Innehållsförteckning
VäxlaIntroduktion:
In modern manufacturing, the application of heat-sensitive plastics is becoming increasingly widespread due to their unique physical and chemical properties, making them an ideal choice for numerous industrial sectors. However, the processing of heat-sensitive plastics poses significant challenges because they easily degrade and discolor under high temperatures. These characteristics make it difficult to meet production requirements using traditional processing technologies. The molecular structure of heat-sensitive plastics can break down easily in high-temperature environments, leading to reduced material performance, such as discoloration and weakened strength. Traditional single-screw extruders exhibit limitations when plastifying heat-sensitive plastics, particularly in shear force delivery and temperature regulation. This often results in uneven plastification or excessive degradation of the material, thereby affecting product quality, consistency, and increasing scrap rates and costs. To address this challenge, twin-stage extruders offer an efficient solution. Comprised of a GTE type high-speed co-rotating twin-screw mixer and a GDS series low-speed single-screw extruder, these two parts are vertically arranged orthogonally, working together to achieve efficient plastification and uniform mixing while avoiding overheating degradation issues. The following text will delve deeper into the technical characteristics, application examples, and optimized usage strategies of twin-stage extruders in the processing of heat-sensitive plastics, fully showcasing their innovative potential and wide application prospects in modern processing technology, especially how through their unique dual-stage design and process decomposition, independent control and optimization of each processing step are achieved, enhancing production efficiency and material utilization rate.
Challenges in Processing Heat-Sensitive Plastics:
- Heat-sensitive plastics are prone to chemical and physical changes under high temperatures, posing significant challenges to their processing. When exposed to high-temperature environments, their molecular structure begins to change, leading to a severe reduction in their physical properties. High temperatures can accelerate the breakage of polymer chains, causing a decrease in molecular weight, which in turn affects the mechanical strength and chemical stability of the material. For heat-sensitive plastics like polyvinyl chloride (PVC) and polyoxymethylene (POM), not only does discoloration occur, but harmful gases may also be released, affecting not only the quality of the final product but also potentially polluting the production environment.
- Traditional single-screw extruders have obvious limitations when processing these materials. Due to their design constraints, single-screw extruders cannot provide sufficient shear force to ensure uniform plastification of heat-sensitive plastics. Additionally, these machines usually employ electric heating with external surface ventilation cooling, so temperature control is not precise enough, easily resulting in overheating areas during processing, thereby causing local or comprehensive degradation of the material. Since heat-sensitive plastics need to be processed at lower temperatures and with precise shear rates, these shortcomings of single-screw extruders become bottlenecks in improving product quality and production efficiency.
- Using traditional technology to process heat-sensitive plastics often leads to inconsistent product quality and increased scrap rates. Uneven plastification and material degradation can cause instability in the final product’s performance, increasing production costs and reducing a company’s market competitiveness. These issues highlight the necessity of seeking more advanced and precise processing technologies. To overcome these challenges, the application of twin-stage blending units has become a breakthrough in the field of heat-sensitive plastic processing. Its structural features include: the first stage uses a GTE type high-speed co-rotating twin-screw machine for mixing in an open barrel with almost zero pressure, and the second stage is a GDE low-speed single-screw extruder that extrudes the mixed and matured material at low speed and temperature, thus avoiding thermal degradation and precisely controlling and optimizing blending effects. The twin-stage machine not only improves product quality but also significantly reduces scrap rates, bringing significant economic and technical benefits to manufacturing enterprises.

Technical Features of Nanjing Granuwel Twin-Stage Extruder:
- The first stage is a GTE type high-speed co-rotating twin-screw mixer, and the second stage is a GDS series low-speed single-screw extruder, both vertically arranged orthogonally to form a dual-stage compound unit. This design combines the advantages of twin-screw and single-screw, achieving efficient plastification mixing and shear dispersion while avoiding contradictions between high shear overheating and high-pressure extrusion.
- The twin-screw enforces conveyance, ensuring uniform mixing and plastification of the material during processing. Its unique screw structure promotes better mixing effects, allowing heat-sensitive plastics to be heated and mixed evenly. The geometric shape and configuration of the screw are carefully calculated to maximize its shear and distribution effects on the material, thereby improving material fluidity and processing efficiency.
- The single screw performs high-pressure extrusion but adopts a low-speed, low-shear method, equally avoiding overheating contradictions. This design enables the twin-stage extruder to maintain product quality while improving production efficiency and reducing production costs.
- The combination of twin-screw and single-screw breaks down the process functions, increasing independent operating variables, which is conducive to stepwise optimization of each process. This multifunctionality not only guarantees product quality but also enhances production efficiency and reduces production costs.
- The twin-stage extruder is widely used in various heat-sensitive material systems and large-capacity devolatilization operations, such as PVC, XLPE, halogen-free flame-retardant cable materials, shielding materials, high concentration carbon black materials, and post-processing operations after rubber dehydration. By simplifying the operation process and improving material utilization, the twin-stage extruder provides a cost-effective solution for manufacturing enterprises, fully meeting the needs of modern manufacturing.
