Innehållsförteckning
VäxlaTwin screw extruder uses for processing ordinary high-gloss powder
Application of high-gloss powder in plastic industry
High-gloss powder is a powder additive that can be added to plastics to increase the brightness of products and improve the appearance and texture. The principle of high-gloss powder is to use the diffuse scattering of light to modify small flaws in plastic products rather than just relying on pure Covering can improve the appearance of the product. To produce a glossy effect, the most commonly used high-gloss powder in the plastics industry is barium sulfate. A certain proportion of barium sulfate is added to the plastic modification to make the product shiny and improve the strength, stiffness and wear resistance of plastic products.
When processing ordinary high-gloss powder masterbatch, we need to pay attention to two points, for the twin-screw extruder: one is the actual effect of mixing, and the other is to ensure that the powder is not agglomerated and evenly dispersed in the plastic carrier.
At this stage, all the twin-screw extruders are suitable for the production and processing of high gloss powder as long as they are qualified products.
In order to ensure (improve) the mixing effect, in the arrangement of the extruder screw combination, the location of the mixing section, the gap between the two screws, the degree of wear of the thread element, the setting of the barrel temperature, and the precision of the temperature control will affect the dispersion of the highgloss powder in the plastic granulation.
Considerations for twin screw extruders uses in the processing of standard high gloss powder masterbatchinclude the following points.
Raw material selection-twin screw extruders uses
The selection of high-quality raw materials is very important for the production of high gloss powder.
Selection of raw materials: The selection of high-quality raw materials is crucial for the production of high gloss powder masterbatch.
Ensure that the quality of raw materials conforms to the product specifications to avoid the mixing of impurities and contaminants.
Extruder parameter setting-twin screw extruders uses
Adjust the operating parameters of the twin-screw extruder, including temperature, pressure and speed, etc., to ensure that the ideal product performance and appearance are obtained during processing.
Temperature control-twin screw extruders uses
Controlling the temperature of the extruder is a key step. Ensure that the temperature of the screw and barrel is moderate to avoid material degradation caused by too high temperature or too low temperature affecting the extrusion effect.
- Setting of regulating temperature in melting zone-twin screw extruders uses
- We suggest that the set temperature T of the melting zone should be linked to the extruder screw aspect ratio i and rotation speed n: n≤200rpmT≈120℃, n=200-350rpmT≈140℃, n=500-800rmpT≈140℃n=500 -800rpmT≈150℃ When i=18, reduce by 5℃; when i≥20, reduce by 10℃.
- Cooling water temperature control
Due to the self-cleaning nature of the twin-screw extruder, the gap between the screws is small. The material in the barrel cavity will increase the internal friction due to the drag force between the melts, causing the internal temperature of the material to rise significantly. Fast, and the heat accumulates to the peak in the extrusion section. Therefore, the temperature setting of the twin-screw extruder changes from rapid heating at the feed port to rapid cooling in the extrusion section, so the control requirements for cooling water are stricter. Otherwise, the dispersion of the masterbatch will be affected because the material temperature is too high.
