Innehållsförteckning
VäxlaIntroduktion
Extruders are mechanical devices that use heat, pressure, and mechanical shear to process materials. Twin screw extruders, as the name suggests, consist of two intermeshing screws within a barrel. These screws rotate in the same direction, creating a kneading and mixing action to facilitate material processing.
Intermeshing Twin Screw Extruder

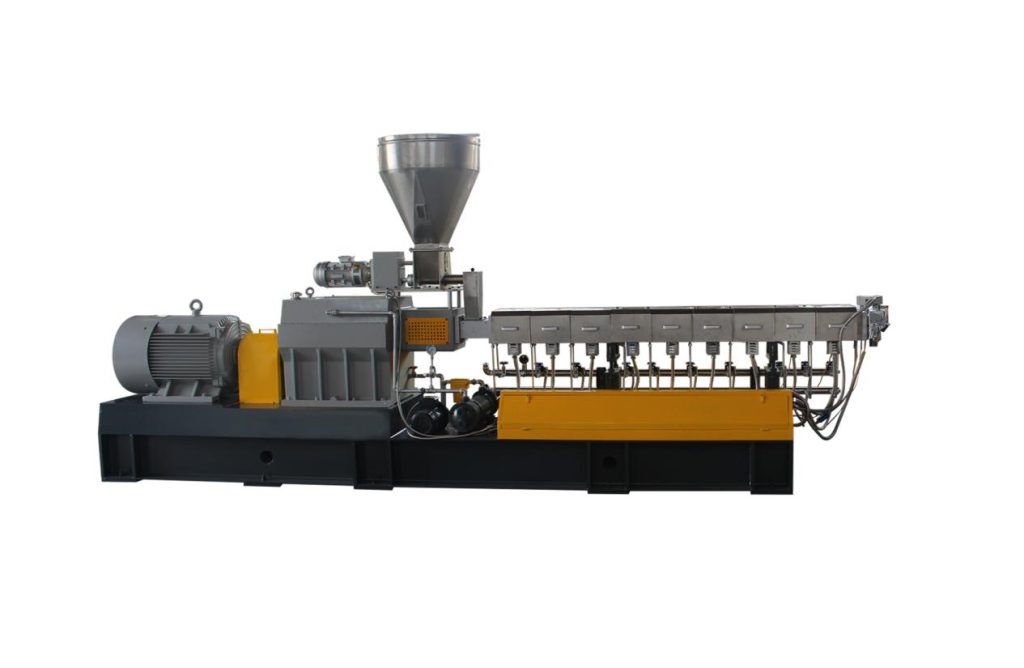
In contrast to non-intermeshing twin screw extruders, intermeshing twin screw extruders have screws that closely mesh together within a single barrel. This design allows for intense interlocking action, enhancing mixing and distributive capabilities.
Intermeshing Twin Screw Extruder Application
Intermeshing twin screw extruders are widely used in industries where efficient mixing, compounding, and dispersion are required. The screws in an intermeshing twin screw extruder have a complex profile with interlocking elements, allowing for greater material processing capabilities.
- Polymer Compounding
- Masterbatch Production
- Blending and Alloys
- Rubber Processing
- Food and Feed Processing:
- Pharmaceutical and Nutraceutical Manufacturing
Intermeshing Twin Screw Extruder Advantage
- One of the key advantages of intermeshing twin screw extruders is their excellent self-wiping ability. As the screws rotate, the intermeshing elements scrape against each other, ensuring that the material is consistently mixed and distributed throughout the process. This results in improved product quality and uniformity.
- Introducing additives, fillers, or reinforcing agents into the material is also easier with intermeshing twin screw extruders.
- The interlocking screws provide sufficient pressure and shear forces to disperse these components uniformly within the matrix, leading to enhanced material properties.
The design of intermeshing twin screw extruders enables a wide range of applications across various industries. They are commonly used in the plastics industry for compounding polymers with additives, creating masterbatches, and producing blends. Additionally, intermeshing twin screw extruders find applications in the food industry for mixing ingredients, extruding dough, and processing meat and fish products.
In the field of pet feed for kinds of proteins, carbohydrates,axunge/fat etc compounding and dispersion;
In the field of polymerization reaction for monomer polymerization, devolatilization and other physical or chemical reactions.
Key components of an intermeshing twin screw extruder
The key components of an intermeshing twin screw extruder include the barrel, screws, drive system, and control panel.
Barrel and screw shaft through precision machining, to ensure that the accuracy of the design requirements, to ensure the uniform distribution of materials, efficient processing.The barrel is equipped with heating and cooling zones to control the temperature during the extrusion process. The drive system provides the necessary power and torque to rotate the screws, while the control panel allows for precise adjustment of parameters such as screw speed, temperature, and pressure.
