· John Smith · plastic-granulator · 4 min read
Granulator for PET Flakes:Boosting Efficiency and Quality in Recycling
Discover how a granulator for PET flakes can enhance recycling efficiency and material quality. Learn about its mechanics, benefits, and optimal designs.
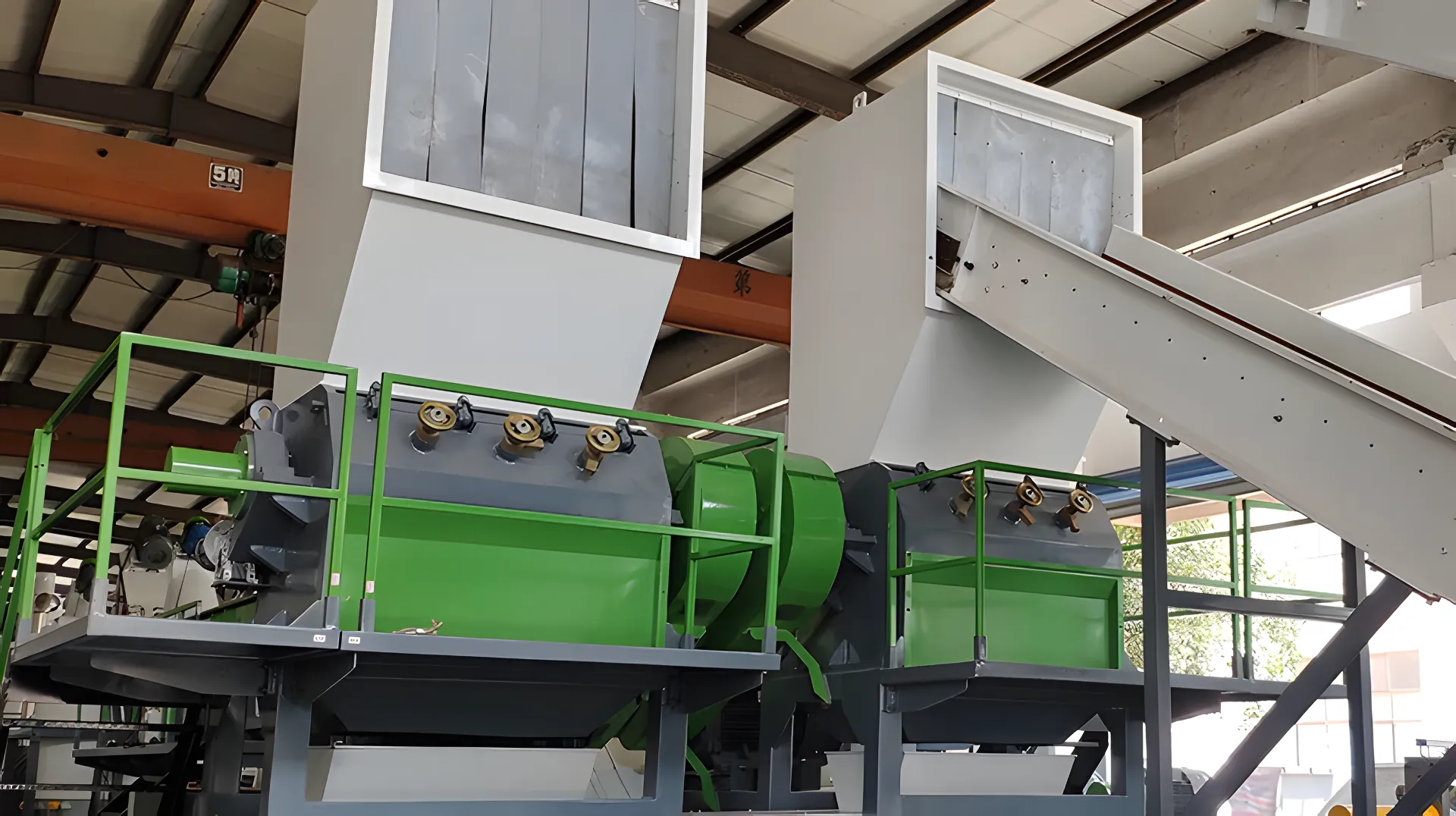
Recycling centers focused on PET (Polyethylene Terephthalate) bottles often grapple with the task of improving both the quality of their recycled materials and the efficiency of their processes. One pivotal piece of equipment that plays a crucial role in this aspect is the granulator, sometimes known as a “crusher”. This article explores the inner mechanics, benefits, and strategic importance of a plastic granulator specifically designed for PET flakes.