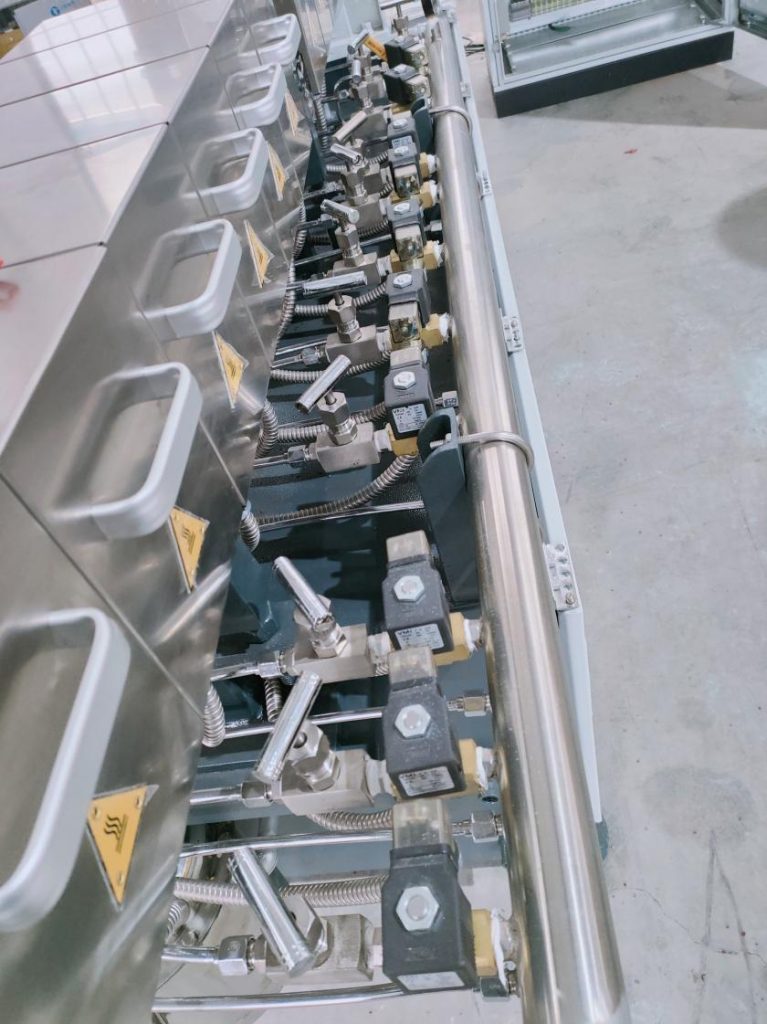
Therefore, each section is equipped with an independent cooling pipeline. The solenoid valve controls the inlet and outlet of the cooling water, and the throttle valve controls the flow of cooling water. During the process of opening and closing the solenoid valve, precise control of the temperature is achieved. It puts forward very high requirements on the quality and life of solenoid valves. Usually, the ideal temperature control range is +-2°C. If the temperature difference adjustment range exceeds 10°C, it will be difficult to ensure the actual mixing effect.

The accuracy of temperature regulation depends on the flow rate and temperature rise of cooling water. The larger the flow rate is and the smaller the temperature rise is, the higher the accuracy is.
And the cooling water of the machine barrel should be soft water (small circulation).
Normally, high-temperature water will form dirt in the flow channels of the cylinder. Over time, the cooling flow channels of the cylinder will be blocked. In order to facilitate maintenance and temperature control, we are equipped with a special cooling water tank. In the water tank, we require customers to add softened water or Distilled water to prevent clogged water channels. The water in the water tank passes through a high-temperature-resistant water pump and is pumped to the main pipeline, where it is then diverted to each cylinder through solenoid valves. Therefore: each cylinder is an independent temperature control unit, which forms a closed cooling system through a temperature control meter or temperature control module solid state relay, main water inlet pipe, main return pipe, solenoid valve, flow valve and other pipe joints. unit, the hot water returned from each temperature control zone is collected and returned to the water tank through the plate heat exchanger.
- Solidified particles
There are many factors that cause the formation of solidified particles. It is a comprehensive factor, which is not only related to the mixture of formula and component quality and even batch, but also related to the performance of ACM mill, such as excessive heating of grinding cavity and so on.
For the twin screw extruder, the first reason is that the clearance in each part of the screw is too small or too large, the friction increases when the screw is small, and the local temperature is too high, which leads to the curing of the material at low temperature due to the loss of self-cleaning ability.
On the other hand, the setting temperature of each zone is unstable, especially in the discharge area, the specific temperature in operation far exceeds the set temperature, or the discharge port accumulates for a long time, which will cause low temperature curing.
Therefore, there are three key conditions for the production and processing of high gloss powder masterbatch:
- Perfect formula and high-quality ingredients
- It is a machine with excellent technical parameters and superior performance.
- It is a skilled manipulation technique.
Day-long maintenance and precautions for high-gloss powder masterbatch production equipment
1. Screw speed: Adjust the screw rotation speed to ensure that the raw materials are fully mixed during the extrusion process and to maintain uniform extrusion.
