Table of Contents
Toggleco-rotating VS counter-rotating
In the counter-rotating twin screw extruder, the raw material is transported in a positive displacement similar to that in a gear pump. The speed of the Counter-rotating is lower and the raw materials shear heat is small, raw materials are not easy to decompose, thus it is not high requirements for the thermal stability of raw materials, especially suitable for heat sensitive raw materials (such as PVC) forming production and processing. Compared with the co-rotating twin screw extruder, the counter-rotating twin screw extruder has higher conveying efficiency, better exhaust effect and melting effect.
Although the dispersing mixing effect of raw materials is worse than that of the co-rotating twin screw extruder, but the ability to create a stable head pressure is stronger, so it is more suitable for extrusion products directly. In addition, the use of counter-rotating twin screw extruder instead of single screw extruder can eliminate the process of preplasticizing granulation and directly extrusion and processing of PVC powder, which reduces the cost of products. The counter-rotating twin screw extruder is mainly used for extrusion PVC pipes,profiles, plates and granulation. Parallel counter-rotating twin-screw extruders have also been applied in large – scale pipe production lines.

The co-rotating twin screw extruder has the advantages of high conveying efficiency, strong dispersion and mixing capabilities, good self-cleaning performance, uniform residence time distribution of materials in the machine, and good adaptability. It is more suitable for other applications, such as compounding, mixing, devolatilization, and chemical reactions, such as blending modification between different plastics, between plastics and rubber, blending of various additives with plastics, glass fiber, carbon fiber reinforced plastics, and continuous mixing of polymer modification.
The co-rotating twin screw extruder is rarely used in extrusion products, if you want to extrude products by co-rotating twin screw extruder, a single screw or gear pump can be matched with to increase stability, higher extrusion pressure, to ensure the quality of the product extrusion. The Starch-based 100% degradation material is very popular in the present market.The sheet extrusion of the packaging box is directly extruded through parallel co-rotating twin screw with gear pump in the same direction.The advantage of such method is to set the material blending modification and product molding in one machine, effectively lower production and processing costs, avoid the influence of secondary melting after material performance.
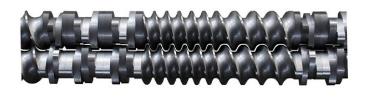
single screw VS twin screw
Applications:
- Pipe extrusion
- Sheet extrusion
- Profile extrusion
- waste plastic recycling granulation
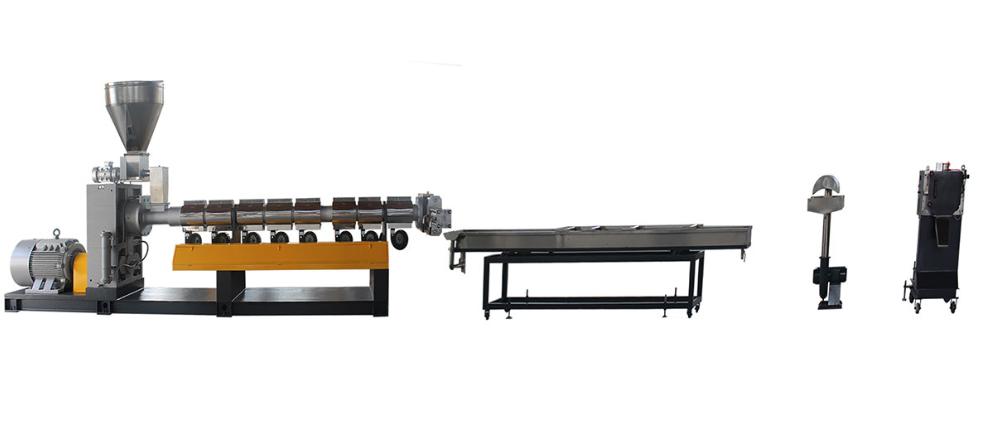
The twin screw extruder has good mixing and plasticizing ability, and the residence time of material in the extruder is short, so it is suitable for powder processing. Twin screw is mainly used for modification and compounding blending of various plastics, as to its screws and barrels adopt building block structure, which can adjust the screws structure according to the production material, can achieve a multi-purposes machine. The twin screw extruder with the advantages of low energy consumption and high production efficiency.
Applications:
- Foam extrusion
- PET extrusion
- Reacting extrusion
- Compounding extrusion

About us
Nanjing Granuwel Machinery CO., LTD is specializing in R&D design and manufacture of high polymer extruders, our team of top-level extrusion professionals provides the right extruder for your exact application.
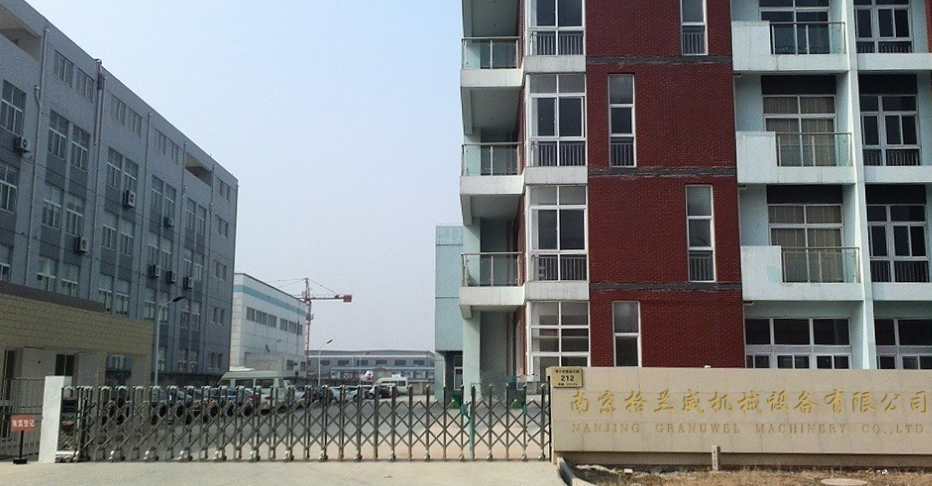
Nanjing Granuwel Machinery CO., LTD
We possess excellent capability of innovation and product development, and desire to provide best products for our customers through the improvement of equipment structure and reduction of equipment energy consumption through our practical experiences and technical innovation.
For any question/inquiry,warmly welcome to contact us!!!
Tel: +86-25-86199956
Mobile: +86-13813371123