Proper granulation methods can also reduce the risk of overheating for heat-sensitive materials. However, due to PVC’s tendency to absorb water, air-cooled hot cutting is generally used; most heat-sensitive materials should adopt water ring or underwater granulator methods: Water ring Pelletizing systems and Underwater Pelletizing systems work well with twin-stage extruders in processing heat-sensitive plastics. Through effective cooling mechanisms, they ensure the stability of sensitive materials during processing, reducing material degradation problems caused by high temperatures.
Water Ring Pelletizing System:
At the point where the plastic strip is cut, water is sprayed to form a circular water band. This water band not only surrounds the freshly cut plastic strip but also rapidly cools the material through the quick cooling effect of water. This rapid cooling process is crucial for heat-sensitive plastics because it prevents the material from being exposed to high temperatures for too long, thereby protecting the physical and chemical properties of the material from being affected. An additional advantage of water ring granulation is its relatively simple operation, low maintenance costs, and ability to accommodate plastic strips of different sizes and shapes, offering an economical and effective solution.
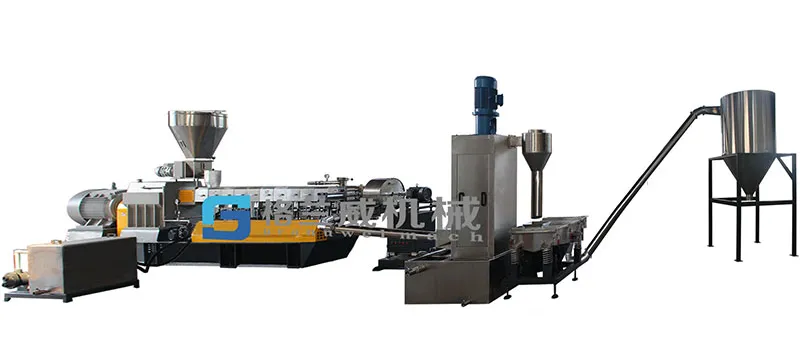
Underwater Pelletizing System:
The cutting process of the plastic strip is completely carried out underwater. When the plastic strip is cut, it directly falls into the water. The water not only acts as a cooling medium but also transports the cut particles to the next processing step. The greatest advantage of this method is its extremely rapid removal of generated heat from sensitive materials, almost completely eliminating the risk of material damage caused by overheating. Underwater granulation ensures the preservation of material characteristics, especially suitable for heat-sensitive plastics that are highly susceptible to temperature. Although underwater pelletizing systems may require more complex equipment and higher initial investments, their long-term benefits in maintaining product quality and reducing scrap rates are significant.

Application Examples:
In the field of processing heat-sensitive plastics, the application of twin-stage extruders is becoming increasingly widespread, with its advantages particularly evident when handling materials such as polyvinyl chloride and polyoxymethylene. For example, enterprises focusing on the production of PVC cable materials face issues of low production efficiency and unstable product quality. By introducing twin-stage extruders, enterprises not only significantly increase the output of PVC cable materials but also reduce material degradation issues caused by excessive temperatures. The precise temperature control and uniform mixing capabilities of twin-stage extruders ensure the quality consistency of PVC cable materials while reducing scrap rates and enhancing overall production efficiency.
Case studies show that twin-stage extruders not only optimize the processing process and increase output when handling heat-sensitive plastics like PVC and POM but also ensure product quality consistency through precise process control. This represents a huge technical and economic benefit for production enterprises pursuing high-quality standards.
Slutsats:
With its research and application in the field of heat-sensitive plastic processing, Granuwel’s twin-stage extruder has become a reliable piece of equipment that greatly improves the production process and product quality. Through precise control of temperature and shear rate, the twin-stage extruder solves many challenges encountered by traditional single-screw extruders when processing heat-sensitive plastics, such as material degradation, uneven mixing, and low production efficiency. This technological advancement not only enhances the processing efficiency of heat-sensitive plastics but also ensures high standards in product color, strength, and consistency.
Manufacturing enterprises have gained significant economic and competitive benefits from adopting twin-stage extruder technology. Cost savings are reflected in reduced material waste, lower energy consumption, and decreased maintenance expenses. Meanwhile, due to improved product consistency and quality, enterprises can enhance their products’ market competitiveness, attract more customers, and expand market share. These direct and indirect economic benefits make the twin-stage extruder an essential piece of equipment for any enterprise committed to improving production standards and profitability.
As concern for environmental protection and sustainable production continues to grow, future twin-stage extruders will also focus more on optimizing energy efficiency and material utilization rates. Moreover, with the development of emerging markets and diversification of industrial demands, twin-stage extruders will adapt to a wider range of materials and application fields, making greater contributions to innovation and development in global manufacturing.