How A Plastic Granulator Works
Understanding the mechanics of a plastic granulator helps in appreciating its significance. The core function revolves around two sets of cutting knives located within the cutting chamber. One set, known as “bed knives,” is stationary. The other set, known as “rotor knives,” is mounted on a rotating “open” rotor. When the rotor spins quickly, driven by an electric motor, the rotor knives interact with the bed knives, creating a scissor-like cutting motion.
Optimal Cutting Design
In the industry, the “double-scissor” configuration for the rotor knives represents optimal cutting efficiency. For instance, a well-configured granulator might include 10 rotor knives and 4 bed knives. This setup has been shown to offer the highest efficiency and durability for transforming PET bottles, whether flattened or not, into PET flakes. For recyclers, understanding that flattened bottles can enhance output rates is crucial when planning operations.
At the cutting chamber’s bottom lies a metal screen with multiple holes, typically around 9.5mm in diameter. This screen ensures that the PET flakes remain in the chamber until they are appropriately sized, usually between 12-18mm, before they can pass through.
Post-Granulation Process
Once granulated, the PET flakes are propelled into an air classification system via a blower. This system is vital in filtering and collecting fines and lightweight plastics, such as PP/PE films commonly used in bottle labels. Efficient separation at this stage ensures higher quality PET flakes, contributing to the overall value and usability of the recycled material.
Enhancing Production Efficiency
The meticulous design and maintenance of the plastic granulator significantly affect production efficiency. Here are a few benefits:
- Material Quality: High-quality PET flakes reduce the need for additional processing and improve the end product’s quality.
- Throughput: Optimized cutting reduces downtime and enhances the rate at which bottles can be processed.
- Energy Efficiency: Advanced granulators often consume less power while offering higher performance, reducing operational costs.
Importance in PET Bottle Recycling Lines
For anyone looking to optimize a PET bottle washing line, the plastic granulator stands out as the critical equipment to assess first. Effective granulation not only influences the downstream processes but also dictates the overall efficiency and cost-effectiveness of the recycling line.
Recyclers worldwide recognize that investing in a high-quality granulator can lead to substantial long-term savings and improved output quality. This understanding is supported by various industry studies and general consensus among PET recycling experts.
Maintenance Tips
To maintain the efficiency and longevity of your plastic granulator, consider these tips:
- Regularly inspect and sharpen knives to ensure clean cuts.
- Monitor and replace the screen as needed to maintain proper sizing of PET flakes.
- Lubricate moving parts to reduce friction and wear.
- Check for foreign objects that could damage the equipment.
FAQ Section
What is the purpose of a plastic granulator in PET bottle recycling?
A plastic granulator cuts PET bottles into smaller flakes, optimizing material quality and production efficiency in recycling centers.
How does the double-scissor array benefit PET flake production?
The double-scissor array of rotor knives offers optimal cutting, increases output, and enhances durability, ensuring efficient processing of PET bottles into flakes.
Why are flattened bottles preferred in granulation?
Flattened bottles provide higher output rates as they are easier to cut, leading to more efficient production.
What should be the diameter of holes in the granulator’s screen?
The recommended diameter for the holes in the metal screen is approximately 9.5mm to ensure the proper sizing of PET flakes.
How can I maintain my plastic granulator for longevity?
Regularly inspect and sharpen knives, monitor and replace the screen, lubricate moving parts, and prevent foreign objects from entering the cutting chamber.
What role does the air classification system play post-granulation?
The air classification system filters out fines and lightweight plastics, like PP/PE films, ensuring a higher quality of PET flakes.
Conclusion
In the intricate world of PET bottle recycling, the plastic granulator emerges as a linchpin in optimizing both material quality and production efficiency. Its design, cutting mechanism, and post-process separation capabilities make it indispensable. By maintaining your granulator diligently and understanding its strategic importance, you can significantly enhance your recycling operations. The granulator is more than a machine—it’s a cornerstone in the sustainable management of PET materials.