Non-Intermeshing Twin Screw Extruder
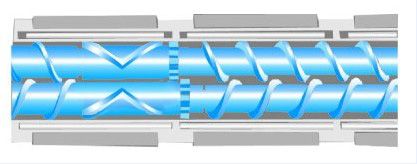
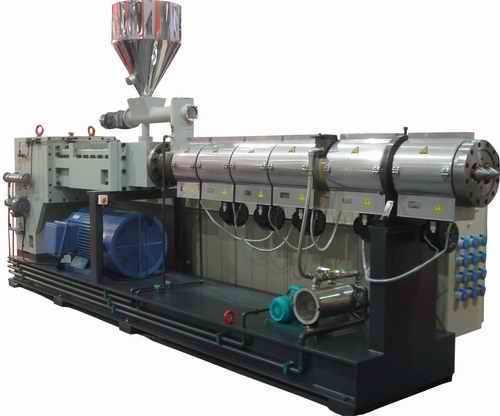
A non-intermeshing twin screw extruder, also known as a parallel twin screw extruder, features two screws that do not come into direct contact with each other. Instead, they rotate side by side within separate barrels. Each screw has its own distinct channel, allowing for independent control of material flow and processing conditions.
Non-Intermeshing Twin Screw Extruder Advantage
The non-intermeshing twin screw extruder offers several advantages in specific applications.
- Firstly, it allows for precise control over temperature, residence time, and shear rates, making it suitable for processing heat-sensitive materials.
- Secondly, the absence of direct screw contact reduces the wear and tear on components, resulting in longer machine life.
- Lastly, this type of extruder is often used for devolatilization processes in the polymer industry, where volatile compounds need to be removed.
Key components of a non-intermeshing twin screw extruder
Key components of a non-intermeshing twin screw extruder include the barrels, screws, drive system, and control panel. The screws can be co-rotating or counter-rotating, depending on the desired processing requirements. Additionally, the extruder may feature various feeding mechanisms, such as gravimetric or volumetric feeders, to ensure consistent material intake.
Non-intermeshing Twin Screw Extruder Application
- Polymer Devolatilization
- Heat-Sensitive Materials
- Compounding and Blending
- Speciality Polymer Production
- Pharmaceutical Processing
- Food Processing
Comparison between Non-Intermeshing and Intermeshing Twin Screw Extruders
Both non-intermeshing and intermeshing twin screw extruders offer unique advantages and are suitable for specific applications. To better understand their differences, let’s compare them across several aspects:
Performance and Efficiency
Introducing heading 3 to display the outline structure.
Non-intermeshing twin screw extruders excel in applications where precise control over processing conditions is crucial. They offer excellent temperature control, residence time distribution, and shear rates. This makes them ideal for processing heat-sensitive materials and achieving specific product properties. On the other hand, intermeshing twin screw extruders are known for their superior mixing capabilities. They provide intense shearing and dispersive forces, resulting in improved homogeneity and dispersion of additives or fillers.
Processing Capabilities
Non-intermeshing twin screw extruders are often favoured when devolatilization or reactive extrusion processes are required. The independent channels of the screws allow for better control over these processes. Intermeshing twin screw extruders, on the other hand, are highly efficient in compounding and blending applications. Their interlocking screws ensure excellent distributive mixing, making them suitable for achieving uniform dispersion of additives or creating speciality compounds.
Material Compatibility
Both types of extruders are compatible with a wide range of materials, including plastics, rubbers, food ingredients, and pharmaceutical compounds. However, the choice of extruder depends on the specific material and desired processing requirements. Non-intermeshing twin screw extruders are often preferred for heat-sensitive materials or processes requiring precise temperature control and shear. Intermeshing twin screw extruders are commonly used for compounding, blending, and achieving superior mixing performance.
Maintenance and Cost Considerations
Maintenance requirements and costs can vary between non-intermeshing and intermeshing twin screw extruders. Non-intermeshing twin screw extruders typically have fewer wear parts due to the absence of direct screw contact. This can result in reduced maintenance needs and longer machine life spans. On the other hand, intermeshing twin screw extruders have complex screw profiles with interlocking elements, which may require more frequent maintenance and replacement of wearing parts. The cost of non-intermeshing twin screw extruders may be higher initially due to their precise control capabilities, while intermeshing twin screw extruders are often favored for their excellent mixing performance and versatility.
In conclusion, non-intermeshing twin screw extruders and intermeshing twin screw extruders offer distinct advantages in different applications. Non-intermeshing twin screw extruders provide precise control over processing conditions and are suitable for devolatilization and reactive extrusion. Intermeshing twin screw extruders excel in mixing, compounding, and achieving uniform dispersion of additives. The choice between the two depends on the specific material, processing requirements, and desired outcome.