2. Cleaning and maintenance of the extruder: Clean the extruder regularly to prevent residues from affecting product quality. Regularly inspect the screw, barrel and other critical components to ensure they are operating properly.
3. Product cooling: After extrusion, the product is properly cooled to ensure that there is no moisture residue on the surface of the high-gloss powder masterbatch, and to reduce energy loss caused by subsequent drying.
4. Quality control: Implement strict quality control measures, including sampling testing of extruded products, to ensure that products meet specifications and customer requirements.
5. Safety production: During the processing process, relevant safety operating procedures must be followed to ensure the safety of operators and equipment.
Through the above precautions, the production efficiency and product quality of ordinary high-gloss powder processed by a twin-screw extruder can be effectively improved.
If you want know more about high-gloss powder masterbatch production, welcome to contact us for further information.
Om oss
Nanjing Granuwel Machinery CO., LTD är specialiserat på FoU-design och tillverkning av högpolymerextruders, vårt team av extruderingsproffs på högsta nivå tillhandahåller rätt extruder för din exakta applikation.
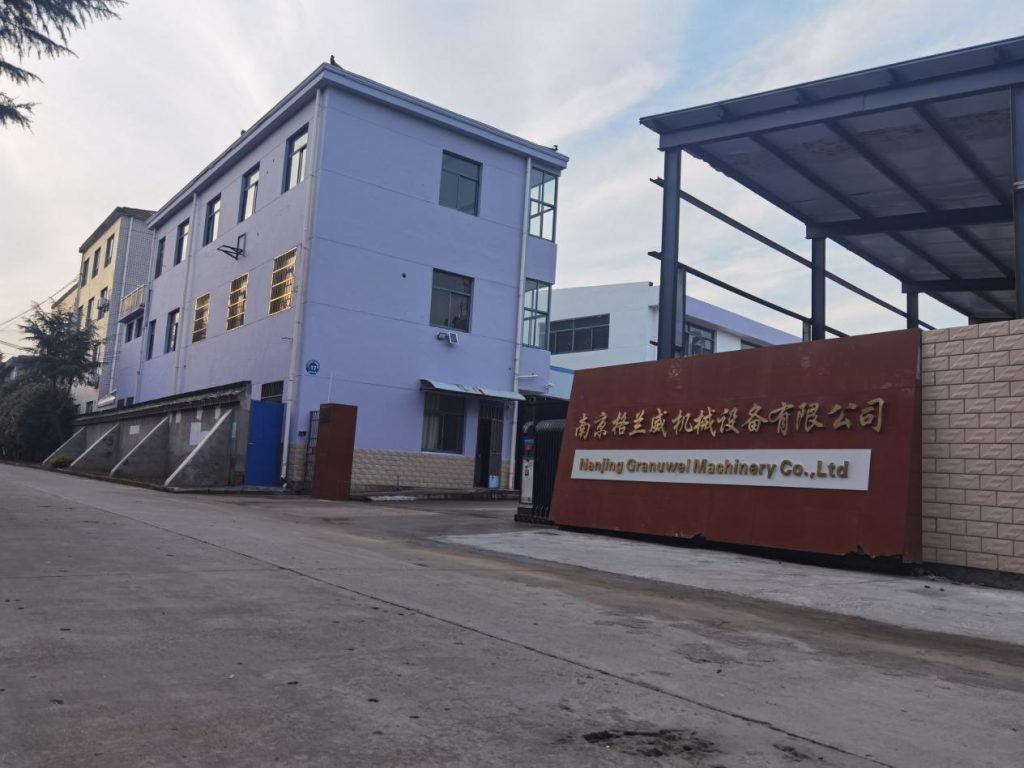
Vi har utmärkt innovations- och produktutvecklingsförmåga och önskar att tillhandahålla de bästa produkterna för våra kunder genom att förbättra utrustningens struktur och minska utrustningens energiförbrukning genom våra praktiska erfarenheter och tekniska innovationer.
För någon fråga eller förfrågan, varmt välkommen att kontakta oss!!!
Tel: +86-25-86199956
Mobil: +86-13813371123
E-post: [email protected]
Web: https://toolant.net