Table of Contents
ToggleWhat is degradable polymer masterbatch extrusion and pelletizing equipment?
Degradable polymer masterbatch extrusion and pelletizing equipment refers to specialized machines used in the production of degradable polymer masterbatches, which are concentrated mixtures of degradable additives and polymers.

What is degradable masterbatch?
The degradable masterbatch refers to small granules of a concentrated mixture of biodegradable additives during manufacturing to accelerate its degradation under certain environmental conditions. In order to reduce costs, a certain proportion of CaCO3, corn starch and other inorganic substances are heated in this masterbatch formula. At the same time, due to the characteristics of corn starch and CaCO3, they will accelerate the degradation of plastic products. The amount of addition varies from 15-60% depending on the final product.
Types of degradable masterbatch
Biodegradable Masterbatch:
Enhances the biodegradability of plastics, allowing them to be broken down by microorganisms into natural substances like water, carbon dioxide, and biomass.
Key components of biodegradable masterbatch include:
- Base Polymers: PE, PP, PS.
- Photodegradable Additives: UV absorbers, photooxidants, metal stearates.
- Blending Agents: Compatibilizers, plasticizers.
- Functional Additives: Antioxidants, stabilizers, colorants.
- Filler: CaCO3 corn starch, etc.
Used in agricultural films, packaging, and outdoor products to reduce plastic waste through light-induced degradation.
Photodegradable Masterbatch:
Contains additives that promote degradation when exposed to sunlight, typically UV light.
Key components of photodegradable masterbatch include:
- Base Polymers: Polyethylene (PE), Polypropylene (PP), Polystyrene (PS).
- Photodegradable Additives: UV absorbers, photooxidants, and prodegradant additives (e.g., metal stearates).
- Blending Agents: Compatibilizers and plasticizers for uniform dispersion and enhanced processability.
- Functional Additives: Antioxidants, stabilizers, and colorants.
- Filler: CaCO3 corn starch, etc.
These materials are used in applications like agricultural films, packaging, and outdoor products to reduce plastic waste by accelerating degradation under light exposure.
Oxodegradable Masterbatch:
Uses additives that accelerate oxidation and fragmentation of plastics when exposed to heat and oxygen, eventually breaking down into microplastics which are then biodegraded by microorganisms.
Key components of oxodegradable masterbatch include:
- Base Polymers: PE, PP, PS.
- Oxodegradable Additives: Metal stearates, prodegradant additives.
- Blending Agents: Compatibilizers, plasticizers.
- Functional Additives: Antioxidants, stabilizers, colorants.
- Filler: CaCO3 corn starch, etc.
Used in packaging, agricultural films, and disposable products to reduce plastic waste through accelerated oxidation and subsequent biodegradation.
No matter what type of degradable masterbatch you need to produce, our extrusion and pelletizing production line can help you achieve efficient and high-quality production
No matter what type of degradable masterbatch you need to produce, Granuwel extrusion and pelletizing production line can help you achieve efficient and high-quality production.
How is degradable masterbatch made?
Degradable masterbatches are made by degradable masterbatch extrusion and pelletizing lines, as shown in the picture below.

The production involves several key steps, from the selection of raw materials to the final extrusion and pelletizing process. Here’s a detailed breakdown of how degradable masterbatches are made:
1. Selection of Raw Materials
- Base Polymer: Commonly used polymers such as polyethylene (PE), polypropylene (PP), or other types of plastic resins.
- Filler: CACO3 powder, corn starch powder, generally mesh size greater than 1250 mesh
- Degradable Additives: These include substances that promote degradation, such as organic compounds, metal stearates, or starch-based additives.
- Other Additives: Depending on the desired properties, other additives like antioxidants, UV stabilizers, and plasticizers may be included.
2. Weighing and Mixing
- Accurate Weighing: The raw materials are accurately weighed to ensure the correct proportions of base polymer and degradable additives.
- Pre-Mixing: The materials are pre-mixed to ensure an even distribution of additives before they enter the extrusion process.

More options: Loss-in-weight metering feeding can be used to automatically feed the twin-screw host according to the formula proportion, thus avoiding environmental pollution caused by dust during the mixing process of the high-speed mixer. It can also reduce the labor intensity of workers. But it must be noted: CaCO3 and cornstarch must be coated materials.
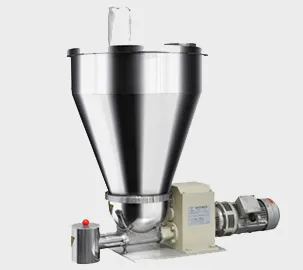
3. Extrusion Process
- Feeding: The pre-mixed materials are fed into the extruder using a feeder system (volumetric or gravimetric).
- Melting and Compounding: Inside the extruder, the materials are heated to melt the base polymer. The screw mechanism mixes the polymer with the degradable additives, ensuring a homogeneous blend.
- Twin-Screw Extruder: Preferred for more complex formulations due to better mixing capabilities.
4. Shaping and Cooling:
- Die Head: The molten mixture is pushed through a die head, shaping it into continuous strands.
- Cooling: The extruded strands are cooled, typically using air cooling systems, to solidify the material. It is recommended to use air-cooled strips and try not to use water cooling. Because the particles will degrade when exposed to water, and because of the one meter of starch, they will absorb water. It has to be dried afterwards.
5. Pelletizing:
Cutting: The cooled strands are cut into uniform pellets using a pelletizer. This can be done using:
- Strand Pelletizer: Cuts the strands after cooling.
- Underwater Pelletizer: Cuts the strands while they are still in the water for more consistent pellet sizes.
6. Drying:
Removing Moisture: The pellets are dried to remove any residual moisture, using methods such as:
- Centrifugal Drying: Uses centrifugal force to remove water.
- Fluidized Bed Drying: Uses hot air to dry the pellets.
7. Sieving and Classification:
- Uniform Size: The pellets are sieved and classified to ensure they are of uniform size and free from any oversized or undersized particles.
8. Quality Control:
Throughout the production process, quality control measures are implemented to ensure that the degradable masterbatch meets the required specifications and performance standards. This includes:
- Testing: Samples are tested for consistency, degradation properties, and other relevant parameters.
- Adjustments: Any necessary adjustments to the formulation or process conditions are made to maintain product quality.
Benefits Of Using Degradable Masterbatches
Environmental Impact: Accelerates plastic degradation, reducing long-term waste accumulation.
Cost-Effective: Provides an affordable solution compared to fully biodegradable plastics.
Versatility: Compatible with various polymers and applications, including packaging and agriculture.
Resource Efficiency: Utilizes renewable resources and reduces reliance on fossil fuels.
Regulatory Compliance: Helps meet environmental regulations and standards.
Enhanced Product Performance: Improves properties like flexibility, strength, and UV resistance.
Brand Image: Enhances sustainability credentials and appeals to eco-conscious consumers.
Waste Management: Reduces costs associated with waste disposal and management.
If you have any other questions about degradable polymer masterbatch extrusion and pelletizing, feel free to contact GRANUWEL MACHINERY.