for mixing, plasticizing, and pelletizing the raw materials.
Slutsats
Customers find twin screw extruders to be quite essential. Twin screw extruders come in a variety of forms, with varying characteristics and applications. As a result, it is important to understand the performance and application of various twin screw extruders.
The intermeshing co-rotating twin screw extruder is an example of a combined screw since it has a high speed and shear rate. It’s commonly utilized in the modification of polymers that aren’t readily decomposed by heat compounding, filling, or reactive extrusion materials. The intermeshing counter-rotating twin screw extruder is a good plasticizing machine because of its mixing function. Its greatest feature is that it can directly mould PVC powder. If the screw’s geometric structure is changed, it can also be used to process other materials.
To start, ascertain the extrusion volume based on the size of the plastic section. After that, select the specifications of the twin screw extruder by using the calculated extrusion volume. Essentially, if processing and molding conditions are equal, a conical twin-screw extruder can withstand greater pressure than its parallel counterpart.