In this blog post, as a professional manufacturer specializing in the R&D and production of industrial extruders, we, Granuwel, will walk you through compostable and biodegradable plastic extruders, how they work, and their practical significance for environmental protection.
Conventional plastic takes at least 200 years to fully decompose naturally, and in some cases, it could take as long as 500 to 1,000 years. Today, an incredible amount of plastic remains to be degraded, which has become a big threat to the environment. The degradable process of compostable and biodegradable plastics can be much shorter, like several months once the conditions are appropriate. There’s no doubt that turning conventional plastics into compostable and biodegradable plastics is an environmentally friendly and sustainable solution.
Then, here comes the question: How to Make Compostable & Biodegradable Plastics?
Innehållsförteckning
VäxlaHow to Make Compostable & Biodegradable Plastics?
Before we jump into the this topic, let’s quickly go over the difference between compostable and biodegradable plastics.
Difference Between Compostable And Biodegradable Plastics
Typically, all compostable plastics are biodegradable, while not all biodegradable plastics are compostable.

Compostable Plastic Bags

Biodegradable Plastic Tableware
Biodegradable plastics can be decomposed by microorganisms under natural conditions and eventually converted into natural substances such as carbon dioxide, water and organic fertilizers. However, compostable plastics require specific environmental conditions (such as sufficient oxygen, warm temperature and humidity) to completely decompose within a specified time and convert into non-toxic organic substances. In addition, compostable plastics do not leave harmful residues after decomposition, while biodegradable plastics may decompose into toxic residues such as microplastics in some cases. Therefore, compostable plastics are seen as a more environmentally friendly option because they do not harm the environment during the decomposition process.
The Production Processes of Compostable and Biodegradable Plastics
The production processes of compostable and biodegradable plastics are basically the same. The difference mainly lies in the raw materials and additives they use.
Material Selection
Usually, these materials are required: Base Resins, Additives, Pigments, Fillers, Auxiliaries, Compatibilizers and Degradation Promoters.
Here are some commonly used materials:
Base Resins: PLA (Polylactic Acid), PHA (Polyhydroxyalkanoates), PCL (Polycaprolactone), PBS (Polybutylene Succinate), and other bio-based or biocompatible polymers.
Additives: Plasticizers, antioxidants, stabilizers, lubricants, etc. (typically used to improve the processing and performance of the final product.)
Pigments: Include both organic and inorganic pigments, such as TiO2 (Titanium Dioxide), carbon black, etc. (used to impart the desired color and appearance to the product.)
Fillers: Renewable or biodegradable fillers such as natural fibers, starch, lignin, etc. (used to enhance the physical properties of the material or reduce cost.)
Auxiliaries: Such as crosslinking agents, blowing agents, antimicrobial agents, etc. (used to enhance specific functions or processing performances of the material.)
Compatibilizers: When blending different types of biodegradable resins, compatibilizers may be needed to improve compatibility between components, ensuring uniform material properties.
Degradation Promoters: In some biodegradable plastics, specific additives may be included to accelerate the degradation process under certain conditions.
Using Twin Screw Extruders for Making Compostable & Biodegradable Plastics
Twin Screw Extruders are usually used for making compostable and biodegradable plastics due to their excellent performance in the uniform melting and mixing of raw materials.

Twin Screw Extruders for Making Compostable & Biodegradable Plastics >>
Material Melting, Mixing & Compounding
All the materials will be sent into the extruder barrel through the hopper. In the barrel, materials are compressed, sheared by the rotation of dual screws, and finally turned into the required molten composite. Different screw types will be chosen to achieve different results.
Different Dual Screw Types
In the production of compostable and biodegradable plastics, different types of extruder screws each have their unique advantages. Here are some examples and brief explanations
1. Co-rotating twin-screw extruder
Co-rotating twin-screw extruder, specially designed for better mixing effects and higher shear force, is commonly used for biodegradable plastics production, for example Polylactic Acid (PLA).
2. Counter-rotating twin-screw extruder
The counter-rotating twin-screw extruder is suitable for producing biodegradable plastic sheets, especially those materials that require high melt pressure and temperature stability. However, in applications where the mixing effect requirements are not very stringent and there is minimal filler content, counter-rotating twin-screw extruder is capable of offering a more stable melt flow and uniform mixing effects.
3. Intermeshing twin screw exturder
Intermeshing twin screw extruder is generally used in applications requiring high shear force and mixing effects, such as the production of some bio-based biodegradable plastics.
4. Non-intermeshing twin screw exturder
Non-intermeshing twin screw exturder is suitable for materials that do not require high shear force but need stable conveyance and mixing, as well as for materials that are more sensitive to temperature.
Extrusion
The molten composite melt is extruded through the die head of the extruder to form the sheet or granules.
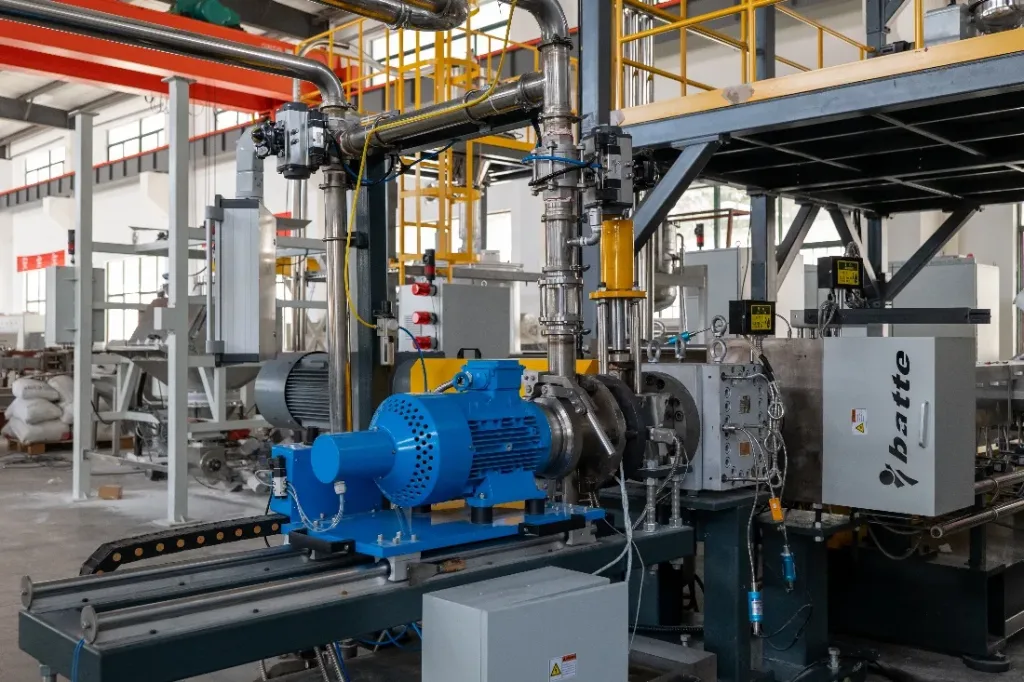
Compostable & Biodegradable Plastic Underwater Pelletizing System

Air-Cooled Conveyor Belt
Cooling and Pelletizing
The extruded biodegradable material needs to be cooled. The cooling method can be air cooling or water cooling. The cooled material is usually in the form of strips or pellets. Then, the material is cut into pellets of the required size by a pelletizer for easy storage and further processing.
Degradable material granulation
Under normal circumstances, when the production volume is low or the filler content is high, air-cooling is used to cool the strands. This is because fully biodegradable materials are hydrophilic, and using water cooling might result in the granules containing too much moisture, which could affect product quality. Of course, for higher automation levels and larger production volumes, we can use underwater pelletizing. The advantage of underwater pelletizing is its high degree of automation, requiring minimal manual operation and produces aesthetically pleasing and beautiful granules. However, subsequent high-power drying equipment must be invested to thoroughly dry the granules, followed by vacuum packaging for bagging.
One-Step Forming Sheets
For the disposable biodegradable products such as meal boxes and water cups used in the catering market, Granuwel has developed a one-step sheet extrusion equipment. This equipment integrates the excellent mixing capabilities of parallel co-rotating twin screws with the stable extrusion pressure provided by a melt pump, combined with a specialized T-die suitable for biodegradable materials to directly extrude sheets in one step. Compared to the traditional process of first using flat twin screws for compounding and granulating, followed by single-screw melting and forming to extrude sheets, the advantages of this equipment are:
- It avoids the secondary melting that may occur when materials are granulated and then melted again, which can lead to performance degradation and the risk of material overheating and decomposition.
- It reduces the investment cost in equipment and lowers the energy consumption during operation.

Compostable & Biodegradale Plastic Sheet Extrusion Production Line

Compostable & Biodegradable Plastic Sheet Extrusion Line
The Differences Between Compostable Extruders and Biodegradable Plastic Extruders
Temperature Control
- Compostable/Biodegradable Plastic Extruders: Require more precise temperature control as these materials are sensitive to heat; excessive temperatures can cause material degradation or performance issues.
- Conventional Industrial Plastic Extruders: Also need temperature control, but the range is broader and less sensitive compared to compostable/biodegradable plastics.
Screw Design
- Compostable/Biodegradable Plastic Extruders: Screw design may need special consideration for the material’s melting and mixing characteristics. Certain screw types (like separating, shearing, dividing) might be more suitable for processing these materials.
- Conventional Industrial Plastic Extruders: Although diverse in screw design, they are mainly optimized for traditional plastics.
Material Compatibility
- Compostable/Biodegradable Plastic Extruders: Must ensure compatibility with the specific compostable or biodegradable plastics used to avoid damaging the equipment or affecting product quality.
- Conventional Industrial Plastic Extruders: Also consider material compatibility, but since they handle a wide range of traditional plastics, the compatibility requirements are generally lower.
How Much Does It Cost to Make Biodegradable Plastic/Compostable Plastic?
The cost of making biodegradable plastic varies based on raw materials, production equipment, process, and scale. Factors like additives, energy, and location also influence costs.
The cost of twin screw extruders?
For instance, a 200kg capacity degradable pelletizer could be priced around $40,000 USD. It is important to note that these figures are approximate and can fluctuate based on specific requirements and market conditions.
Feel free to contact Granuwel, if you intend to purchase high quality extruders for making compostable & biodegradable plastics.